Abstract
Brazing is becoming an increasingly popular joining method and especially for aluminum and its associated alloys using vacuum brazing techniques.
Some key advantages of vacuum aluminum brazing is its flexibility to join materials of varying shape and form and also its possibilities for joining dissimilar materials.
Along with welding, brazing is becoming an ever more important technique for joining materials. Many products made of aluminum, including aluminum alloys can only be economically manufactured using brazing techniques.
The unique feature of vacuum brazing is that the aluminum oxide cannot be removed by the vacuum. The mechanism of the brazing process is as follows: The coefficient of expansion of aluminum is about three times as great as that of aluminum oxide. That’s why the oxide layers crack up on heating and the liquid brazing alloy can pass through these cracks down to the bare base material.
The aluminum oxide layer becomes mechanically detached. Oxidation of the aluminum in the cracks during the heating phase can only be prevented if the atmosphere is completely devoid of oxygen. As a result, there is not only a minimum requirement put on the level of the vacuum (10-4 mbar or better) but in addition getter materials must be used to scavenge the last oxygen atoms from the atmosphere around the component to be brazed. It must be clear that although feasible such a process is difficult to carry out. That’s why vacuum brazing is a less commonly employed technique than brazing with fluxes.
The vacuum aluminum brazing process is usually a relatively short cycle due to the fast pumping and heating characteristics of the furnace, the excellent temperature uniformity at soak temperatures, and the high thermal conductivity of the aluminum parts being brazed. Figure 1 shows a typical vacuum aluminum brazing cycle.
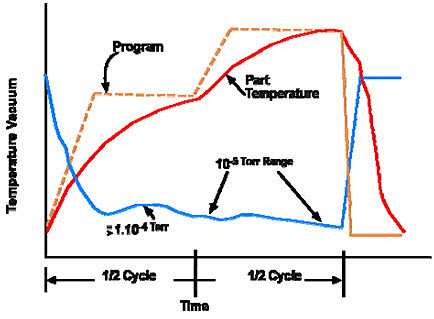
Figure 1: Typical Vacuum Aluminum Brazing Cycle
Benefits of Vacuum Aluminum Brazing
Brazing has many advantages when compared to other metal joining processes. Given that brazing does not melt the base metal of the joint, it allows for more precise control of tolerances and provides a clean joint with no need for additional finishing. The meniscus (crescent shaped) formed by the filler metal in the brazed joint is ideally shaped for reducing stress concentrations and improving fatigue properties.
Ideal situations for brazing:
- Joining parts of very thin or thick cross sections
- Compact components containing many junctions to be sealed (e.g. heat exchangers) or deep joints with restricted access
- Joining dissimilar metals such as copper and stainless steel
- Assemblies with a large number of joints specifically, vacuum aluminum brazing minimizes distortion of the part due to uniform heating and cooling as compared to a localized joining process.
Vacuum aluminum brazing is ideal for oxidation sensitive materials; vacuum brazing is considered a flux-free process that eliminates corrosive flux residue. Post-brazed parts are clean with a matte grey finish. The process is relatively nonpolluting and no post-braze cleaning is necessary.
Examples of Vacuum Aluminum Brazed Parts Examples of vacuum aluminum brazed parts often include heat exchangers, condensers, and evaporators used in automotive, aerospace, nuclear, and energy industries. Some of these parts are shown in Figures 2, and 3.
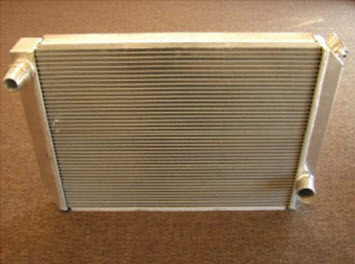
Figure 2: Vacuum Aluminum Brazed Radiator
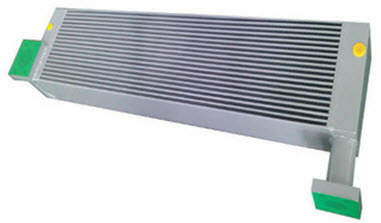
Figure 3: Aluminum 3003 vacuum brazing fin plate radiators
Types of Vacuum Aluminum Brazing Furnaces
Typical vacuum aluminum brazing furnaces are either singlechamber (batch type) or multiple-chamber (semi-continuous). Batch type furnaces are usually loaded horizontally, but can be designed for a vertical loading operation. Semi-continuous furnaces are horizontally loaded and are typically automated using load carriers and external conveyor systems.
Batch furnaces tend to be simpler in design (one loading/unloading door) than semi-continuous furnaces, less expensive, and easier to maintain. Semi-continuous furnaces have higher production rates because of the multi-chamber design and operate more efficiently by not having to cool heating zones or heat cooling zones. Example of batch type and semi-continuous type furnace is shown in Figure 4.
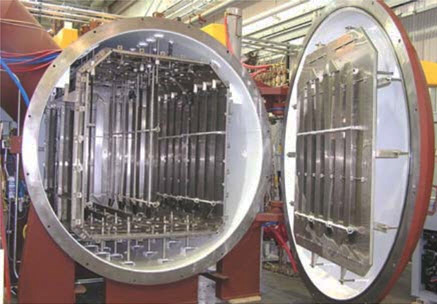
Figure 4: Batch Vacuum Aluminum Brazing Furnace Benefits
- Excellent for Liquid Flow Through (LFT), high density fin and heat exchanger applications
- Conducive to lanced offset fin stock and other high surface area cooling approaches
- Higher pressure and hermetic seal capability even in thin wall designs
- Can combine with various welding processes or structural bonding for design flexibility
- Fluxless process eliminates potential corrosion issues
- High batch rate oven runs depending on size and configuration