Abstract
Defects and anomalies are an everyday challenge within the framework of foundry technologies. As demand for castings with very specialized applications rises, the issue of quality becomes more important.
The Rheo Casting process involves using slurry in a semi solid state with the amount of benefits directly linked to the fraction solid at the time of casting. Advantages can include a reduction in shrinkage and significantly reduced latent heat.
Within the framework of foundry technologies the presence of defects, anomalies and imperfections in the final product are an ever present reality. This cohabitation between process and quality issues is becoming more and more problematical because of the request of increased performance in castings, in order to produce a large series of components which often have very critical applications.
Voids or cavities are generated within a casting during solidification, caused by volume contraction, by poor feeding systems and/or gas (prevalently hydrogen) development. Generally, interdendritic shrinkage pores, inclusions, secondary dendrite arm spacing are privileged crack initiation sites, independently of the loading conditions. These parameters directly affect the mechanical performances of the alloy leading to a reduced strength and ductile properties, irregular crack development and in extreme conditions can cause the materials failure.
SSM-processing presents an alternative manufacturing route for aerospace, military and especially automotive components. Suspension parts, engine brackets and fuel rails for the automotive industry are being produced in Europe, whereas examples from the USA include mechanical parts for snowmobiles and mountain bikes. Asia has focused more on the production of electronic components such as electrical housing components and notebook cases with emphasis on magnesium alloys.
Rheocasting involves preparation of SSM slurry directly from the liquid alloy, followed by a forming process such as High Pressure Die Casting (HPDC). With “Rheo” processes the alloy is cooled into a semi-solid state and then is introduced into a die without the presence of an intermediate solidification step; semi-solid slurry with non-dendritic solid particles is produced from a fully liquid regular alloy. It is cooled to obtain the desired fraction solid and then it is cast into a part. Component shaping directly from SSM slurries is inherently attractive due to its characteristics, such as overall efficiency in production and energy management.
A critical advantage of rheocasting is the ability to cast the metal at a wide range of fraction solids. The majority of the process advantages of using nondendritic, semi-solid alloys are dependent on the amount of solid at the time of casting. Reduction of shrinkage, a decreased amount of latent heat, and the magnitude of viscosity are dependent upon and increase of the percentage of solid in the alloy.
However, as the fraction solid increases, semi-solid casting begins to deviate from conventional die casting processes. For the higher fraction solid material, a more powerful shot end is required on the die cast machine because of the much higher viscosity of the alloy. Additionally, the stroke of the piston is usually longer to accommodate the larger opening in the cold chamber. Casting cycle time is therefore shorter with high fraction solid casting, but more costly changes are required for the die casting machine to handle the more viscous material.
The Figures 1 and 2 present the schematic overview of rheo casting process and microstructure of rheocast A356 alloy.
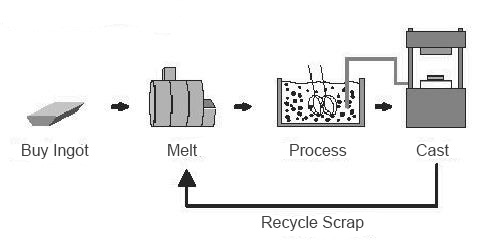
Figure 1: Rheo casting process
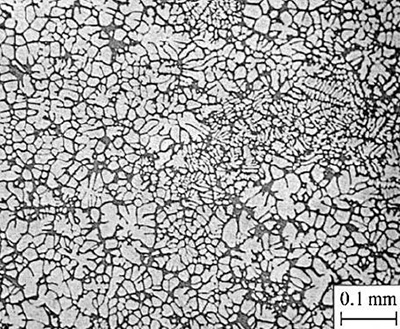
Figure 2: Microstructure of rheocast A356 alloy