Abstract
Furnace brazing represents an advanced industrial joining technique suitable for high-volume production. This process involves heating entire assemblies to the braze alloy's melting point, enabling simultaneous production of thousands of joints. The article examines the process principles, advantages, and critical considerations for successful implementation. Key benefits include precise tolerance control, ability to join dissimilar materials, and minimal thermal distortion, though the process requires careful attention to base-metal cleanliness and joint design.
Introduction to Brazing Technology
Brazing is a specialized joining process utilizing a filler metal with a lower melting point than the materials being joined. By definition, brazing occurs at temperatures above 450°C; lower temperatures characterize soldering processes. In furnace brazing, entire assemblies are heated until the braze alloy melts and flows into joints through capillary action.
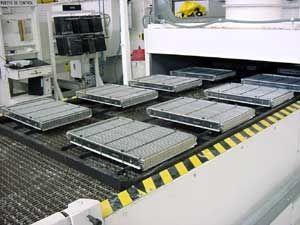
Figure 1: Belt conveyor brazing furnace
Common Brazing Methods
There are many heating methods available to accomplish brazing operations. The most important factor in choosing a heating method is achieving efficient transfer of heat throughout the joint and doing so within the heat capacity of the individual base metals used. The geometry of the braze joint is also a crucial factor to consider, as is the rate and volume of production required. The easiest way to categorize brazing methods is to group them by heating method.
Various heating methods serve different brazing requirements:
- Furnace brazing (including exothermic, hydrogen, argon, and vacuum atmospheres)
- Torch brazing
- Induction brazing
- Dip brazing
- Resistance brazing
- Infrared brazing
- Blanket brazing
- Electron beam and laser brazing
- Braze welding
Furnace Brazing Process Fundamentals
Process Characteristics
The process relies on capillary attraction to distribute molten filler metal throughout the joint. Filler metal placement occurs before components enter the furnace, with careful positioning on the furnace belt crucial for success.
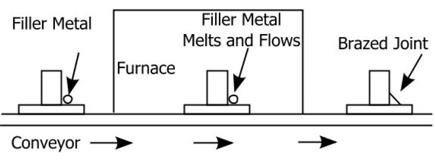
Figure 2: Schematic of furnace brazing process
Temperature and Time Considerations
Joint quality depends significantly on temperature control and timing. Higher temperatures enhance both alloying and wetting actions of the filler metal, with brazing temperatures necessarily exceeding the filler metal's melting point.
Advantages of Furnace Brazing
The process offers several benefits:
- Preserves base metal integrity
- Enables precise tolerance control
- Produces clean joints requiring minimal finishing
- Allows joining of dissimilar materials
- Reduces thermal distortion through uniform heating
- Facilitates cost-effective production of complex assemblies
- Supports automation and mass production
Process Limitations and Requirements
Key considerations include:
- Need for exceptional base-metal cleanliness
- Careful attention to design and manufacturing parameters
- Pre-production planning for components and assemblies