Abstract
What would an ancient craftsman think if he saw a complex metal part take shape before his eyes in a small cabinet? He would likely think he was witnessing magic.
That kind of magic is commonplace these days, as more companies market machines that use high-powered lasers and metallic powders to produce items directly from computer-aided designs.
Selective Laser Melting (SLM) is an Additive Manufacturing (AM) process that can produce near-net shape products from metallic powders, in a layer-by-layer fashion, directly from three-dimensional Computer-Aided Design (CAD) models. Besides being capable of printing complex geometries and allowing shorter manufacturing times, SLM is also capable of using different grades of steel, non-ferrous metals, ceramics, smart materials and even multiple materials in the same component. Parts produced by SLM can achieve near-full density, as the powders are fully melted and fused together during the process. SLM fabrication with materials such as 316L stainless steel, Ti6Al4V, Inconel 718 and AlSi10Mg has achieved relative densities of 99% or higher. This has allowed SLM to be applied in the fields of medicine and aerospace.
A simplified schematic of a typical SLM setup is shown in Figure 1. During the SLM process data is provided from a CAD model, which is then virtually sliced into thin layers. A plan for each layer is made automatically, resulting in appropriate scan paths. Through the scanner mirrors, a laser beam selectively scans and melts the powder that covers the surface of a substrate, according to the developed scan paths. After a layer is finished, the building platform is lowered by an amount equal to the layer thickness, and a new layer of powder is deposited. The process repeats until the completion of the whole part.
As mentioned above, to date, the SLM process has been able to fabricate metallic parts from different material powders, such as titanium alloys, nickel-based superalloys, aluminum alloys and stainless steels. Although the SLM process offers great advantages, such as manufacturing complex parts using less material, it is affected by many factors, such as laser energy input and scan speed, scan strategy, powder material, powder size and morphology. The SLM process involves complicated physics, such as absorption and transmission of laser energy, rapid melting and solidification of material, microstructure evolution, flow in a molten pool, and material evaporation. As a result of all these factors, the process tends to form defects like porosity, incomplete fusion holes, cracks, and impurities. These defects are detrimental to a fabricated part in terms of its mechanical and physical properties. These factors have so far limited the application of selective laser melting.
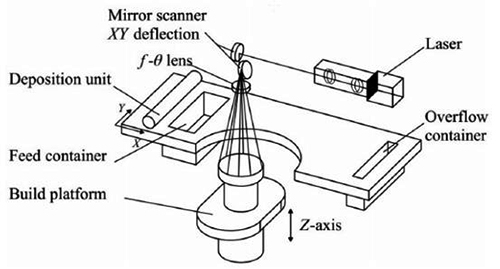
Figure 1: Schematic layout of a typical SLM setup
Benefits of SLM
Allows for complex geometries (e.g. tool inserts with conformal cooling channels)
Ideal process for prototyping
Reduces amount of material used
Best suited for
Low-volume fabrication
Complex parts
Materials for SLM
Titanium Ti-6Al-4V
Tool steel (1.2709)
Aluminum alloys
Stainless Steel 316L
Inconel 718
Industries for SLM processes
- Automotive
- Engineering
- Medical and dental technology
- Tooling
- Aerospace
- Motor sports
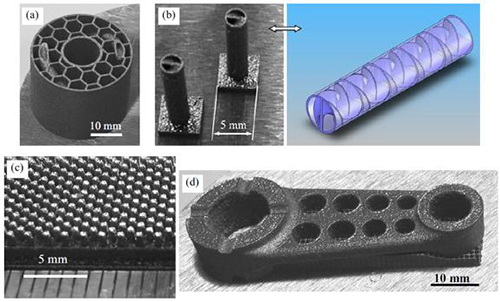
Figure 2: 3D models and functional prototypes with a complex geometry fabricated by SLM: (a) light-weight model with complex inner structure and two spiral cooling channels from SS grade 316L powder; (b) Kenics mixing element with a diameter of 3 mm and height of 15 mm and (c) sample with developed structure (pin diameter is 400 μm, height is 1 mm) from SS grade 904L powder; (d) part of combustion engine from Inconel 625 powder