Abstract
Additive manufacturing is a relatively recent manufacturing method which has become a key area of interest in multiple industrial sectors.
Some of the most prominent benefits of AM include very low energy consumption, reduced waste, and a reduced time to market, to name but a few.
Interest in additive techniques has grown swiftly as applications have progressed from rapid prototyping to the production of end-use products. Additive equipment can now use metals, polymers, composites, or other materials to “print” a range of functional components, layer upon layer, including complex structures that may be difficult or impossible to manufacture by other means.
Benefits of Additive Manufacturing
Additive manufacturing and traditional manufacturing face different trade-offs, with each process likely to play a role in the deployment of manufacturing capabilities. AM has the potential to vastly accelerate innovation, compress supply chains, minimize materials and energy usage, and reduce waste. Below, we list some benefits of AM technology:
• Lower energy consumption: AM saves energy by eliminating production steps, using substantially less material, enabling reuse of by-products, and producing lighter products.
• Less Waste: Building objects up layer by layer, instead of traditional machining processes that cut away material can reduce material needs and costs by up to 90%. AM can also reduce the “cradle-to-gate” environmental footprints of component manufacturing through avoidance of the tools, dies, and materials scrap associated with CM processes. Additionally, AM reduces waste by lowering human error in production.
• Reduced time to market: Items can be fabricated as soon as the 3-D digital description of the part has been created, eliminating the need for expensive and time-consuming part tooling and prototype fabrication.
• Innovation: AM enables designs with novel geometries that would be difficult or impossible to achieve using CM processes, which can improve a component’s engineering performance. Novel geometries enabled by AM technologies can also lead to performance and environmental benefits in a component’s product application.
• Part Consolidation: The ability to design products with fewer, more complex parts, rather than a large number of simpler parts – is the most important of these benefits. Reducing the number of parts in an assembly immediately cuts the overhead associated with documentation and production planning and control. Also, fewer parts mean less time and labor is required for assembling the product, again contributing to a reduction in overall manufacturing costs. The “footprint” of the assembly line may also become smaller, further cutting costs.
• Lightweighting: With the elimination of tooling and the ability to create complex shapes, AM enables the design of parts that can often be made to the same functional specifications as conventional parts, but with less material.
• Agility to manufacturing operations: Additive techniques enable rapid response to markets and create new production options outside of factories, such as mobile units that can be placed near the source of local materials. Spare parts can be produced on demand, reducing or eliminating the need for stockpiles and complex supply chains.
Applications of Additive Manufacturing
Interest in additive techniques has grown swiftly as applications have progressed from rapid prototyping to the production of end-use products. Additive equipment can now use metals, polymers, composites, or other materials to “print” a range of functional components, layer upon layer, including complex structures that may be difficult or impossible to manufacture by other means.
AM technology is currently in use in the following fields: jewelry, footwear, industrial design, education, transportation, consumer products and electronics, architecture, engineering, construction, geographic information systems, automotive, aerospace, dental and medical, government and military, industrial machinery, etc. New AM applications are continually being identified due to increased customer exposure and quality improvements. The primary applications for AM can be broadly broken into the areas of rapid prototyping, rapid tooling, and rapid manufacturing.
The development of innovative, advanced AM techniques has progressed rapidly in recent years, and expanded to a broader range of industry applications. Compared with conventional manufacturing, AM is particularly suitable for producing low volumes of products, especially for parts with complex geometries. AM processes also offer great potential for customization, such as fabricating personalized implants for hip and knee replacements. The AM market in 2013, consisting of all AM products and services worldwide, grew 34.9% to approximately $3 billion, according to Wohlers’ Report 2014. This compares to growth in 2012 of 32.7% to approximately $2.3 billion. In the 2014 edition of the report, Wohlers Associates conducted a survey of 29 manufacturers of professional-grade, industrial AM systems (those that sell for $5,000 or more) and 82 service providers worldwide. The survey asked each company to indicate which industries they serve and the approximate revenues (as a percentage) that they receive from each. Figure 1 shows the results. The “Other” category includes a wide range of industries, such as oil and gas, sporting goods, commercial marine products, and various other industries that do not fit into named categories.
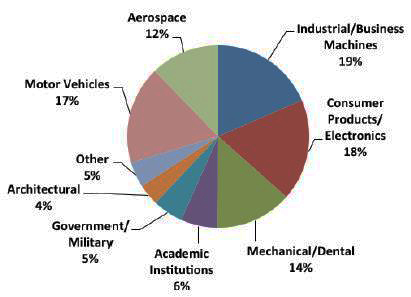
Figure 7: Industries served by AM Manufacturers and Service providers