Abstract
Sub-Liquidus Casting is one of many known semi-solid metal technologies and holds great value offering grain refinement accompanied by proper control of melt temperature and cooling rate.
Some key advantages include improved tool life and time savings through quicker solidification.
Semi-solid metal (SSM) technology is different from the conventional forming processes which uses either solid or liquid metals as the starting material. This process deals with slurries, which in principle, can be produced in any material systems where liquid and solid phases coexist over a freezing range. The SSM process has advantages over other casting processes which are associated with less porosity and shrinkage voids, lower processing temperature and shorter time, less mold erosion, faster cycle time and longer die life.
Semisolid processing consists of two or three stages. First, a globular structure within the semisolid alloy is created. Then the semisolid slurry is used either directly for applications that require slurry (rheocasting) to form a component with near-net shape or be solidified as billets for later reheating during thixocasting.
There is a wide range of (SSM) processes patented or under investigation within research and development centers worldwide.
One of them is the Sub-Liquidus Casting (SLC) process. The process was developed by THT Presses Inc., USA, and explores a phenomenon of grain refinement accompanied by proper control of melt temperature and cooling rate.
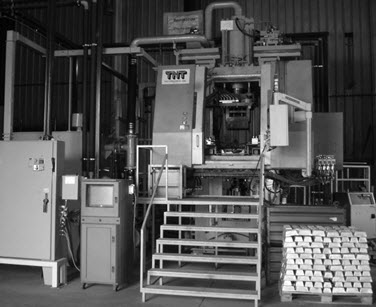
Figure 1: 400t THT press machine In fact, the successful process cycle can only be implemented if good grain refinement is achieved in the molten alloy supplied to the machine. The grain refined material is poured into the shot sleeve at temperatures just above liquidus and cooled to a semisolid state before transfer to the mold. For practical reasons, a superheat of 5–10°C is used to compensate for heat losses during alloy transfer from the furnace to the shot sleeve.
The slurry is developed within the shot sleeve, which means that no slurry processing equipment is required outside of the casting machine (Figure 2). For aluminum alloy A356 the temperature in the chamber before injection is between 570°C and 590°C. For proper grain refinement, fine rosettes transform into globules within seconds while coarse dendrites in poorly refined alloy would require more time to transform into globular features.
Although the machine features alone do not constitute the entire process, the specific features allow its proper implementation. They include large and shallow shot diameter and short stroke as well as a unique gate plate. The shot piston and sleeve wall temperatures are controlled to extract the heat primarily through the piston and less through the shot sleeve walls. The melt is transferred to the die cavity at very low velocity of the order of 1 m/s–2 m/s through a gate plate with multiple gates.
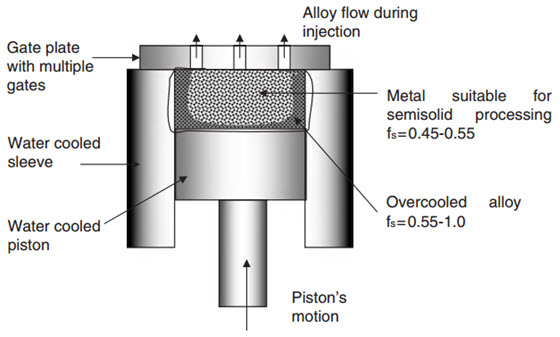
Figure 2: The concept of sub-liquidus casting (SLC) developed by THT Presses Inc. The advantages and requirements of sub-liquidus casting (SLC) are summarized as follows:
SLC advantages:
1) Breakway gates
2) Less sensitive to:
• Microstructural effects on properties
• Metal flow in die cavity and entrapment of bubbles
• Directional solidification
3) Less thermal input to die (~50% less)
• Longer tool life (2-5 times)
• Quicker solidification
SLC Requirements:
1) Grain refinement
2) Melt temperature (in furnace)
3) Melt cooling in shot sleeve
4) Time to develop slurry structure
5) Melt flow into die cavity
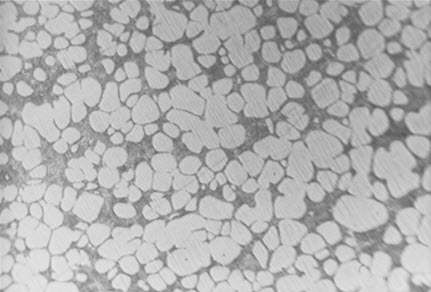
Figure 3: Typical A356 alloy SLC microstructure (x100)