Abstract
MIM is a relatively new injection molding method by which metal powders are combined with thermoplastic binder to generate complex molded shapes.
The technique generally has common application in a number of industry sectors such as aerospace, automotive, and medical devices.
Metal Injection Molding (MIM) is a relatively new production method that was developed in the 1970s. In the MIM process, fine metal powder is mixed with a thermoplastic resin called the binder, and the mixture is then processed into a molded body with a complex shape by the same injection molding method as that for general plastic. After that, the binder is removed from the molded body by heating or using a solvent, and the resulting molded body is sintered at high temperature to obtain the final product. Compared to conventional powder metallurgy, MIM can make a product with higher density, which is to say increased strength.
This manufacturing method allows to produce metal parts with complicated shapes and small tolerances, with the ease and automation of the injection molding machine. The process however requires some extra steps to accomplish this.
The metal injection molding process consists of the following steps:
- MIXING: At the mixing stage, both metal powder and the polymeric binder (thermoplastic types) are combined into a homogeneous mixture;
- INJECTION MOLDING: Injection molding machines are used to inject the green part. The mould dimensions are calculated by applying a "shrinkage factor" which is around 15-20% for most material to the part drawing;
- DEBINDING: Debinding is a process whereby the binder is removed from the molded part, leaving behind the metal 'skeleton' that retains the molded shape. This remaining element is known as the 'brown' part;
- SINTERING: Finally, the brown parts are sintered The metal powder particles will be bonded together and consequently this step provides the strength in the finished product.
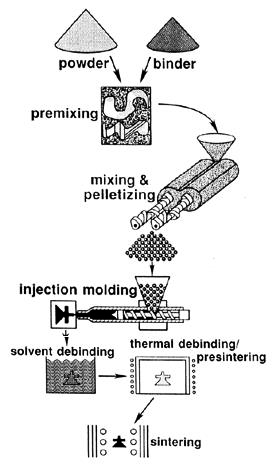
Figure 1: The MIM Process
Metal injection molding is best suited for the high-volume production of small metal parts. As with injection molding, these parts may be geometrically complex and have thin walls and fine details. The use of metal powders enables a wide variety of ferrous and non-ferrous alloys to be used and for the material properties (strength, hardness, wear resistance, corrosion resistance, etc.) to be close to those of wrought metals. Also, because the metal is not melted in the MIM process (unlike metal casting processes), high temperature alloys can be used without any negative affect on tool life. Metals commonly used for MIM parts include the following:
- Low alloy steels
- Stainless steels
- High-speed steels
- Irons
- Cobalt alloys
- Copper alloys
- Nickel alloys
- Tungsten alloys
- Titanium alloys
Metal parts manufactured from the MIM process are found in numerous industries, including aerospace, automotive, consumer products, medical/dental, and telecommunications. MIM components can be found in cell phones, sporting goods, power tools, surgical instruments, and various electronic and optical devices.