Abstract
Boriding is an established surface treatment process which helps tackle the common issue of extending the general life of moving bearing applications and especially in dusty, corrosive environments.
There are several advantages of the boriding surface treatment process including a prolonged hardness at high temperatures, flexibility in its applications with different material types and more.
Most mechanical components used in a variety of rolling, rotating, or sliding bearing applications, as well as those that are used in metal-cutting and forming operations, rely strongly on high hardness and low friction surface properties of base metals for high performance and durability during use. In a dusty, sandy and corrosive environment, high resistance to erosion and corrosion becomes very important.
There are numerous surface treatment methods that are currently used to enhance the near-surface properties of engineering components. Some of these methods (such as nitriding, carburizing, carbonitriding, and boriding) are theremo-chemical in nature and based on thermal diffusion of carbon, nitrogen, and boron atoms into the near surface regions of these components at high temperatures.
Boriding is a surface treatment process of diffusion and chemical reaction of the elemental boron into a substrate at elevated temperatures which results in a refractory coverage with superior mechanical properties and corrosion resistance. The boriding process can be carried out by both chemical and electrochemical means. One needs an activator (which is a reducing agent such as hydrogen) in a chemical process as well as a boriding agent. Activators and the boriding agent (which is generally a boron halide) react to derive elemental boron which diffuses into the metal surface.
There are various chemical and physical boriding techniques such CVD (chemical vapor deposition), PACVD (plasma-assisted CVD) and PVD (physical vapor deposition). Apart from these, boriding can also be carried out by heating the boron-yielding agents or elementary boron in air-free media at elevated temperatures which results in the diffusion of boron on the surface. In the electrochemical method the metal is immersed into the melts of boron salts and boron is reduced and deposited on the surface using a suitable potential. Elemental boron then diffuses into the metal structure.
On the other hand, Boriding can be achieved with boron in different states such as solid powder, paste, liquid and gas. Different methods of boriding exist such as plasma boriding, paste plasma boriding, electrochemical boriding (called PHEB), boriding in a fluidized bed, gas boriding, solid boriding (powder or paste). Boriding is a well-known thermomechanical surface hardening extensively used for many decades.
The boriding procedure is dependent on the boriding agent, boriding type, temperature and time. Boriding temperature is the biggest factor which affects the cost of the process and choice of the substance to be borided. Elevated temperatures may be detrimental to the mechanical properties of the substrate.
Other advantages of boriding include:
- Hardness of the boride layer can be retained at higher temperatures than, for example, that of nitride treatments.
- Can be applied to a wide variety of ferrous, nonferrous, and cermet materials.
- Borided surfaces have moderate oxidation resistance (up to 850) and are quite resistant to attack by molten metals.
- Borided parts have an increased fatigue life and service performance under oxidizing and corrosive and corrosive environment.
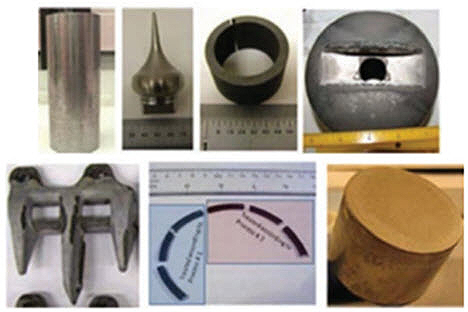
Figure 1: Industrial parts treated using boriding: (a) engine piston pin, (b) titanium textile guide, (c) superalloy bearing part, (d) Inconel 718 ball valve, (e) agricultural knife guard, (f) engine piston ring, and (g) engine tappet.