Abstract
Magnesium alloys are widely, and increasingly used in some key industrial sectors such as the automotive and aerospace industry and can be particularly associated with providing possibilities for meeting ever increasing light weighting requirements.
It is possible to increase the application of Mg alloys through alloying with other elements such as aluminum, zinc, copper, manganese, which will provide much improved mechanical performance of the material where required.
Magnesium (Mg) and its alloys are applied in different fields, such as the automotive and aircraft industries, as well as biomedical applications. Aluminum, zinc, copper, manganese, and silicon are among a variety of alloying elements added to magnesium. Some of these elements, such as aluminum and copper, improve specific mechanical properties. Aluminum is the most favorable alloying element as it forms a solid solution with magnesium, which can be used to improve the mechanical properties through heat-treatment procedures. Manganese is added to improve corrosion resistance, while silicon, along with the addition of calcium, improves high temperature properties, ductility, and creep resistance.
In the paper of L. Čížek, et al. investigation was made with use of cast plates (size 10x20x150 mm) of model alloy of the “Electron” type with the following chemical composition (weight %): Mg, Al-8.25, Zn-0.63, Mn-0.22, Si-0.035, Cu-0.003, Fe-0.014, Be-0.002, Zr-0.002, rest Mg. Samples for tensile test had a form of bar with length 115 mm, diameter 6 mm, in central part the diameter was reduced to 4 mm in the length of 30 mm. Samples as cast state and after heat treatment T4 (after ASTM) were used. Conditions at heat treatment: pre-heating 375°C/3h → heating 415°C/18h, cooling on air. Samples for ECAP method after application of heat treatment T4 and rolling were used for next investigation. Size of sample for ECAP method was 8 x 8 x 50 mm. Testing of mechanical properties was made on testing machine INOVA TSM 20. Temperature range of the equipment is up to 800°C. Heating to the required temperature is realised in 3 stages in argon atmosphere. Testing of mechanical properties of samples after ECAP method on INOVA TSM 50 was realized. Samples for tensile test after ECAP had a form of plate and measured size of sample was 3 x 12 x 1.5 mm. Total length of sample was 40 mm.
Results of measurement of elastic-plastic properties of cast alloy by tensile test in dependence on temperature are summarised in the Figure 1. and alloy after T4 in Figure 2.
This Figure shows that values of Rm swiftly decrease with increasing temperature of the test. In other measured values there was registered initial growth with indistinctive maximum in temperature zone of approx. 250°C for work to rupture, and approx. 3000°C for elongation and reduction. After achieving of the maximum there follows sharp fall, at the highest temperatures the achieved values are mostly lower than the values at the temperature of 200°C. In Figure 2. values of Rm at ambient temperature is significant higher than in the case of initial alloy. The temperature dependence is similar, but decreasing of Rm is started at lower temperature than in the case of initial alloy. This phenomenon is probably connected with dissolvability of intermetalic phase Mg17Al12 in the case of initial alloy during of testing. Tensile test of samples after ECAP method was made at 250°C with strain rate 1.10-4s-1. This temperature on the base of previous measurement was selected from the reason of best plasticity.
The results of this testing were following: Tensile strength Rm = 35 MPa and percentage elongation was 250%. Percentage reduction from the reason impossibility of correct fracture area measurement was approximately determined 400%.
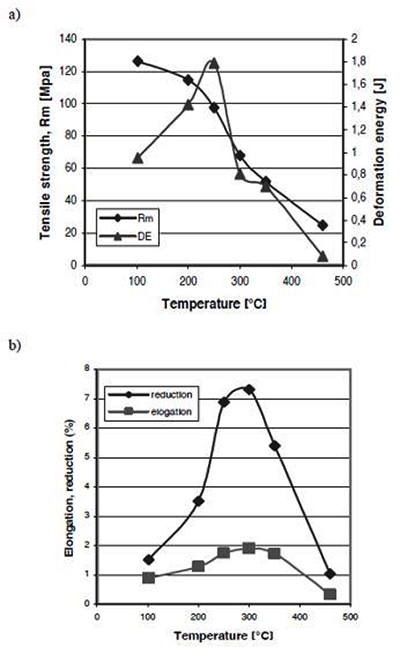
Figure 1: Temperature dependence of mechanical properties alloy AZ91 as cast state: a), b)
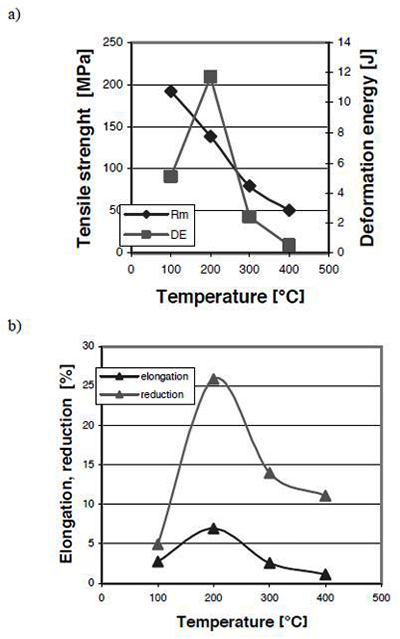
Figure 2: Temperature dependence of mechanical properties alloy AZ91 after heat treatment: a), b)