Abstract
Laser beam welding provides a large number of quality advantages including speed, accuracy, good consistency in the joint properties.
One relatively new area for laser beam welding is in the welding of magnesium alloys. So far indications are positive with deep penetration welds in cast magnesium being possible with relatively low laser power.
There are many laser welding parameters affecting the welding quality. Laser power, welding speed, focal position, shielding gas flow, laser pulse frequency etc. are consid-ered as the base laser welding parameters that should be optimized for high welding quality.
Unsuitable welding parameters result in many defects such as an unstable weld pool, substantial spatter, tendency for drop-through for large weld pools, sag of the weld pool, undercut, porous oxide inclusions, loss of alloying elements, liquation and solidification cracking. On the other hand in order to achieve optimum welding in production both welding quality and productivity should be optimized.
Titanium and titanium alloys are widely used in space, aerospace, ship and chemical, nuclear energy and medical industries, because of many advantages such as low specific weight, high strength, excellent corrosion resistance, attractive fracture behavior and high melting point. Weldability of commercial pure titanium and most titanium alloys is good in general, although special cares must be taken during the welding process because pure titanium and titanium alloys are highly susceptible to contamination from atmospheric gases.
Laser welding of titanium alloys has advantages because of low heat input, especially compared to arc welding processes, resulted in low distortion, minimizing the shrinkage and residual stress of joints and ensuring excellent mechanical properties of joints. The disadvantages of laser butt welding is the difficulty of the joint fit up, which requires extreme precision along the edges to be welded. Laser welding is one of the most modern of all metal and alloy joining processes and, thanks to its technological and economical features, laser welding becomes more and more competitive to conventional arc welding processes, even to electron beam welding.
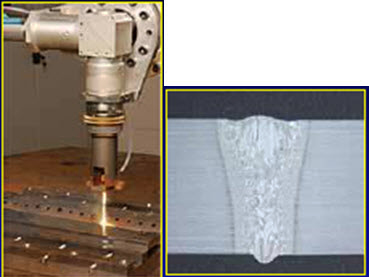
Figure 1: Laser beam welding of titanium alloy
While magnesium alloys are considered to be readily weldable by conventional arc and resistance welding techniques, it is recognized that for alloys with more than 1 per cent zinc, hot shortness may be produced which may result in weld cracking. In addition, a number of magnesium alloys are susceptible to stress corrosion cracking and could only be considered for use after stress relieving has been carried out. For work hardened alloys, the strength in the fusion zone may be lower than in the parent material as a result of the recrystallisation that takes place during welding.
Filler wire may be used in gas metal arc welding or gas tungsten arc welding to avoid crack sensitivity, particularly in Mg alloys containing Al. ER AZ61A is often preferred when welding wrought alloys of this type while ER AZ92A has been found to lower crack sensitivity in Mg-Al-Zn and Mg-Al cast alloys.
Laser beam welding has not been widely applied to magnesium alloys. Baeslack et al. laser welded a high strength magnesium casting alloy (5 wt% Y, 2 wt% Nd) and had problems with heat affected zone liquation cracking. Chen et al. were able to obtain deep penetration welds in cast magnesium (4.5 mm at 1 kW) with relatively low laser power. Recently, Niemeyer et al. have laser welded magnesium alloys (including AZ31B) with Nd:YAG and CO2 lasers. They were able to produce sound welds with minimal undercut using a CW Nd:YAG laser.
The autogenous welds exhibited little change in hardness but had only about one third the tensile ductility at room temperature. Deep drawing the laser welded sheets was still possible at elevated temperatures. This study examines the conditions for laser beam welding of AZ31B-H24 magnesium alloys in more detail. Welds were carried out with Nd:YAG and CO2 lasers. Absorptivity effects on threshold irradiances and weldability of butt joints were examined. Weld hardness profiles were determined and compared with the microstructure of the weld and heat affected zone. Chemical analyses of the weld were carried out to determine loss of alloying elements and oxidation. The results augment the magnesium laser welding work of Niemeyer et al.