Abstract
Electro-slag welding is a primary method for cast weld assemblies of heavy sections since one of the key characteristics is its suitably high deposition rate.
As with all welding techniques the success relates to the control of the numerous variables of the process and with ESW it is no different in that controlling the mass-transfer coefficient can drive a successful operation.
The quality of welded joint depends greatly on the structure and properties of a weld metal and heat affected zone (HAZ), which are determined by thermal cycle. As well as the melting and crystallization of weld metal, the change of temperature results in structural transformations, volumetric changes, elastic-plastic deformations of product material, which at unfavorable thermal cycle in the HAZ causes arising of brittle hardened structures for carbon and alloyed steels which predetermined the increased tendency of metal of this zone to cracks and brittle fracture of welded joint as a whole.
Therefore, in welding of carbon structural steels the task is put to produce welded joint of a full strength. For the thermal cycle of the HAZ in electroslag welding (ESW) the delayed heating of this zone, its long exposure at the temperatures of overheating and next delayed cooling in the region of temperatures of pearlite, intermediate and martensite transformations are characteristic.
The aim of the work S.M. Kozulin, I.I. Lychko, G.S. Podyma is the study of effect of thermal cycle on the structure and mechanical properties of welded joint in multilayer electroslag welding using consumable nozzle. The measurements of thermal cycles of the metal of heat affected zone were carried out. To study the effect of self-heat treatment on the structure and properties of welded joints the investigations were carried out including macro- and microanalysis of weld layers and their heat affected zones as well as mechanical tests of the characteristic areas of welded joints. It was found that in the overheating zone of base metal, not exposed to the reheating, the growth of grains reaches N2 and N1 according to the GOST 5639—82 and in the zones of reheating (self-heat treatment) – N7 and N8. (Figure 1 a and b).
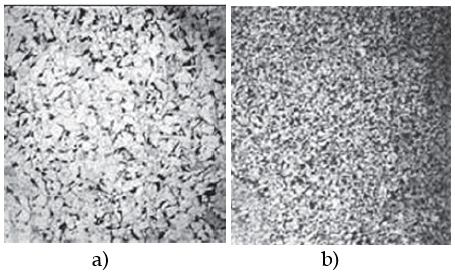
Figure 1: a) metal of 2nd layer exposed to reheating higher than the temperatures of Ac3 point in making the 3rd layer b) Deposited layer of metal exposed to reheating higher than the temperature of point Ac3
The hardness of metal of layers and areas of heat affected zone exposed to reheating is on average by 20 % lower than that of the areas of heat affected zone with base metal not exposed to reheating. It was shown that in multilayer electroslag welding alternatively from one edge of a butt to another one the volume of self-heat treatment of the layers of multilayer electroslag weld reaches 38.4 %. In multilayer electroslag welding with deposition of layers from the middle of a butt to its edges, the volume of self-heat treatment of the first (central) layer reaches 87 % and the rest (except of the external layers) is 30—43 %. It was established that the width of heat affected zone scarcely depends on specific energy input in the investigated range of its values.
On the other hand in the work of S.Scnchurov is presented mathematical models of metallurgical processes of electroslag welding (ESW), electroslag remelting (ESR), electroslag hardfacing (ESH) and centrifugal electroslag casting (CESC). The models allow to predict chemical composition of metal along and in transversal sections of an ingot, a weld and a surfacing layer, and in thickness of a casting. Using of the models reduces expenses during selection of optimum process conditions and materials which providing weld metal or ingot metal with required composition.
One of the most important parameters of the mathematical models is a mass-transfer coefficient. A physical modelling method of study of mass-transfer between molten metal and slag in electroslag technologies (EST) was developed. Influence of electrode melting rate and casting velocity on mass-transfer coefficients was studied.
The model is based on the analysis of the kinetics of interaction between the metal, slag and gas. This approach was used for the processes of ESR (1), ESW (2), ESH (3) and CESC (4). The model makes it possible to forecast the chemical composition of the electroslag metal, including the composition in longitudinal and transversal sections of a weld or ingot, and takes into account the following factors:
- the simultaneity of all the reactions taking place at the metal-slag boundary, and their effects on one another;
- the effects of diffusion of all the reagents in the metal and slag on the rate of each reaction;
- the interaction between the molten metal and slag at the tips of electrodes, during melting of the parent metal, and at the surface between the metal pool and slag;
- the electrochemical effects;
- the effects on the reaction rates of the chemical composition and the amount of slag taking place over a period of time and caused by the interaction between the slag, metal and gas, the deoxidizing of the slag pool, the pouring of flux, the solution in the slag of the oxide films at the surfaces of the electrode and edges of the parent metal;
- the introduction of metallic additives into the metal pool;
- the segregation during the metal and slag skin crystallization.
Generally, the result of this model indicate that the possibility of prediction of the chemical composition of the electroslag metal enables optimization of electroslag technologies as early as in the design stage, by selecting the composition of the initial materials and the process conditions providing electroslag metal with the required composition.