Abstract
Magnesium alloys are widely, and increasingly used in some key industrial sectors such as the automotive and aerospace industry and can be particularly associated with providing possibilities for meeting ever increasing light weighting requirements.
Key to wider the application of magnesium alloys are the relative advancements that can be gained through a range of process improvements which can have a direct impact on microstructure and surface microhardness to improve overall material performance.
In the paper of the T. Tański, L.A. Dobrzański, R. Maniara was presented the investigation of structure of the MCMgAl9Zn1, MCMgAl6Zn1 magnesium alloys in its as cast state. The chemical composition of the investigated materials is given in Table 1.

Table 1: Chemical composition of magnesium alloys
As a result of metallographic investigations made on the light and scanning microscopes it has been confirmed that the magnesium cast alloys MCMgAl9Zn1 in the cast state are characterized by a microstructure of the solid solution α constituting the alloy matrix as well as the γ – Mg17Al12 discontinuous intermetallic phase in the forms of plates located mostly at grain boundaries (Figures 1, 2). Moreover, in the vicinity of the γ intermetallic phase precipitations the presence of the needle eutectics (α + γ) has been revealed (Figures 1a, 2a). In the structure of the examined magnesium cast alloys one can observe, apart from Mg17Al12 precipitations, turning grey-green phases, characterized by angular contour with smooth edges in the shape of hexahedrons. Out of the chemical composition examinations with the use of the EDS dispersive radiation spectrometer as well as literature data, one can conclude that it is the Mg2Si compound which, when precipitating, increases the hardness of castings (Figures 1b, 2b).
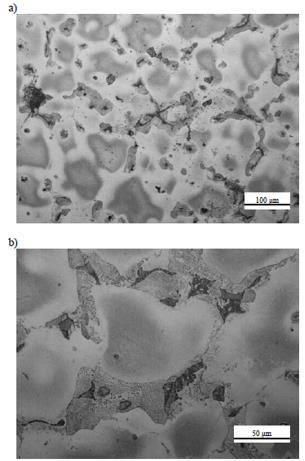
Figure 1: Microstructure of MCMgAl6Zn1 magnesium alloys in as-cast state
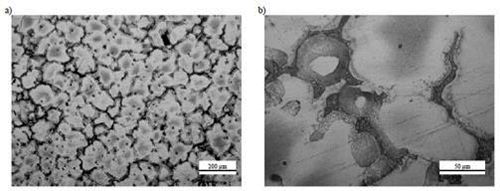
Figure 2: Microstructure of MCMgAl9Zn1 magnesium alloys in as-cast state
The aim of Leszek Adam Dobrzanski et al study was to improve the surface layer properties of the Mg-Al-Zn cast magnesium alloys by melting and feeding of TiC, VC, WC, SiC, NbC and Al2O3 particles onto the surface. Laser processing was carried out using high diode power laser (HDPL). A series of experiments was carried out with varying scan rates and laser power. The resulting surface layers were examined using microhardness measurements and corrosion resistance tests. Mg-Al-Zn alloys after laser treatment are characterized by two zones: alloyed zone (AZ) and heat affected zone (HAZ) with different thickness and shape depending on laser power and ceramic powder used. Alloyed zone is composed mostly of dendrites with the Mg17Al12 lamellar eutectic and Mg in the interdendritic areas. The increase of microhardness from about 50 HV0,1 to about 200 HV0,1 in alloyed zone were observed.
Microhardness, test results, depending on distance from surface (Figure 3), has shown that microhardness increases in the surface layer. The increase of hardness in the alloyed zone is resulting from considerable structure refinement of magnesium containing phase (100-300 HV0,1) and very hard carbides particles (about 1500-1600 HV0,1) occurrence in this area. Values between 300 and 800 HV0,1 are connected with the inuence of carbide and oxide particles on the microhardness of the areas near to the hard particles. Increase of alloying particles quantity causes also the increase of microhardness of alloyed surface.
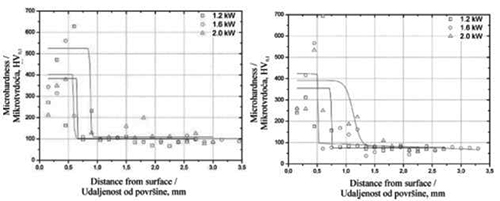
Figure 3: Cross-section microhardness prole from the surface: a) MCMgAl12Zn1 alloy, b) MCMgAl6Zn1 alloy alloyed with SiC powder, scan rate: 0.75 m/min
Surface layer examinations confirm that it is possible to carry out surface layer alloying of the cast magnesium alloys using the HPDL high power diode laser with beam power values in the range of 1.2÷2.0 kW and with an alloying feed rates of 0.25÷1.0 m/min. Laser alloying of the TiC, VC, WC, SiC carbides and Al2O3 oxide powders, whose melting points are much higher than the melting points of the investigated alloys, causes inundation of the non-dissolved powder particles into the molten substrate. Strong circulation of the molten metal occurs, followed by sudden solidification when the laser beam has passed. The width of the surface layer increases with the applied laser power increase.
Alloyed area is composed of dendrites with the Mg17Al12 and Mg lamellar eutectic in the interdendritic areas, whose main axes are oriented according to the heat transfer directions. A lack of dissolution of carbide and oxide particles during laser alloying process and microhardness increasing of the alloyed zone were revealed. These results lead to an conclusion that laser surface treatment of Mg-Al-Zn alloys should be further developed and investigated particularly for instance for large surface elements application.