Abstract
Laser beam welding effectively uses energy from the laser beam itself to melt and join the same metals and also dissimilar metals to one another.
Some of the main advantages of laser beam welding are its rapid speed (up to 10 times faster than TIG welding), highly repeatable results, accuracy to allow for problematic deep narrow welds to be completed.
Laser beam welding is a fusion joining process that uses the energy from a laser beam to melt and subsequently crystallize a metal, resulting in a bond between parts. Laser beam welding can be successfully used to join many metals to themselves as well as to dissimilar metals. Main applications are related to welding steels, titanium, and nickel alloys.
When the laser beam makes contact with the metal(s), the energy is converted from light to thermal energy. Concentrating the laser on an area as small as 0.2 mm in diameter, the heating effect is magnified greatly. Providing the laser power is calibrated correctly, the weld area (where the two pieces meet) will melt and then crystallize, fusing the parts together. If the laser is too powerful the laser may heat the material beyond the point of vaporization and simply slice straight through it. It is therefore important that the laser beam be set up to operate for the specific application being considered.
The action of the laser beam that leads to the formation of a welding cord can be decomposed following the stages below (Figure 1):
- the material is first heated by conduction;
- the absorbed energy provokes, by superficial penetration, the melting of the alloy on the impact surface;
- the operation takes place by emitting a metallic vapour which develops at the centre of the impact point. The material partly absorbs and diffuses the energy of the beam;
- the vapour pressure increases and dispels the melting alloy to the periphery of the beam and upwards. A narrow (capillary) shaft is created, which then propagates through the material. This shaft, whose diameter is barely greater than that of the beam, is physically occupied by metallic vapour plasma. Its walls are coated with a film of melting metal maintained by capillarity;
- the melting metal is finally sent backwards and closes the capillary that forms the welding cord (Figure 2).
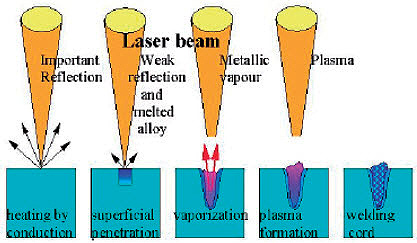
Figure 1: Stages of welding cord formation
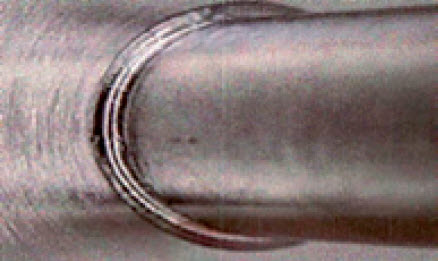
Figure 2: Welding cord by continue welding
Advantages of laser beam welding
High productivity (nearly 10 times faster than TIG).
- Low heat input and therefore low distortion.
- Ease of automation for repeatability.
- No need for filler wire, thus reducing costs.
- Similar and dissimilar metals can be welded easily.
- Clean weld joints.
- Deep and narrow welds can be done.
- Absence of distortion in welds created.
- Minimal heat affected zones in welds created.
- Excellent metallurgical quality will be established in welds.
- Ability to weld smaller, thinner components.
- Increased travel speeds.
- Non-contact welding.
Disadvantages of Laser Welding
- Slow welding speeds (25-250 mm/min).
- Rapid cooling rate cause problems such as cracking in high carbon steels.
- High equipment costs.
- Very high reflectivity of a laser beam by the metal surface.
- High equipment cost.
- Require precise joint and laser beam alignment.
Applications of Laser Welding
Used in electronics industry for applications such as connecting wire leads to small electronic components, to weld medical equipment, transmission components in automobiles and in cladding process.