Abstract
Vacuum brazing is categorized as a technique by its protected sealed environment under vacuum and extremely high temperatures greater than 800°C.
The main advantages of using vacuum brazing include achieving high integrity hermetic joints with minimal distortion.
Vacuum Brazing is an advanced high temperature brazing technique which is performed at high temperatures (›800°C) in a protective atmosphere. Other brazing techniques are soft brazing (‹450°C) and hard brazing (450-800°C). Advantage of high temperature brazing compared to soft and/or hard brazing is that a joint is created with higher strength and higher quality, without using fluxing agents. Because of that, no undesired surface reactions will appear and the parts remain very clean and bright after the brazing process. Also the parts, after the high temperature brazing process, can be hardened with almost every hardening technique like carburizing, nitriding, nitrocarburising or vacuum hardening. It is even possible to do the hardening and brazing in one process.
To achieve a good joint using any brazing process the following conditions must be met:
• The part must be properly cleaned prior to brazing
• The parts must be protected, either by fluxing or atmosphere during heating process to prevent oxidation
The parts must be designed to afford capillary attraction (gap clearance, etc.)
Why Vacuum Furnace Brazing?
Vacuum brazing is usually a high temperature (typically 1700°F/927°C - 2250°F/1232°C), flux less process using nickel-base, pure copper and less frequently precious BFM.
There are several advantages to brazing under vacuum conditions:
• The purity level of the atmosphere (vacuum) can be precisely controlled. Atmospheres of much higher purity can be achieved than can be obtained in regular atmosphere furnace, in effect; there is less residual oxygen to contaminate the work piece.
• The vacuum condition at high temperature results in a decomposed oxides layer, and by doing so improves the base metal wetting properties. Improved wetting will result in better joint properties (e.g. increased strength, minimum porosity, etc.)
• Reduced to a minimum distortion because all parts are heated and cooled uniformly at precisely controlled heating/cooling rates.
• Repeatability and reliability of the brazing process in modern vacuum furnaces, ideally suitable for Lean/Agile manufacturing system.
Vacuum Brazing Equipment
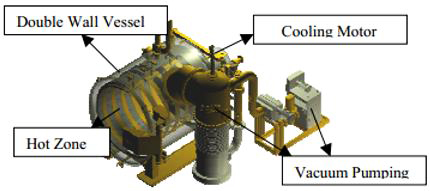
Figure 1: Vacuum Brazing Furnace Assembly
Two types of vacuum furnaces are available in the industry depending on material used for construction of hot zone. The choice of hot zone construction (heating elements and insulation) depends on the vacuum level requirement, compatibility with base material and braze filler metals, temperature requirements, and cooling speed.
The Special Benefits of Vacuum Brazing
• Clean and bright parts and assemblies
• Hermetic joints of high integrity
• Metallurgic consistency
• Numerous braze alloys available: nickel, copper, silver, gold, etc.
• Bond strength
• Minimal distortion
Filler Metals for Vacuum Brazing Services
• Nickel alloys
• Silver alloys
• Pure metals
• Copper alloys
• Gold alloys
• Precious metals
• Silver alloys
Application
Vacuum brazing for:
• Fuel Cell Brazing Technology
• Marine applications
• Aircraft applications
• Stainless steel, age harden for the food industry
• Other industry
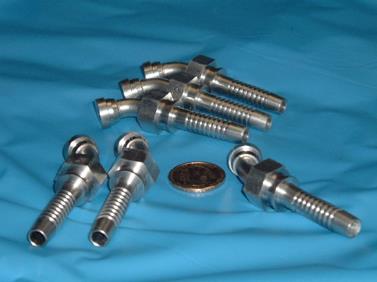
Figure 2: Vacuum brazing product