Abstract
Ion Plasma Nitriding is considered one of the most superior surface treatment techniques which drives improvements in the hardness, wear resistance and corrosion resistance of the surfaces of steels.
Due to the general material performance improvements, IPN has application in a number of areas including in the production of dies and punches, gears, crankshafts and many more areas where robust, quality components are required.
Ion-plasma nitriding (IPN) is a surface hardening treatment process that allows to increase the hardness, wear resistance and corrosion resistance of the surfaces of steels. It is the most technically superior of all nitriding processes and has many advantages compared to traditional salt bath and gas nitriding.
Steels are the most common materials treated with plasma nitriding. This process permits the close control of the nitrided microstructure, allowing nitriding with or without compound layer (white layer) formation. In addition to enhanced material performance, the lifespan of your parts will increase with much improved strain limits, fatigue strength, wear resistance and corrosion protection.
With a wide range of process control and optimization possibilities, plasma nitriding makes it possible to achieve stringent requirements not capable by gas or salt bath nitriding. Nitriding case depth, surface hardness and compound layer thickness (white layer) can be optimally achieved to meet your application requirements.
How It Works?
The parts are placed in a vacuum vessel, convectively heated to the required process temperature in an atmosphere of specialty gases. High voltage is then applied between the work pieces and the furnace wall. As the process gases begin to activate (ionize), a corona discharge (violet glow) takes place in the treatment chamber. The high voltage reacts with the positive gas ions, which are energized and accelerate in a direction toward the work piece with much energy creating an “ion bombardment” to the surface.
This ion bombardment can create intense heat in the work piece and must be controlled. The heat is precisely controlled via very fast on-off voltage transition times or “pulse ionization”. The controlled ion bombardment reacts with carbon atoms in the work piece forming nitrides. These nitrides eventually channel their way through the material’s grain boundaries, diffusing into the part leaving behind a hard, non-distorted, smooth surface.
Within an individual process, several parameters such as voltage, gas mixture, pulse frequency, temperature, time, etc. are controlled. Unique combinations of these variables can be developed for exotic applications and saved as a custom “recipe”, which can be run again and again with absolute repeatability.
The Plasma Ion process is done in a vacuum vessel at low temperatures (750°-1040°F or 400°-560°C) where high-voltage electrical charge forms plasma, causing nitrogen ions to accelerate and impinge on the metal. When the nitrogen ions bombard the part they heat up metal, clean the surface, and absorb nitrogen into the surface, and can be applied to any ferrous metal.
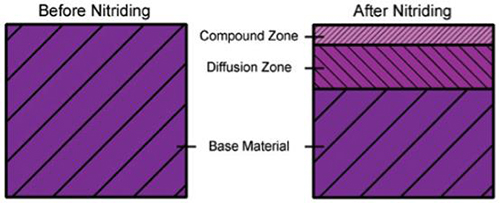
Figure 1: The schematic view of Plasma Ion Nitriding Ion (Plasma) Nitriding Pros
- Mechanical masking (sometimes reusable) can be used to prevent nitriding of specific areas of the product
- Great process for alloy steels and stainless steels that require surface activation to allow for nitriding
- Ion bombardment helps “sputter” clean the surface
- Gases used for processing are safe and environmentally friendly
Ion (Plasma) Nitriding Cons
- Limited on compound zone thickness (maximum) due to the nature of the process
- Relatively less superior temperature control (as compared to gas) – this can lead to variance in case depth / hardness / dimensional stability
- Increases surface roughness
Typical Applications for Plasma Ion Nitriding
- Dies and punches for metal forming
- Gears
- Crank shafts
- Feed screws
- Camshafts
- Guides
- Cylinders
- Mandrels
- Molds for plastics
- Molds for casting of nonferrous metals and alloys
- Milling tools
- Drilling tools