Abstract
Lightweight aluminum alloys, long studied by metallurgists and prized by aircraft makers, continue to be improved, more recently by the careful addition of lithium. The results could save fuel and extend the lives of aircraft.
In part two of this series we learn what held this technology back for decades. We also see how two new alloys measure up against a legacy aluminum.
Lithium-containing aluminum alloys have generated much interest in the aerospace industry because lithium additions to aluminum can decrease the density and improve the stiffness compared to conventional aluminum alloys of comparable strength.
Aluminum-Lithium alloy development
The first patents concerning the use of Al-Li alloys were issued in the US in 1927 to Czochralski after the publication of a binary equilibrium diagram. Assman conducted an exhaustive survey of binary, ternary, and quaternary lithium alloys in 1926, but he failed to find any major benefits because of an unfortunate selection of aging conditions and a lack of cold working prior to artificial aging.
During the period of expansion in development of Al-Li alloys in the US, more fundamental studies were being conducted in the UK. Silcock identified the precipitation sequence in binary and Al-Cu-Li alloys, and detected the presence of δ' (Al3Li)-phase, a fact that remained largely ignored until the late 1960s. Jones & Das examined heat treatments and compositional effects on mechanical properties and microstructure (14), with the aim of improving ductility.
The use of Alcoa aluminum-lithium (Al-Li) alloys in aerospace applications began in the late 1950’s with alloy 2020. In the 1980’s, Alcoa’s alloy 2090 and other 2nd generation Al-Li alloys were developed. However, these alloys did not receive widespread use due to their anisotropy, low toughness, poor corrosion resistance and manufacturing issues. Recent developments have produced a new generation of Al-Li alloys which provide not only density and weight savings, but also many improved properties, such as excellent corrosion resistance, good spectrum fatigue crack growth performance, a good strength and toughness combination and compatibility with standard manufacturing techniques. This results in well balanced, lightweight aluminum alloys.
A paper by C. Giummarra et al. discusses two aluminum-lithium alloys for aerospace applications, 2099 and 2199, including the relationship between their alloying elements and thermal-mechanical processing, and the alloy’s properties. The paper also discusses the benefits when these new alloys are applied to an aircraft.
Alcoa has developed a number of Al-Li alloys with these benefits, such as 2199 sheet and plate for fuselage and lower wing applications, respectively, and 2099 extrusions for internal structure. The development of such alloys, in conjunction with involvement from aircraft original equipment manufacturers (OEM) such as Bombardier, has to lead to the new alloys being more refined and closely matched to the needs of OEMs for a given aircraft program or application.
Alcoa and Bombardier’s recent cooperation on these alloys began in 2005 with development studies for the C-Series aircraft. A new plane requires improved alloys that can offer lower weight, improved performance and longer life. The exact properties required for the alloy depend very much on the aircraft size, mission specifications, design drivers and technical requirements. Thus, the close collaboration between Bombardier and Alcoa allowed for the development of the most appropriate alloys and tempers in the timeframe required.
Development Background
Alloy Development 2099 and 2199 are two new Al-Cu-Li alloys which have been developed by Alcoa over the past several years. The composition of these alloys as registered with the Aluminum Association is listed in Table 1.
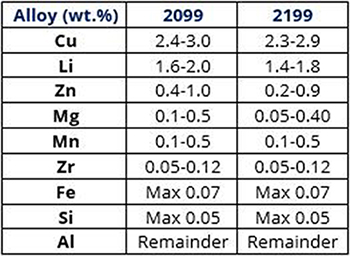
Table 1: Aluminum Association Registered Composition (wt. %) for 2099 and 2199.
2199 plate was tested in the range of 12.7 to 38.1mm (0.5 to 1.5 in.) thick in two T8 tempers, T8E79 and T8E80. Based on these results, minimum properties have been estimated and can be seen in Table 2. Also listed in Table 2 for comparison purposes, are the properties for 2024-T351 plate which is the incumbent lower wing skin alloy used by Bombardier.
Compared to 2024, the 2199 plates have lower density, significantly better stress corrosion and exfoliation corrosion resistance, significantly better spectrum fatigue crack growth performance, better toughness, and higher tensile yield and compressive yield strengths. The ultimate tensile strength, bearing and shear strengths for the T8E80 temper are similar to those for 2024, while for the T8E79 temper, these strengths tend to be lower. This reduction in tensile yield strength provides the higher spectrum of fatigue crack growth (FCG) performance. As long as the strength is adequate for the application, the better crack growth performance may be beneficial, as seen in this case. Thus, one of the two tempers of 2199 may be more suitable for a given application, depending on the individual requirements.
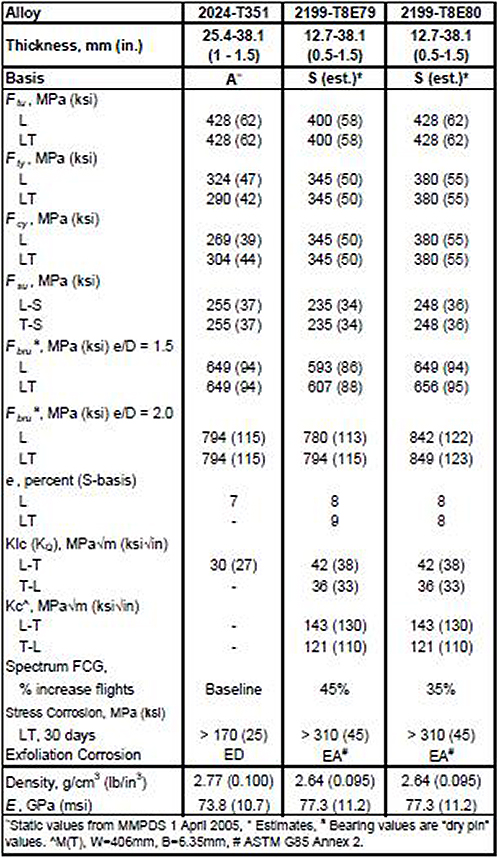
Table 2: Properties for Al-Li 2199-T8E79 and 2199-T8E80 plate compared to 2024-T351.