Abstract
Ultrasonic Additive Manufacturing (UAM) is essentially a hybrid of two AM process; sheet lamination and Computer Numerical Control (CNC).
Due to its specific process parameters UAM has several distinct applications including the manufacturing of functionally graded materials, structurally embedded electronic systems and fiber reinforced metal matrix composites.
Ultrasonic Additive Manufacturing (UAM) is a hybrid sheet lamination/Computer Numerical Control (CNC) manufacturing process. UAM utilizes Ultrasonic Welding (UW) to bond thin metal foils in a layer-by-layer fashion and periodic CNC machining to create the desired 3D shape. The technology was first introduced by White under the name of Ultrasonic Consolidation. During the bonding step, a cylindrical textured machine tool, called the sonotrode, is pressed at a constant normal force against the metal foil, which is kept in place via a clamping or tensioning mechanism. The sonotrode rolls over the foil while oscillating at a constant frequency of approx. 20 kHz perpendicular to the direction of travel (see Figure 1).
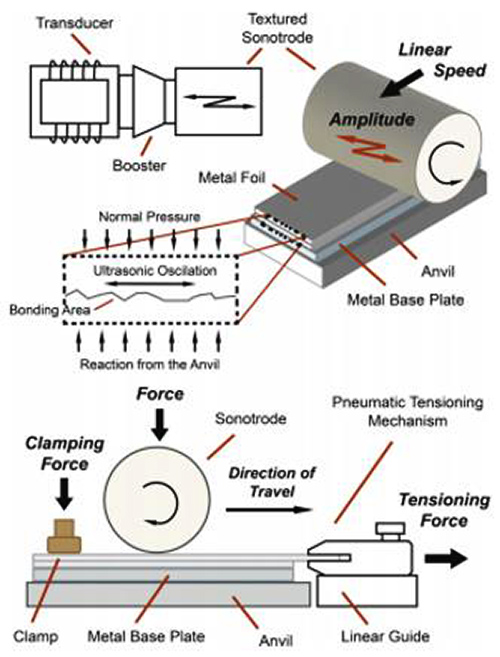
Figure 1: Schematic overview of Ultrasonic Additive Manufacturing (UAM)
Process parameters
UAM process parameters have a direct consequence on the quality of the final part. The important parameters in UAM are the ultrasonic amplitude (approximately 5-50μm), the applied normal force (500-2000N), the travel speed of the sonotrode horn (up to 50 mm/s), the texture of the sonotrode horn (Ra between 4 and 15 μm) and the substrate preheat temperature (up to 150°C). These parameters vary for different materials and need to be optimized for every material. The placement of foils and its orientation also play a major role in deciding the final properties of the part.
A commonly used parameter to represent the bond quality in UAM is linear weld density (LWD), which is given by:
LWD=Bonded interface length/Total interface length
Unbonded interfaces will show up as voids within the metal, parallel to the layering.
Applications of UAM
A. Functionally Graded Materials UAM can manufacture the FGM are used for the applications where high level mechanical as well as physical properties are required such as aerospace vehicle shields, rocket nozzles where the temperature reaches up to 2000°C. Other applications are the heat exchanger plates, lightweight armor plates for defense applications, heat engine components.
B. Structurally Embedded Electronic Systems In current industrial applications, the electric systems embedded in a solid enclosure or part are becoming essential so as to facilitate the portability, robustness and flexibility in the functioning. Thus UAM provides a single stroke method to produce better electrical applications such as embedded sensors and RFID, tamperproof electronics.
C. Fiber Reinforced Metal Matrix Composites UAM can be used to manufacture the MMC in which the matrix is a metal where as another component is fiber of Silicon Carbide (SiC) reinforced in the metal matrix. These fiber reinforced MMC manufactured by UAM are used I the applications such as airplane wing frames where the low weight and higher strength is expected. The F-16 Falcon fighting plane uses silicon carbide fibers in titanium matrix for structural components of the jet’s landing gear. Apart from these, other applications are golf clubs, fishing rods, brake parts, biological prosthetics etc.
Figure 2 shows the list of metal combinations that have been successfully tested in UAM.
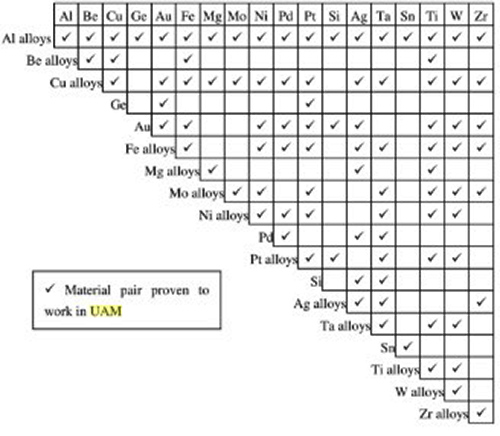
Figure 2: List of metal combinations proven to work in UAM