Abstract
Press Hardening Steels (PHS) are a unique group of materials which are mostly comprised of different kinds of boron-alloyed manganese steels and gain wide application to produce high strength structural body elements.
As part of the AHSS group of steels, PHS play an important part in the ever increasing challenges of light weighting vehicles whilst maintaining durability and passive safety.
Environmental aspects have become extremely important when engineering new passenger cars. In order to reduce fuel consumption and toxic emissions, one step is to decrease the weight of the vehicle. Regarding the car body structure this means down-gauging of the sheet components and the introduction of more advanced high strength steels (AHSS) in order to maintain a high performance in terms of crashworthiness, durability etc.
The advanced high-strength steels (AHSS) help engineers meet requirements for safety, efficiency, emissions, manufacturability, durability, and quality at a low cost. AHSS are a newer generation of steel grades that provide extremely high-strength and other advantageous properties, while maintaining the high formability required for manufacturing. It was well known that AHSS have been on the road for many years, but with additional research and development, automakers are using these newer grades in more applications.
The AHSS family includes Dual Phase (DP), ComplexPhase (CP), Ferritic-Bainitic (FB), Martensitic (MS or MART), Transformation-Induced Plasticity (TRIP), Hot-Formed (HF), and Twinning-Induced Plasticity (TWIP).
Among the Advanced High Strength Steels, Press Hardening steels (PHS) form a unique group: these are mostly different kinds of boron-alloyed manganese steels and gain wide application to produce high strength structural body elements (e.g. A-and B-pillars, etc). Press Hardening Steels are widely used in car body manufacturing in hot forming processes.
To illustrate typical applications of AHSS, and press-hardened components in particular, are shown in Figure 1. Press-hardened components are in red color, otherwise indicated with arrows.
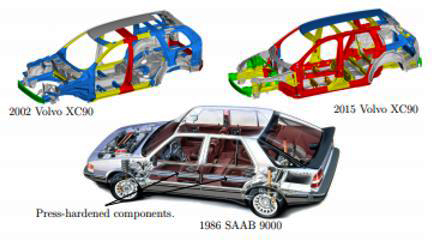
Figure 1: Automotive body structures. Press-hardened components are shown in red, otherwise indicated with arrows.
What are Press-Hardened Steels (PHS)?
Press-Hardened Steels are Boron added (.001%-.005%) Carbon /Manganese steels that have been in use since the mid 1980’s for automotive body in white construction. These steels are also known as HF or Hot Formed Steel.
The hot forming process of PHS steels
Hot forming of steels is a complex forming and tempering operation: it is often termed as hot press forming or press hardening of steels, too. The full austenitization of the material is regarded as the first step in hot press forming. Forming is performed is cooled down rapidly in the tool applying the critical cooling rate, hence resulting in martensitic microstructure.
To enable the Boron-alloyed steel material to be formed and further on cooled down to a fully martensitic structure, the material first has to be heated up to its austenitization temperature at around 880-950°C. To achieve a fully martensitic structure, the cooling rate must exceed 25-30°C/s. The small amount of Boron (~ 0.002 weight-%) is used to facilitate the quenching process, wherefore the material often is referred to as Boron steel in colloquial terms. (Figure 2).
The hot-forming process is mainly divided into two different approaches, the indirect and the direct one, where the direct process is the most commonly used among the automotive OEMs. These two processes offer different advantages for the final application in terms of design versus cost and available choices for surface protection.
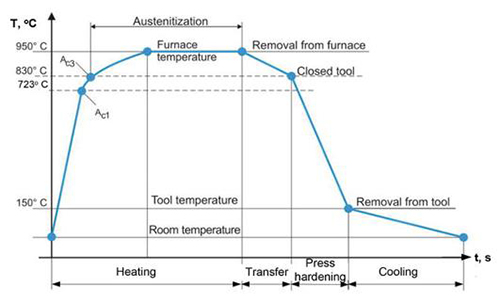
Figure 2: Temperature vs. process time for hot press forming of PHS Making the first forming step(s) by conventional cold forming, the indirect process offers the possibility for more complex geometries and undercut designs before the shaped components are heated, transferred to the oven and finally tempered (Figure 3). This means that two sets of tools are necessary, one for pressing and one for cooling. One advantage however, with this process, is that it offers the possibility to use a conventional zinc-based coating for cathodic corrosion protection.
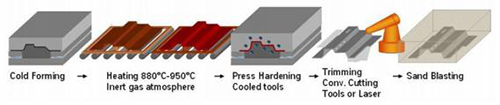
Figure 3: Schematic description of the indirect hot-forming process. cold-forming of the blank in one or several steps, heating of the pressed part to roughly 900°C, rapid cooling of the part to achieve a martensitic structure, post processing like laser or tool cutting etc.