Abstract
This article examines the annealing process of aluminum and aluminum alloys, with particular focus on the 6061 Al alloy. The research investigates the effects of heat treatment on microstructure evolution in ultrafine-grained samples fabricated through differential speed rolling (DSR). Through detailed analysis of microhardness, softened fraction, and microstructural changes across various annealing temperatures (150-400°C), the study demonstrates the transformation from lamellar to equiaxed grain structure. Key findings reveal that annealing temperatures significantly influence grain size, shape aspect ratio, and boundary misorientation angles, with optimal recrystallization achieved at 350°C.
Understanding Aluminum Alloys: Properties and Industrial Applications
Aluminum (Al) alloys have become increasingly vital in automotive, marine, and aerospace industries due to their exceptional material characteristics. These alloys offer a unique combination of properties, including low specific gravity, high strength-to-weight ratio, superior wear resistance, and excellent thermal and electrical conductivity. Additionally, their low melting point, minimal gas solubility (except for hydrogen), outstanding castability, and strong corrosion resistance make them ideal replacements for traditional materials like steel and cast iron in many applications.
Recovery, Recrystallization, and Grain Growth Processes
Recovery Phase
During recovery, the material undergoes initial structural changes where dislocations reduce primarily at the grain fragment centers. This reduction creates a subgrain structure with distinct networks of dislocations at the subgrain boundaries. As heating time and temperature increase, the polygonization becomes more refined, and subgrain size gradually expands. While recovery provides initial property changes, complete restoration from cold working effects requires full recrystallization.
Recrystallization Process
Recrystallization marks the formation of a new, microscopically observable grain structure. The resulting structure exhibits minimal internal strain, with few dislocations within the grains and minimal concentrations at grain boundaries. This process represents a crucial transition in the material's microstructure.
Post-Recrystallization Grain Growth
Following recrystallization, continued heating can lead to grain coarsening through various mechanisms.
Experimental Study of 6061 Al Alloy
A significant research investigation by Young Gun Ko and Kotiba Hamad examined heat treatment effects on ultrafine-grained 6061 Al alloy processed through differential speed rolling (DSR). The study utilized:
- Two-pass DSR with 75% thickness reduction
- Speed ratio of 1:4
- Various annealing temperatures (150-400°C)
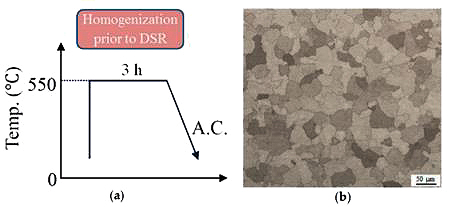
Figure 1: Homogenization conditions and resultant microstructure
The chemical composition of the studied 6061 Al alloy included:
- 0.9% Mg
- 0.71% Si
- 0.5% Fe
- 0.24% Cu
- 0.19% Cr
- Other elements in smaller quantities
- Balance: Aluminum
Results and Analysis of Heat Treatment Effects
Microhardness and Softening Behavior
The study revealed three distinct phases in microhardness evolution across temperature ranges. During the initial recovery phase up to 225°C, the material exhibited only slight decreases in microhardness, with minimal structural changes as recovery processes dominated. The critical transformation zone between 225-350°C showed a sharp decrease in microhardness accompanied by significant material softening, marking the primary recrystallization period. Finally, above 350°C, the material entered a stabilization phase where microhardness values leveled off, indicating completion of primary recrystallization.
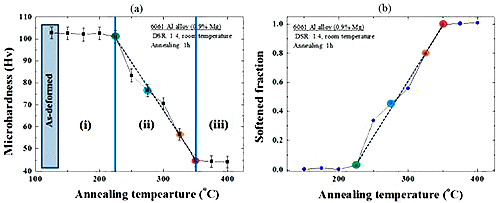
Figure 2: Microhardness and softened fraction graphs
Microstructural Evolution Analysis
The transformation of the material structure was meticulously documented through EBSD mapping at key temperature points. The analysis revealed progressive changes throughout the heating process:
The sample at 225°C showed initial breakdown of lamellar structure with approximately 18% recrystallization, marking the early stages of structural transformation. By 275°C, while some original lamellar structure remained, approximately 31% recrystallization was achieved with visible transition to equiaxed grains.
Key improvements were observed at higher temperatures:
- 325°C yielded enhanced structural refinement with 52% recrystallization
- 350°C achieved maximum transformation with 84% recrystallization
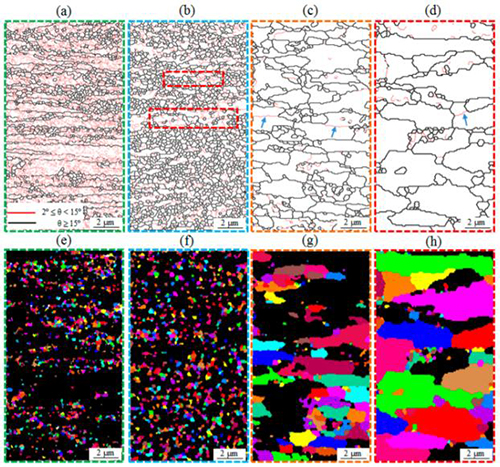
Figure 3: EBSD maps and recrystallized microstructures
The progressive increase in recrystallized fraction demonstrated a direct correlation with the observed decrease in microhardness values. This relationship was particularly evident in the 350°C samples, which exhibited the optimal microstructural configuration and lowest microhardness values.