Abstract
Steels commonly used in the power generation industry have a finite life and are subject to the phenomena known as creep.
Chromium and tungsten have been studied to assess their potential to improve creep life and overall results were positive where optimum inclusion of Cr and W results in much improved creep rupture strength.
The Cr and W effect on the creep strength of ferritic steels were studied in the paper of Y. Hasegawa, T. Nishiura, T. Sato using the new strengthening hypothesis, precipitation strengthening mechanism, by examining the residual aligned precipitates consisting of W and Cr. In 2 mass% W-containing steel, the increase in Cr content up to 10 mass% resulted in the creep life extension. However, the Cr content higher than 11 mass% decreased the creep life. In 9 mass% Cr containing steel, the increase in W content decreased the creep deformation rate with creep time. However, it also shortened, the time to reach the minimum creep rate. Therefore, Optimum Cr and W contents possibly resulted in the optimum alloy design.
To understand the effect of W and Cr contents on creep strength, the precipitation strengthening hypothesis by the precipitates at the block boundary must be introduced. The residual aligned precipitation line is supposedly an effective obstacle for the dislocation motion at the interparticle space of aligned precipitates. The new hypothesis will be activated after block boundary migration. It occurs during the acceleration creep period. On the basis of the hypothesis, creep strength was expressed as he summation of threshold creep stress and effective internal creep stress. According to the experimental data of microstructure recovery, the effective internal stress decreased with creep deformation and consequently vanished. In such cases, creep strength is decided only by threshold stress of creep. Integrating all, we concluded that the creep deformation mechanism of ferritic creep-resistant steel possibly transits from the viscous dislocation gliding mode to the microstructure recovery driven type mode during the acceleration creep.
Cr and W effect on the creep strength of W-containing ferritic steels are studied using the new strengthening hypothesis by the examining the residual aligned precipitates consisting of W and Cr. From the obtained results the authors have been concluded that:
- Cr-content increase resulted in the creep-life extension up to 10 mass %. Cr content more than 11% decreased the creep life for 2 mass% W containing steel;
- W-content increase decreased the creep deformation rate with creep time. However, it shortened the time to reach the minimum creep rate;
- Therefore, optimum Cr and W contents may result in the highest creep rupture strength;
- To understand the effect of W and Cr contents on creep strength, the precipitation strengthening hypothesis by the precipitates at the block boundary must be introduced;
- The residual aligned precipitation line is supposedly the obstacle for the dislocation motion at the interparticle space of the aligned precipitates;
- The new hypothesis occurs after block boundary migration, long-term creep;
- On the basis of the hypothesis, the creep strength was expressed as the summation of threshold creep stress and effective internal creep stress;
- According to the experimental data of microstructure recovery, the effective internal stress decreases with creep deformation and vanishes. Finally, the creep deformation mechanism of ferritic creep-resistant steel may transit from the viscous dislocation gliding mode to the microstructure recovery driven type mode.
Creep resistant steels must be reliable over very long periods of time in severe environments. Their microstructures have to be very stable, both in the wrought and in the welded states. The paper of H. K. D. H. Bhadeshia reviews the quantitative methods for the design of steels for elevated temperature applications. A methodology is described for the calculation of complex precipitation reactions over periods extending many tens of years. However, microstructure alone is not enough in the design of alloys. The estimation of the creep rupture stress using a neural network technique is described in the second part of this review. The calculation of the influence of solute-elements on the self-diffusivity of iron, which features in many creep equations, is an emerging area in alloy design. The methodology for such calculations is reviewed in the final section of the paper.
The Matrix Microstructure
The most exciting ferritic creep-resistant steels start with a microstructure which is martensitic. On the other hand, the best established steels of this kind rely on allotriomorphic ferrite or bainite as the starting microstructure. Why are modern heat-resistant steels based on martensite? Is the martensite desirable and can it be altered to better fit the purpose? And how do calculations contribute to this exercise? Low-chromium steels, such as the classical 21⁄4Cr1Mo or 1CrMoV alloys have formed the backbone of the power generation and petrochemical industries for at least five decades, for operating temperatures of 565°C or less. The 21⁄4Cr1Mo is essentially bainitic, whereas the 9Cr1Mo type alloys developed much later, for higher temperatures and greater corrosion/oxidation resistance, are martensitic. Figure 1(a) shows that in the unmodified form the 9Cr1Mo does not have a superior creep rupture performance.
The answer must be that the martensitic matrix arises by chance. The chromium concentration was increased for oxidation and corrosion resistance with balancing additions of other solutes to avoid d -ferrite. The hardenability then becomes sufficiently large to induce martensite instead of bainite for identical cooling conditions. This is illustrated by the calculated time–temperature transformation diagrams for 2.3, 4.3, and 9.3 wt% chromium steels in Figure 1(b). Martensite, Bainite and Precipitation Could it be that the martensitic microstructure, which has a very high number density of defects, encourages the precipitation of more numerous and finer carbide particles which resist creep deformation? Baker and Nutting conducted a transmission electron microscope study of carbide precipitation reactions during the isothermal tempering of a 21⁄4Cr1Mo steel in two starting microstructural conditions, bainite and martensite. Whereas the kinetics of precipitation were not found to be exactly identical in the two cases, the differences were small over the temperature range of interest (500–650°C). In hindsight this might be expected since both microstructures contain similar defect densities (dislocations, plate boundaries, austenite grain boundaries); the slightly smaller defect density expected in bainite does not seem to have any significant effect on the precipitation kinetics. A bainitic microstructure should therefore be adequate and martensitic steels have the additional burden that they are difficult to weld.
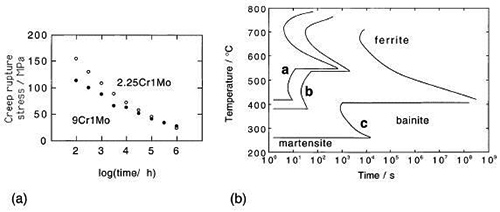
Figure 1: (a, b): Calculated rupture strength as a function of time for a bainitic (low Cr) and martensitic (high Cr) steel. The exact compositions are 0.15C–0.25Si–0.50Mn–2.3Cr–1Mo–0.10Niwt% and 0.10C–0.60Si–0.40Mn–9.0Cr–1Mo–0.00Ni wt% following an identical heat treatment consisting of 1 056°C for 12 h, 740°C for 13 h. (c) Calculated time–temperature transformation diagrams for steels x (0.15C–0.25Si–0.5Mn–1Mo–2.3Cr wt%), y (4.3Cr) and z (9.3Cr). The transformation curves refer to zero percent reaction. In each case the upper curve represents diffusional transformation whereas the lower curve represents bainite.