Abstract
‘Intelligent’ BOF represents the next generation of what is an established process but at the moment more traditional methods have restrictions relating to the precision of the product end point.
The main objective of using an intelligent BOF system is to improve end-point prediction ultimately to allow the plant to eliminate the second sublance reading, thereby reducing operating cost and the associated production delays.
The basic oxygen furnace (BOF) is one of the key processes in iron and steel production. It is a typical complex batch chemical reactor with sophisticated thermal and chemical reaction processes, which converts liquid pig iron into steel with desired grade (temperature and chemical compositions, such as carbon, etc.) under oxidation conditions. The BOF steelmaking end point quality control is always managed with the aid of either operator experience or a first principle charge model; therefore, often resulting in a relatively poor hit ratio of the bath endpoint. The accurate prediction of the endpoint quality is vital not only for BOF operation, but also for “steelmaking caster-hot rolling” production balance.
However, due to the imprecision of the BOF charge model, a lack of real-time measurements and process uncertainties, it is difficult to predict the BOF endpoint product precisely. Due to the facts mentioned above, the good news is that modern intelligent control technology is developing rapidly as a BOF endpoint control model provides a new way.
Tenova Goodfellow is currently commercializing the next generation of ‘intelligent’ BOF (i BOF technology (see Figure 1); designed to reduce GHG emissions while improving yield, productivity, scrap melting capability and operating costs.
It is modular and can be configured in a number of ways to meet the specific requirements of each BOF shop. For example:
- Enhanced end-point detection
- Early warning slop detection
- Enhanced post-combustion
- Automated tapping control
The first installation was the end-point detection module on a 165 short ton top-blown converter at US Steel Hamilton Works. US Steel was able to predict end-point carbon to within ± 0.0115% carbon for 90% of heats and within ± 0.0150% carbon for 97% of heats. Table 1 summarizes consumable cost benefits associated with improved endpoint detection as confirmed by US Steel.
i BOF end-point prediction also reduced the standard deviation for end-point carbon on 0.1% carbon heats by almost 60% which has enabled US Steel to successfully implement a ‘catch carbon’ practice when producing high carbon heats. Ultimately, the objective is to completely eliminate the need for Celox bombs to further reduce consumable costs.
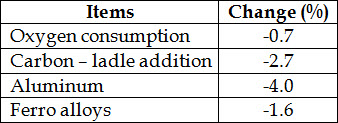
Table 1: Cost benefits using i BOF endpoint detection at US Steel Hamilton Works A second installation on a 360t BOF converter with top blowing and Ar/N2 bottom injection included the improved end-point prediction and the slop detection modules. This BOF was equipped with a sublance system with the normal practice being two sublance readings per heat, the first in-blow and the second confirmatory before tapping. The objective was to improve end-point prediction ultimately to allow the plant to eliminate the second sublance reading, thereby reducing operating cost and the associated production delays.
Table 2 confirms that the predicted end-point C and temperature are in excellent agreement with the final in-melt sublance reading, thereby providing confidence for the plant to eliminate this second sublance reading and to proceed with a ‘blow and tap practice’. A second objective for this installation was to provide advanced warning of the onset of a slop event to avoid yield and productivity losses associated with metal ejection from the converter. Extensive trials demonstrated an 87% slop detection rate with about 20–40secs of advance warning before the visual onset of metal ejection. This warning provides sufficient time for the plant operators to take preventative action to mitigate the effects of the slop event.

Table 2: i BOF endpoint detection compared to end-of-blow sublance readings in a 360t BOF

Figure 1: i BOF technology features