Abstract
One of the earliest and most recognized adopters of adhesives to join metal parts was the aircraft industry who began using the available technologies during World War II.
Nowadays adhesive bonding is a commonly used technique for joining similar and dissimilar materials and whilst if offers great flexibility in design, the mechanics of the joints must be well understood.
Adhesive bonding is a reliable, proven and widely established technique for joining metals, plastics, composites and many other substrates. Metal bonding techniques were widely adopted and developed during and after World War 2 by the aircraft industry, from where they have subsequently spread to other sectors. Today, designers and engineers can choose between adhesive bonding, bolting, riveting, welding or soldering. In many cases the more cost-effective method will be bonding. Joints designed and bonded as recommended by Hexcel have several advantages over those made by traditional methods.
Bonding is the surface-to-surface joining of similar or dissimilar materials using a substance which usually is of a different type, and which adheres to the surfaces of the two adherents to be joined, transferring the forces from one adherent to the other. According to DIN EN 923, an adhesive is a nonmetallic substance capable of joining materials by surface bonding (adhesion), and the bond possessing adequate internal strength (cohesion). Bonding is a material joining technique that, in the traditional sense, cannot be broken without destruction of the bond. Recently, specific bondingon- demand techniques have been developed, for example as an assembly tool without further function, or for recycling based on a separation of materials, a method that today is becoming increasingly important.
Bonding is by far the most universal joining technique. Virtually all technically useful materials can be joined with each other, and one with another, by means of this surface-to-surface and material-joining technique.
Adhesive bonding technology offers great design flexibility as it can be easily integrated into almost all available industrial sequences of single-piece work or mass production. Historically, bonding has long been recognized as a high-performance joining technique. The large majority of original natural binding materials have now been replaced by synthetically prepared adhesives. For example, phenolic resins were first introduced in the late 1920s, while during the 1940s epoxide resins and polyurethane were developed which have since made possible the production of synthetic adhesives.
As polymer chemistry has advanced in terms of knowledge, specific adhesives have been developed that bind very strongly to organic or inorganic materials. With regard to adhesive strength and deformation, these adhesives meet very specific requirements that result from the configuration of the adhesive joint. Meanwhile, high-strength adhesive assemblies have been created with quite short curing periods. In fact, the longstanding problem of extensive curing times necessary to obtain high strength joints has been almost completely resolved with the introduction of new chemical developments in the creation of adhesives. Moreover, skepticism is no longer justified as to the long-term durability of adhesive joints exposed to adverse environments, provided that the bonding is properly conceived.
Design of adhesive joints
Loading conditions - stress Bonded joints may be subjected to tensile, compressive, shear and peel stresses, often in combination. Adhesives are strongest in shear, compression and tension. Cleavage and peel loading are the most taxing, concentrating the applied force into a single line of high stress. Generally joints with rigid adherent surfaces will fail in cleavage. A joint will fail in peel if at least one adherent surface is flexible.
Five basic stresses
Basic joint design: A bonded joint needs to be designed so that the loading stresses will be directed along the lines of the adhesive's greatest strengths. The design should reinforce the tensile, compressive and shear stresses. For maximum strength, cleavage and peel stresses should be designed out of the joints as far as possible.
Simple lap joint: On loading a simple lap joint, the main force resolves into a shear component along the plane of the interface with a peel component at right-angles. The stresses are highest at the edges of the bond causing strain and twisting.
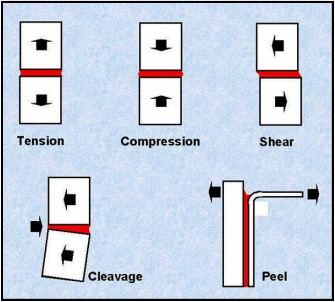
Figure 1: Five basic stresses Basic joint design: A bonded joint needs to be designed so that the loading stresses will be directed along the lines of the adhesive's greatest strengths. The design should reinforce the tensile, compressive and shear stresses. For maximum strength, cleavage and peel stresses should be designed out of the joints as far as possible.
Simple lap joint: On loading a simple lap joint, the main force resolves into a shear component along the plane of the interface with a peel component at right-angles. The stresses are highest at the edges of the bond causing strain and twisting.
The major advantages of adhesive bonding for steel applications are:
- the elimination of thermal distortion associated with welding;
- improved fatigue strength, especially in low and long-term loading conditions, due to low stress concentrations;
- the ability to create efficient complex joints, such as in sandwich structures;
- a reduction of pitting corrosion due to the absence of weld defects and the additional benefit of the adhesive acting as a sealant within a joint, thus minimizing crevice corrosion.
The main disadvantages of the use of adhesives are:
- some surface pre-conditioning is required to obtain strong and durable joints;
- it is difficult to combine the properties of maximum impact resistance and elevated temperature resistance in a single adhesive;
- long-term durability in wet/humid conditions is uncertain due to a shortage of design data at present;