Abstract
Deep drawing can be defined on the most basic level as a metal shaping process used for shaping flat sheets into cup-shaped articles of different dimensions.
For a successful deep drawing process results there are many factors to consider and in this article we will cover the most important of those including the potential for necessary material characteristics, defects in mass production, and what properties are best measured to indicate a successful deep drawing operation.
The study of deformation and failure of stretched sheets is of considerable practical interest in the sheet metal forming operations. In fact, the occurrence of defects in sheet metal forming is an important problem for mass production, i.e. automotive industry. This necessitates the improvement of microstructure in order to increase strain hardening and formability capacity. The modification of the microstructure and/or the composition of the sheet metal effects all of these parameters and then give a complex boundary condition for defect prediction in sheet forming operations.
The most common sheet metal forming processes are used for deep drawing and stretch forming. In several sheet metal forming processes, both forming types are used together. Deep drawing might be defined as the metal shaping process used for shaping flat sheets into cup-shaped articles. The wall thickness of the produced cup is nearly the same as the thickness of the blank sheet. However, when the thickness of the metal sheet is compared with the thickness of the product, the thickness decreases in stretch forming, markedly. A sheet which has a good drawability characteristic should have high resistance to thickness thinning in the desired cup-shape without a change in sheet thickness when it is formed. The r-value is a measure of resistance to thinning, it may be determined by tensile test and is the plastic strain ratio of width to a thickness in a sheet.
Sheet material which is used to stretch forming should be ductile and uniformly deformed without necking. Strain hardening exponents (n) are a measure of good stretch forming characteristics. Having greater value for n means the desired higher ductile and uniform plastic deformation characteristic. Erichsen test is also a measure of good stretchable. The greater height of the cup shows higher stretchable characteristics. Another important technique for controlling failure is sheet-metal forming limit diagram (FLD) Deformation and strain rates (n) are the effective parameters for formability of sheets.
The aspired good deep-drawability can be realized by a favorable anisotropic material flow during the deep-drawing process. For this, the distribution of the orientations of individual grains plays a decisive role and is determining for above mentioned the r-values. Outgoing from a statistic disorderly distributed grain orientations, r-value increases with increasing fraction of {111}-oriented grains and decreasing the amount of those with {100} orientation parallel to sheet plane, Figure 1.
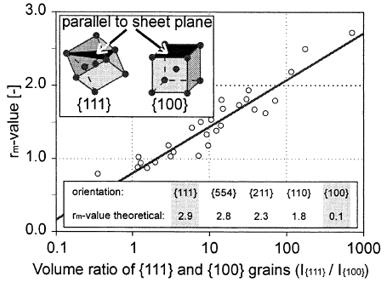
Figure 1: Effect of texture on the mean r-value rm. I{111} and I{100} are the texture intensities of the corresponding orientations.
As above mentioned, the indicative information of deep drawing properties of steels can be obtained from their behaviour during the tensile test. For the pressability criterion of steel, the properties of the yield point, the tensile strength, the strain uniform deformation, and the work hardening exponent are used. Also by ensuring the low scatter in the mechanical properties in the deep drawing steels, the optimum productivity in the drawing press operation is achieved.
The pressability of steel is evaluated using technological test such as Erichsen cupping test. The deep drawing steels should have extremely low carbon content. These steels can be either alloyed with special alloying elements or can be unalloyed steels with special rolling strategies in order to meet demands for lowest possible yield strength levels, good cold formability properties, and good ageing resistance. Deep drawing steels are usually specified by yield strength and tensile strength and by minimum elongation values. For forming properties, minimum values for vertical anisotropy (r-value) and work hardening exponent (n value) are normally specified.