Abstract
Rapid slurry formation (RSF) is a novel semi-solid metal forming technique which allows complex geometries to be formed in a single operation.
Advantages of RSF include a much reduced suspension preparation time and cost and most importantly the ability to achieve a globular structure and high fluidity of suspension at the same time.
Rapid slurry formation is a semi-solid metal forming technique, which is based on a so-called solid enthalpy exchange material (EEM). It is a fascinating technology offering the opportunity to manufacture net-shaped metal components of complex geometry in a single forming operation.
The RSF process differs from other rheocasting processes because heat extraction and temperature control are not necessary. The RSF process is based on enthalpy exchange of two alloys where one alloy is the low superheat melt (high enthalpy).
The other one acts as the cold solid stirring material (low enthalpy) and is also known as enthalpy exchange material (EEM). During the process the EEM is submerged into the melt while stirring action is applied. Heat is absorbed from the melt during stirring operation, and the two alloys with different enthalpies will form a new alloy system with a new enthalpy level.
RSF technology is able to extract a very large amount of heat through enthalpy exchange of similar material in a very short time. This also improves the castability of the alloy significantly. The reason being that through RSF technology, the morphology of the primary phase changes from coarse dendrites to near globular, which eliminates the feeding problem during solidification that is associated with conventional casting method.
The advantage of the method is that the relatively low solid phase fraction (20-30%) provides for achieving a globular structure with simultaneous retaining the high fluidity of suspension, and the preparation of the suspension is much shorter and cheaper than for other methods.
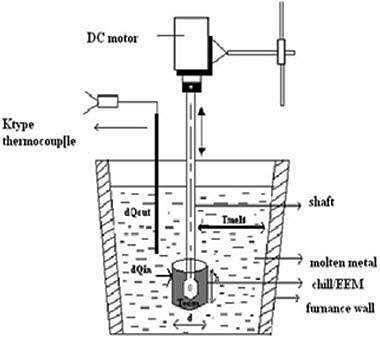
Figure 1: Schematic diagram of heat exchange during slurry formation in RSF process Figure 2(a) exhibits the typical as-cast structure of A 357 alloy where highly dendritic α-Al phase is present. Whereas Fig. 2(b-f) show semi-solid structures of A357 alloy at different rpm. One can see change in dendritic morphology of α-Al in semi-solid structure. This improves the castability of the alloy significantly. The reason being that through RSF technology, the morphology of the primary phase changes from coarse dendrites to near globular, which eliminates the feeding problem during solidification that is associated with conventional casting method.
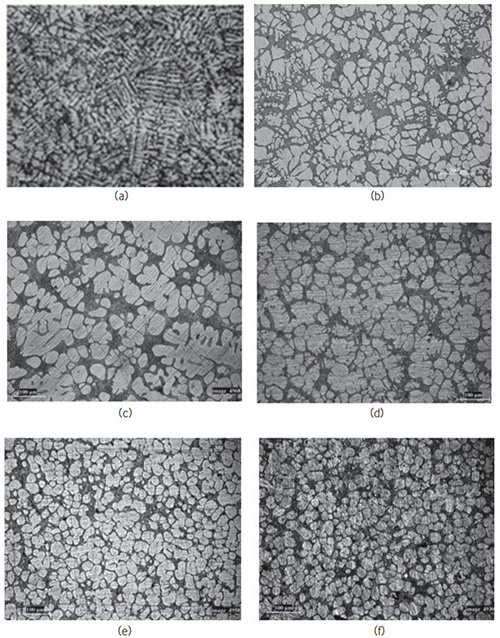
Figure 2: Optical Microstructures of A357 alloy at different rotation speed: (a) 0 rpm, (b) 450 rpm, (c) 800 rpm, (d) 1200 rpm, (e) 1400 rpm and (f) 1800 rpm