Abstract
Boronizing is a surface treatment by which boron atoms are diffused into the surface of the metal in quantities exceeding the solubility limit.
Hardness is improved and thus wear resistance increased as well as a number of other advantages such as corrosion and oxidization resistance.
Metallic parts, tools and equipment are exposed to several effects due to their running conditions. These effects are stress, impact, fluctuating stress, friction, corrosion and combinations of these phenomena. Metallic components must be more resistant to these effects so that they may continue to be in service for a long time. Surface properties, besides with the properties of the overall material, have a great importance in parts that are exposed to friction, wear, corrosion and oxidation in both low and high temperature conditions.
Thus, the improvement of the surface properties of metallic components has become an important subject in last decades. Boronizing is one of the treatments that are carried out to improve the surface properties of steels. The term boronizing is used to describe the diffusion of boron atoms into the surface of metal objects in a quantity exceeding the solubility limit, so that metal boride is formed.
Boronizing can be applied to many metals including all ferrous alloys, titanium alloys, nickel alloys, cobalt alloys, refractory metal (chromium, molybdenum, vanadium, niobium, tantalum, tungsten and zirconium) alloys, etc. Some non-metals like cemented carbides can also be boronized. Copper cannot be boronized since copper atoms act as a barrier preventing the absorption of the diffusing boron atoms. Boronizing gets faster as the purity of the substrate increases, i.e. there is a small amount of alloying elements in the substrate. Further, alloying elements affect the thickness and the morphology of the boride layer.
During boronizing, called also boriding, the surface layer of material is saturated with boron. The process is performed in solid, liquid or gaseous medium and is applicable to any ferrous material as well as to alloys of Ni, Co or Ti. In case of steel it is carried out at temperatures between 840 and 1050°C for up to 10 h creating borides FeB and Fe2B, which have a needle-like structure and hardness reaching 2000 HV.
In addition to improving wear resistance, boronizing enhances also the corrosion resistance and oxidation resistance at temperatures of up to 850°C. The main disadvantage of boronizing is the brittleness of the compound layer, especially the FeB phase.
Boronizing is applicable to titanium alloys and a pack process at 950°C creates a compact, uniform layer composed of TiB2 and TiB compounds. Also, boronizing of pure nickel in powder-pack at 850-950°C for up to 8 h creates the 237 µm thick surface layer composed of Ni2B, Ni5Si2 and N2Si phases with a hardness exceeding 980 HV. The laser boronizing of nodular iron increases hardness five times and produces the fine-crystalline, homogeneous structure of iron borides. The commercial boronizing TitancoteTMB generates a diffusion layer of complex borides with a thickness of 10-200 µm and hardness of 1600-1800 HV with applications in tooling, oil, gas or general components. In addition to titanium, also other refractory metals such as tantalum, niobium, tungsten and also cobalt-chromium alloys benefit from boronizing. One of many advantages is increasing the surface strength without negatively affecting a biocompatibility.
In the paper of T.Popela and D.Vojtĕch is analysed the boride layers on Ti-46Al, Ti-46Al-8Nb and Ti-46Al-8Ta alloys by powder-pack boronizing technique. The process of boronizing was optimized concerning setting of the temperature and duration of boronizing and the composition of boride powder as well.
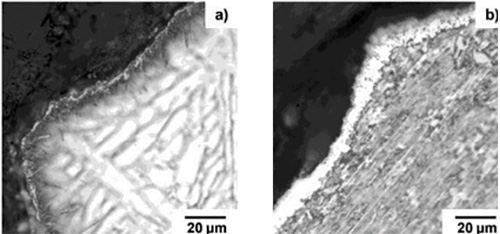
Figure 1: Optical micrographs of boronized layers on the Ti-6Al-4V alloy boronized at: (a) 950°C and (b) 1150°C for 12 hours. As can see in the Figure 1a after treatment a boride layer on the sample was created. However, this layer was very heterogeneous and had insufficient thickness to fully protect the base metal. It is generally known that increase of the boronizing temperature speed up the diffusion of boron into the metal and, therefore, leads to formation of thicker boride layer. Based on this knowledge, another boronizing treatment was tried with temperature of 1150°C and time 12 hours. The result can be seen in the Figure 1b. In this case, the layer is sufficiently thick and homogeneously covers the whole metal specimen.