Abstract
Processes connected to handling liquid metals are extremely important in managing operational costs and productivity but provide most gain in the opportunities available to impact overall quality of the cast component and the related refining activities.
Vacuum degassing is most commonly used to remove hydrogen and nitrogen, which in the finished product can lead to cracking defects in the cast.
Melting and handling liquid metals are two of the most critical components in the overall metal casting operation. The manner in which the metal is melted, the way the metal is transferred into the castings, and the whole liquid metal handling process have a significant impact on productivity, on the cost of operations, and certainly on the quality of the resultant cast component.
Processing the metal in its molten state is the activity wherein the most gains can be achieved. Molten metal processing is an opportunity for refining and quality enhancement. For example, processes such as alloying, degassing, filtration, fluxing, and grain refinement and modification in aluminum are usually carried out in the liquid metal prior to casting. The mass transfer rates and the kinetics are such that these reactions are carried out much more effectively in the melt.
In the continuous casting of steel, vacuum degassing of the liquid steel is often performed to remove hydrogen and nitrogen which can lead to cracking defects in the cast. Degassing effectively prevents this low ductility from occurring and provides steel producers a wider “margin for error” in their caster operation. However, there are significant energy costs associated with degassing that prohibit steel producers from using it for all types of production. Degassing must be used intelligently to achieve a combination of acceptable product quality and energy costs.
The Vacuum Induction Degassing (VID) furnace concept has been developed for special applications in the ferrous and non-ferrous metals industry for charge weights up to 30 tons. Whenever pouring under vacuum is not specified or not required for metallurgical reasons, the bell type furnace with open air teeming is recommended for its favourable economics. Smaller steel shops and foundries will be able to produce with the VID furnace, within one step, high quality vacuum treated steels, whereas larger shops have to realize these qualities employing a conventional LF/VD/VOD production line. The temperature losses during degassing treatment are compensated by induction heating.
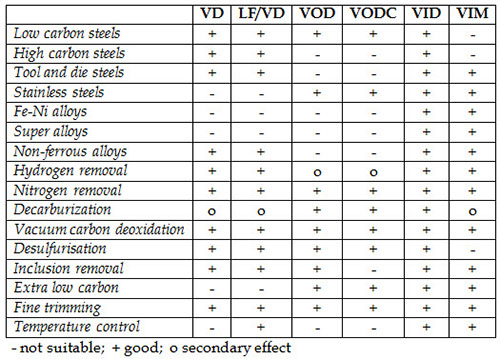
Table 1: Product application and quality improvement in different processes Vacuum Induction Melting (VIM) is one of the most commonly used processes in secondary metallurgy applied for refining treatment in the liquid state and the adjustment of chemical composition and temperature. To achieve the increasing quality demands on the resulting material and at the same time to:
• saving of raw materials such as alloying elements due to higher yield
• saving energy
The application of vacuum in the induction melting process is a must for many specialized materials. For example, vacuum induction melting is indispensable in the manufacture of special alloys, which must be melted under vacuum or in an inert gas atmosphere because of their reactivity with atmospheric oxygen. The process is suitable for the production of high-purity metals within an oxygen-free atmosphere. This limits the formation of non-metallic oxide inclusions.
Vacuum induction melting makes effective degassing of the melt possible and extraordinarily precise adjustment of alloy composition, since the temperature, vacuum, gas atmosphere, pressure and material transport (e.g., through stirring of the bath) can be adjusted independently of one another. Besides the exact concentration of alloying elements, the content of trace elements is also important for many alloys.
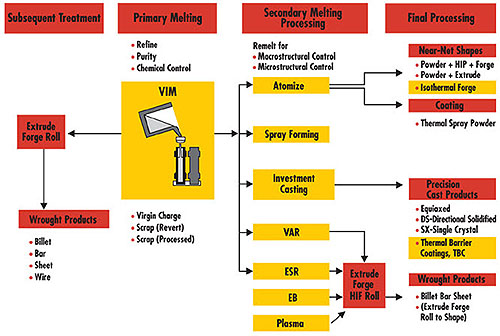
Figure 1: Current processing route for products cast from VIM/VIDP furnaces Metallurgical Advantages of Vacuum Degassing:
- Melting in an oxygen-free atmosphere, this limits formation of non-metallic oxide inclusions and prevents oxidation of reactive elements;
- Achievement of very close compositional tolerances and gas contents;
- Removal of undesired trace elements with high vapor pressures;
- Removal of dissolved gases e.g. oxygen, hydrogen, nitrogen;
- Adjustment of precise and homogeneous alloy-composition and melt temperature.