Abstract
Most commonly known for their excellent strength, corrosion resistance and low density, titanium alloys are a key material for important applications in the aerospace and medical industries.
The covered experiments in this paper show that the second heat treatment of the alloys is most influential in increasing hardness of the finish material.
The study of S. Tanaka, T. Morita and K. Sinoda was conducted to investigate the effects of short-time duplex heat treatment on the microstructure, mechanical properties and fatigue strength of α+β titanium alloy Ti-6Al-4V. The duplex heat treatment was composed of short-time solution (STQ) treatment (1203 K, 60 s) and short-time (STA) aging (753-903 K, 40 s). The first heat treatment transformed a part of prior β phase to acicular α' martensite phase. The second heat treatment precipitated fine α phase in metastable β phase. These change in microstructure increased the hardness of prior β phase. At the same time, the tensile strength and fatigue strength greatly improved without reduction in ductility and their maximum improvement rates reached 29% and 22%, respectively.
2. Materials and Experimental Procedures
Table 1 shows the chemical composition of Ti-6Al-4V used in this study. The material was supplied as round bars (diameter: 14 mm) and machined to the three specimen shapes shown in Figure 1. For the short-time solution treatment, the specimens were kept at 1203 K for 60 s and quenched.

Table 1: Chemical composition of Ti-6Al-4V alloy used in this study (mass %)
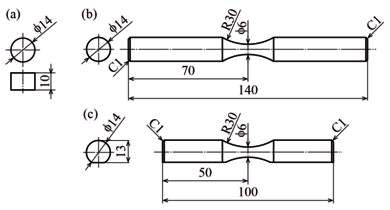
Figure 1: Specimen shapes (mm): (a) button specimen; (b) tensile specimen; (c) fatigue specimen
They concluded that through STQ and STA duplex heat treatment, the improvement rates of the tensile strength and fatigue strength reached 29% and 22%, respectively. The subject of the investigation of Y-K Chou et al., was to compare the mechanical properties of two-step as well as one-step aging treatments for Ti-15V-3Cr-3Sn-3Al specimens.
Ti-15-3 alloy in a sheet form with a thickness of 3.0 mm was used in this study. The chemical composition of the alloy in weight percent was %V=15.1, %Al=3.05, %Cr=2.92, %Sn=2.99, %Fe=0.071, %O=0.12, %C=0.016, %N=0.014 and %S=0.021, with a balance of titanium. The as-received material was in the solution-annealed condition and had the β-transus temperature of about 760°C. The aging treatments were performed at the temperature range from 317 to 593°C for 8 h in vacuum, followed by argon-assisted cooling to room temperature. For the one-step aging treatment, the specimen was identified with a designation of the three-digital numbers (aging temperature in °C) prefixed with a capital letter A. In the case of the specimens subjected to the two-step aging treatment, a capital letter D was added in front the first aging temperature and the second aging temperature was kept at 426°C for 24 h. For example, the designation A482 represented that the specimen was directly aged at 482 for 8 h; the D538 specimen represented the specimen which was aged first at 538°C for 8 h then at 426°C for 24 h. Mechanical tests such as tensile and notched tensile tests were carried out at room temperature. The tensile tests were conducted on a MTS machine at a strain rate of 6.67 x 10-4 s-1, corresponding to a crosshead speed of 1 mm/min. The notched tensile tests were performed at a constant displacement rate of 1.0 mm/min. After testing, the macro-fracture appearance and fractographic examinations of various specimens were conducted using a Hitachi S4100 scanning electron microscope (SEM). For detailed microstructural observations, thin foil specimens were prepared by a standard jet-polisher and then examined with a transmission electron microscope (TEM).
The as-received material in the solution-annealed condition consisted of equiaxed β grains without any observable precipitates (Figure 2).
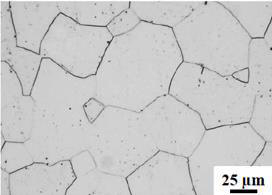
Figure 2: Optical microstructure of the Ti-15-3 base material
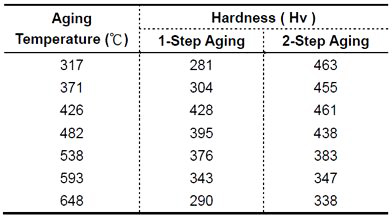
Table 2: Aging temperature and hardness relationship of theTi-15-3 specimens
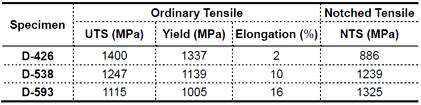
Table 3: Mechanical properties of two-step aged specimens
As conclusions are drawn that:
Regardless of the first aging temperature used in the two-step aging process, the second aging treatment at 426°C/24 h would further increase hardness of the Ti-15-3 alloy but had different degrees. The limited amount of α precipitates during the second step aging (426°C/24h) caused a minor increase in hardness of the D538 and D593 specimens. The low ductility of the D317, D371 and D426 specimens was responsible for the high notch brittleness or low NTS of the material.