Abstract
Alonizing or aluminizing is one of many available surface treatments, which helps to improve environmental resistance in steels.
The process effectively diffuses aluminum into the surface of the material, which then provides enhanced protection against elevated-temperature scaling, corrosion oxidation, carburization and hydrogen permeation.
Protective coatings offer the prospect of minimizing material degradation under the severe operating environments commonly encountered in industries such as aerospace, petroleum and chemical industries. Metallic coatings based on Cr, Al and Si, either singly or in combination, have been in use for several decades to enhance environmental resistance of materials to high temperature corrosion, including high temperature oxidation and hot corrosion, particle erosion, erosion-corrosion, wear and thermal degradation.
Alonizing (also known as Aluminizing) is a metallurgical process that diffuses aluminum into the surface of steels and alloys, providing excellent protection against elevated-temperature scaling, corrosion oxidation, carburization and hydrogen permeation.
Simply put it is a thermochemical treatment where the surface layer of a metal is enriched with some metallic element.
The best way found to eliminate scale formation on the heat exchanger tubes is to have the tubes aluminized. Aluminizing can be performed by hot dipping the tube into a bath of molten aluminum, spray metallizing the surface of the tube with aluminum or diffusing aluminum into the surface of the tube. Spraying or dipping results in a layer of pure aluminum on top of the steel. The layer may or may not have voids depending on the condition of the surface of the tubing before aluminizing and the technique used in applying the aluminum. Also, this method results in a condition in which a temperature runway could result in a melting away of the aluminum protection (at temperatures of 1300°F (704°C) or above). Finally, this methods of aluminizing are not capable of insuring the integrity of a coating of inside surfaces of long tubes of small diameter.
The alonizing method overcomes all these difficulties. The process is a pack cementation operation during which aluminum, in a high temperature vapor phase, is diffused into the surface of the tubing. The resultant diffusion zone, since it is not a coating but is rather a true alloy, cannot be lost through accidentally scraping, scratching, abrading or melting away. The diffusion zone, which can protect both the inside and the outside surface of tubing, is about 0.010 “ (0.254 mm) minimum thickness and has an aluminum content on the surface of about 55%, making the tubes impervious to sulfide scaling.
Characteristics of the aluminizing treatment:
- Diffusion thickness: 10 up to as much as 1000 µm
- Temperature resistance: up to 1500°C
- Prevents unwanted diffusion of other compounds such as carbon
- Applicable to all ferrous metals
- Standard maximum dimensions: 3200x2000x900mm, other dimensions on special order
As mentioned above, alonized materials are used most commonly in tubing and piping utilized in corrosive environments. These types of tubing and piping include furnace tubes, reformer tubes, heat exchanger tubes, waste gas heater tubes, line pipe and downhole tubes for wells and production vessels, sulphur condensers and piping used in oil and chemical production and power generation and wrought metal products, bars, rods, plates and sheets, panels, waterwell panels, and wire screens and metal castings by adding aluminum or aluminum and silicon corrosion and erosion preventive diffusion coatings.
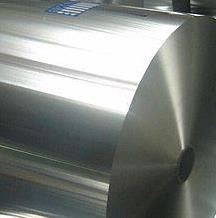
Figure 1: Aluminized steel