Abstract
Industries around the world are seeking to achieve better performance and lighter products with the use of composite materials, but the cost of production with composites pushes the limits of production budgets. Nowhere is this struggle more intense than in the aerospace industry.
But what if a time-tested material could be substantially lightened and improved at the same time? Aluminum alloys, long used and studied by aircraft makers, can indeed be further improved. The results could save more than just fuel and money.
Selecting materials for commercial, military and space-related applications often involves a compromise between performance and cost. The material that will provide the least expensive component while delivering the required performance is usually preferred. The need for a certain level of performance is often dictated by the mission, and this justifies the use of a certain type or class of material.
For example, aluminum alloys have been used extensively for airframe structures. These alloys, both conventional and advanced, were developed for improved mechanical properties so that improvements in aircraft performance could be obtained by reducing structural weight. This can be achieved through reductions in density and improvements in strength, stiffness, durability and damage tolerance. A NASA-funded study by the Lockheed Corporation revealed that reducing the density of aluminum alloys by 7 to 10% could provide cost-effective structural weight reductions when compared to composite materials that have high production costs. These alloys could also potentially provide a unique combination of properties that includes:
1) Decreased densities.
2) Increased stiffness.
3) High yield and tensile strengths.
4) Resistance to the propagation of fatigue cracks.
5) Resistance to exfoliation corrosion.
6) Resistance to stress corrosion cracking.
7) Improved thermal stability.
8) Attractive weight savings, which would help lower operating costs by reducing fuel consumption.
The great potential of aluminum-lithium based alloys as materials possessing higher specific strength and higher specific modulus than the currently established aluminum aerospace alloys has led to intense development activity to enable production of the alloys on a large scale.
Materials Requirements for Aircraft Structures
The requirements for airframe structural materials have changed very little since the early days of aviation, and despite the ever-growing list of secondary requirements, the overriding factors for selection of airframe materials continue to be low density, high strength, and high stiffness. The combination of the 1973 oil crisis and the ever-increasing demands of higher payloads led to a revival of research in the field of high-performance aluminum alloys which continues to this day. Aluminum-Lithium (Al-Li) alloys have three major advantages that put them in a promising position for the future.
Firstly, lithium is the lightest metallic element (density 0.534 gcm-3). Therefore, alloying it with aluminum (density 2.7 gcm-3) lowers the density of the resultant alloy.
Secondly, with the exception of beryllium, whose use is associated with health and manufacturing problems, lithium is the only metal that improves elastic modulus and lowers density when alloyed with aluminum. Wald (5) showed the effect on Young's modulus of adding lithium and other more common metals to aluminum. Every 1 % of lithium added to aluminum increases elastic modulus by approximately 3 GPa and decreases density by approximately 0.08 gcm-3. Alloys based on the Al-Li system are thus capable of high specific modulus and high specific strength, which enables potential savings of weight in aircraft structures-especially when coupled with redesign strategies.
The third advantage of these alloys over materials such as fiber-reinforced composites and titanium alloys is that they can be fabricated by existing equipment. Their behavior is very similar to conventional aluminum alloys when carrying out operations such as extrusion, forging, machining, and forming. Surfaces can be anodically treated or painted and they can also be super-plastically formed under certain conditions. It has also been suggested that lithium-containing alloys may be suitable for moderately elevated temperature uses, which implies that they might be applied in the construction of supersonic aircraft.
PHASE TRANSFORMATIONS IN Al-Li ALLOYS
Al-Li Binary Alloys
The aluminum-rich end of the Al-Li equilibrium phase diagram has been generally agreed to consist of a simple eutectic diagram between a face-centered cubic (fcc) Al-Li solid solution and δ (AlLi) body-centered cubic (bcc) (Figure 1).
Numerous studies have been undertaken to determine the decomposition process in supersaturated solid solutions of the primary α-phase. Initial work conducted by Silcock, using x-ray diffraction techniques, showed the precipitation sequence to be
Supersaturated solid solution → δ'(Al3Li) → δ (AlLi)
Subsequent studies using small-angle x-ray scattering (SAXS), transmission electron microscopy (TEM), and thermal analysis have all confirmed the above reaction sequence. Most of the interest has been confined to alloys containing up to 3.6 wt% (14 at%) lithium, since greater amounts cannot be maintained in solid solution. Spooner et al have reviewed research into the area of the Al-Li phase diagram, and they suggest that the generally agreed position of the δ and (δ' solvus lines is as shown in Figure 1.
If an alloy containing a sufficient amount of lithium is quenched from the solid solution region of the phase diagram and subsequently aged below the metastable solvus, (δ' is precipitated homogeneously in the form of spherical particles. The δ' phase has an ordered Li2 (Cu3Au) superlattice structure; it is fully coherent with the matrix and is in cube-cube orientation with it. As a consequence of the composition of δ', large volume fractions can be produced at relatively low lithium supersaturations, and these coherent precipitates are responsible for age-hardening in the binary system.
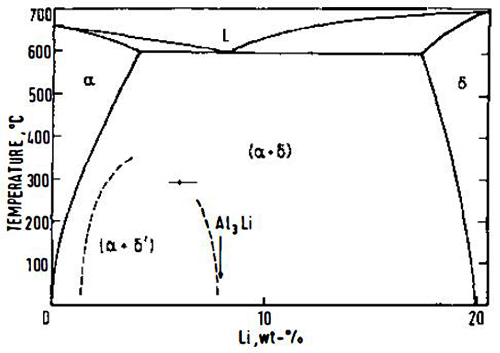
Figure 1: The equilibrium Al-Li phase diagram. Dashed lines represent the metastable δ' (AI3Li) solvus