Abstract
The Romelt process is born and driven by the ever present need to design effective steel and iron making processes which are much cleaner in respect to their environmental impact.
First industrial Romelt plant is currently being constructed in Burma and is expected to have a design annual capacity of 200,000 tpy.
In the changing global market scenario for raw materials for the steel industry, a number of novel iron– and steelmaking process technologies are being developed to provide the steel companies with economically-sustainable alternatives for iron– and steel-making. In addition, the steel industry is also focusing on reduction of energy consumption as well as green-house gas (GHG) emissions to address the crucial subject of climate change. Climate change is presenting new risks to the highly energy– and carbon-intensive, iron and steel industry. The industry needs to focus on reduction of energy consumption as GHG emissions to address climate change. Development of alternate iron– and steelmaking process technologies can provide steel companies with economically-sustainable alternatives for steel production. In addition to CO2 abatement (energy efficiency technologies) initiatives that are being implemented by steel companies, there are a number of alternate ironmaking process technologies that are provide valuable options to steel companies in dealing with the current issues. While the conventional blast furnace ironmaking process is still widely implemented, a number of these alternate ironmaking processes are being considered for implementation.
Current status of some selected ironmaking processes technologies are summarized in Table 1.
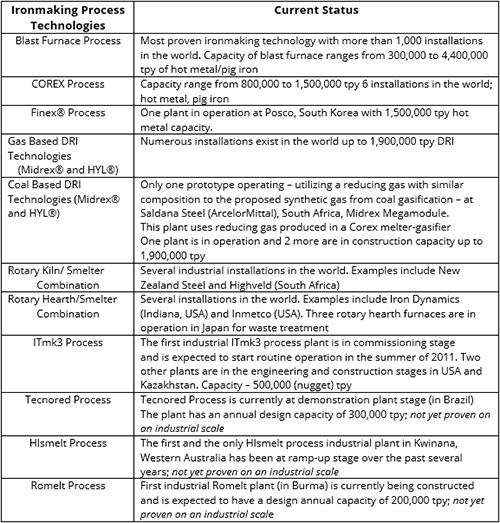
Table 1:Current Status of selected Ironmaking Technologies Romelt process is technique of continuous ironmaking from various iron-bearing materials using inexpensive noncoking coal. The general diagram of the Romelt furnace is shown in Figure 1. Iron containing materials, coal and flux, are fed, using weigh-hoppers, from relevant bins to the common conveyer. The charging into the furnace is performed through the aperture in the furnace roof. No preliminary mixing of charge materials is needed: it takes place directly in the slag bath due to its intensive agitating. The working space of the Romelt furnace is under negative pressure of 1 to 5 mm w.c. which is ensured by induced draft fan.
The bath of melting slag is blown with an oxygen-air (100–40%) mixture through the lower tuyeres positioned below the slag layer. The tuyeres have simple design and proved to be reliable in operation. They ensure the required agitating power of the slag bath.
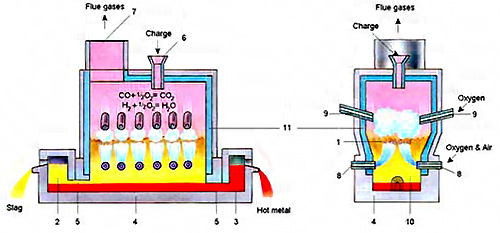
Figure 1:The Romelt furnace scheme: 1 - agitated slag, 2 - sump for slag, 3 - sump for hot metal, 4 - hearth with refractory lining, 5 - channels for slag and hot metal, 6 - feed tunnel, 7 - gas-escape branch pipe, 8 - lower tuyeres, 9 - upper tuyeres, 10 - calm slag, 11 - water-cooled panels The reduction of iron from its oxides in slag can be done by coal particles and by carbon dissolved in metal inclusions in the slag. There are two ways that coal is involved in the reduction of iron in a Romelt furnace:
- reduction occurring on the surface of gas bubbles that contain coal particles; the role of these particles is to regenerate the reducing atmosphere in the bubbles (the thermodynamic conditions which exist in the Romelt process make it difficult for gas bubbles that do not contain coal particles to reduce the iron oxides);
- reduction occurring with the coal particles in direct random contact with the slag; here, reduction takes place under conditions similar to those which exist when iron is reduced by a rotating carbon-bearing sample and gas bubbles are forcibly removed from the sample’s surface.
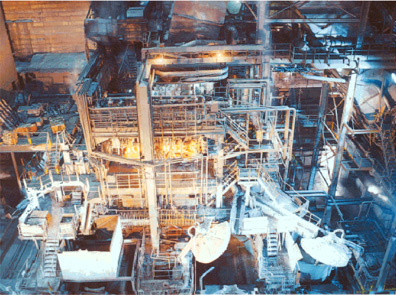
Table 2:The Romelt furnace under operation