Abstract
Explosive welding has a firm reputation for being an effective technique to join metals plates, often of dissimilar materials with a resulting high bond strength.
Some of the key applications of explosive welding include marine, heat exchangers and light weight metals sheets.
It is widely known that the explosive welding technique has established a reputation with respect to the joining of metal plates due to the high reliability of the obtained bond strength. Generally, explosive welding is performed to set plates with a fixed stand-off distance, and the welding is achieved by a high-velocity collision. The metal jet, formed ahead of the collision point, is vital for obtaining a sound bonding because the jet cleans and activates the metal surfaces ahead of the welding. Further, the hydrodynamic behavior of metals under extremely high-strain-rate and high pressure results in a wavy structure at the welded interface.
The application of explosive welding has unique advantages in joining metals that would frequently be incompatible, such as titanium or zirconium and steel. These clad materials are commonly used today in chemical process vessel construction. Intuitively, it may be assumed that the great pressures produced by various types of explosives used in bonding and forming processes could bring the metal plates together so forcefully that welding would naturally occur.
However, it has been shown that high pressure alone is not sufficient to form a satisfactory metallic bond. To achieve a metallic bond, atoms of one metal must come into intimate contact with atoms of the other metal. However, metals are generally coated with surface films including oxides (e.g., Al2O3), nitrides (e.g., AlN), and adsorbed gases (such as H2), which prevent sufficiently close contact. These surface films must be removed by effacement or dispersion before welding can be achieved. Once the films have been removed, the underlying metal can be brought together by high pressure to form the metallic weld. The surface film may also be dissipated in a melted region so that the weld is formed via a solidified zone.
Explosive welding is of two types. The oblique and parallel configuration, the oblique configuration is shown in Figure 1, this method come into play when the size of plate is thin and small, but when the plate is large then parallel method is taken as shown in Figure 2.
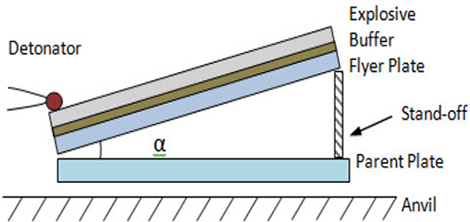
Figure 1:The oblique configuration
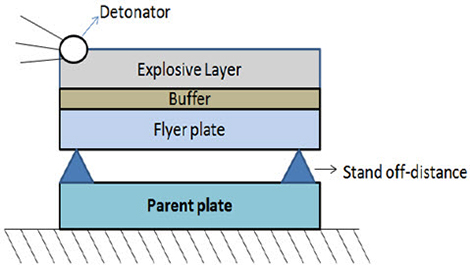
Figure 2:The parallel configuration
In parallel method the plates to be welded are clean and polish very gently so as to form the good welding, in this process the base plate are keep at the ground in which the flyer plate is placed at top of it by the predefine distance called stand-off distance, the design of the stand-off should be able to bear and handle the load of flyer plate and explosive, above this buffer sheet is kept at the surface of flyer plate, so as to protect the top surface from damage due to the shock impact of the explosive. Now the prepared explosive placed in a box structure design at the perimeter of the flyer plate is placed at the top of the flyer plate.
Applications
Explosive welding is used in many different organization and industries, some of the important applications of explosive welding process include:
- Used by the marine for the various applications for the structurally sound corrosion resistant of aluminum and steel.
- Cylindrical components such as tubular transition joints, tube to tube plate and concentric cylinders.
- Heat exchanger with a clad tube sheet and sheel.
- To produce high strength weld between niobium and 6061- T651 Aluminum.
- Feed water heater tubes.
- Joining of dissimilar metals, e.g. steel to aluminum.
- Joining of similar metals, e.g. Aluminum to aluminum [6].
- Light weight metal sheets.