Abstract
In typical EAF systems around 45% of input energy is lost through slag or off gas, the latter representing 70% of the complete loss of input energy.
The expert furnace system optimization process attempts to tackle this issue by allowing a real time assessment of the energy lost through off gas and to allow plants to react quickly and therefore keep this loss to a minimum.
A typical Energy Balance for a modern EAF confirms that ~ 45% of input energy is lost either with the slag, in off-gas or in the furnace cooling system. Importantly, ~70% of these energy losses are associated with the off-gas roughly split 50/50 between chemical energy in the form of uncombusted CO & H2 and thermal energy.
It is well known that continuous off-gas analysis is an important tool in understanding EAF energy efficiency. Because it provides immediate information, off-gas analysis is essentially like a “flashlight” allowing operators to first, see the real-time “in-EAF” energy dynamics of the current practice and second, how best to optimize and control the practice to improve energy efficiency.
Off-gas analysis is effective for determining if an EAF is operating in an overly reducing condition (insufficient post combustion) or an overly oxidizing condition (often too much fume suction or excessive O2 lancing). As explained below, ideally EAF off-gas chemistry should be adjusted to a moderately reducing condition to achieve the highest energy efficiency, highest yield, most productive, lowest cost operation.
The Expert Furnace System Optimization Process (EFSOP) is a dynamic control and optimization system for chemical energy usage in the electric arc steelmaking furnaces (EAF); based on real-time measurements of off-gas composition taken at the fourth hole of the furnace. The principle components of the EFSOP system are the patented water-cooled sampling probe located upstream at the fourth hole and heated line, the off-gas analysis and purging system and the EFSOP HMI.
The EFSOP patented probe is unique in the industry being the only design to survive the harsh environment and the intense conditions at the combustion gap.
The off-gas chemistry for a typical reducing EAF contains significant quantities of uncombusted CO and H2. The chemical energy contained in this gas is extremely high, for example combusting CO to CO2 and H2 to H2O will generate almost 4 times more energy than partial combustion of C to CO. Hence, so called post combustion of a portion of the available CO & H2 “inside the EAF” can represent a significant improvement in overall energy efficiency and correspondingly reduce both burner and electricity inputs.
The EFSOP system measures and analyses the off-gas composition (CO, CO2, H2, and O2) at the fourth hole of the EAF in real time, and uses this information for closed loop control (CLC) process optimization. Additionally, off-gas analysis provides useful information to production personnel to help better understand the EAF operation and to reduce overall conversion costs.
The main components are:
- Patented probe
- HMI and SCADA computer
- Gas analyser
Figure 1 illustrates the three main components and how they are integrated into the control of the furnace while Figure 4 shows that full-spectrum off-gas analysis (i.e. CO, CO2, H2, O2 & N2) is a valuable tool for “holistic optimization & control” of the EAF process.
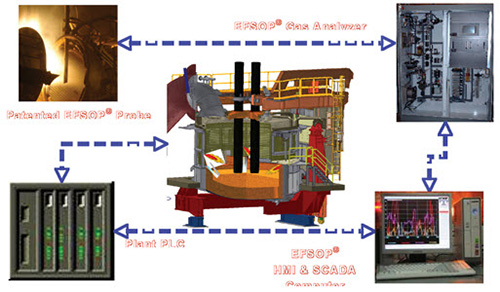
Figure 1: Schematic of the EFSOP system components
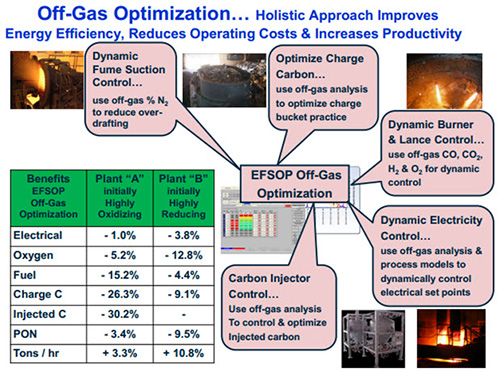
Figure 2: Full-spectrum off-gas analysis (i.e. CO, CO2, H2, O2 & N2) as a valuable tool for “holistic optimization & control” of the EAF process