Abstract
Additive Manufacturing Material Extrusion processes have actually been in existence since the 1980’s and offer a rapid prototyping method to reduce the cost of an otherwise expensive field.
AM-ME can also be known by a number of other names including Direct Ink Writing or DIW, Fused Filament Fabrication or FFF, Extrusion Freeform Fabrication or EFF to name but a few.
In late 1980s Additive Manufacturing Material Extrusion (AM-ME) processes were identified as a part of rapid prototyping or fixtureless manufacturing. The AM-ME process is the one of Additive Manufacturing (AM) process. The AM process is the process of building products by layering a material directly from a Computer Aided Design (CAD) model in a structured manner to fabricate a component or assembly.
Additive Manufacturing Material Extrusion (AM-ME) is a form of rapid prototyping that offers the potential for reduction of cost and time as well as the possibility to create complex structures that are difficult or impossible to machine with common manufacturing techniques.
ISO/ASTM definition: “material extrusion—an additive manufacturing process in which material is selectively dispensed through a nozzle or orifice.”
Material Extrusion can also be known as (in alphabetical order):
- Direct Ink Writing or DIW
- Extrusion Freeform Fabrication or EFF
- Fused Deposition Modeling or FDM® (Stratasys Inc.)
- Fused Filament Fabrication or FFF
- Glass 3D Printing or G3DP
- Liquid Deposition Modeling or LDM
- Micropen Writing
- Plastic Jet Printing or PJP (3D Systems Corporation)
- Robocasting or Robotic Deposition
As Figure 1 shows, the Additive Manufacturing Material extrusion (AM-ME) process is a layering technology where each layer is built from extruded beads of material – typically a thermoplastic. In the AM-ME process, the material is extruded through a nozzle, where it is heated and then deposited in beads placed side by side. The component or assembly is built incrementally, layer by layer. The nozzle can move along the X and Y axes horizontally, and a platform (or deposition head) moves up or down vertically after each new layer is deposited.
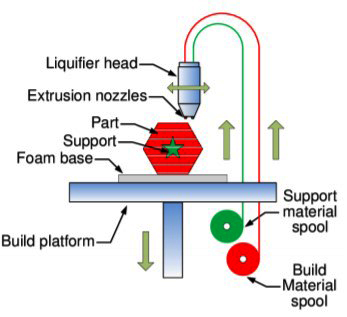
Figure 1: Material extrusion process
The layers are positioned from bottom to top in AM-ME process. For example, the first layer in Figure 2 (a) is built as nozzle deposits material where required onto the cross-sectional area of the cylinder. The following layers are added on top of previous layers. Layers are fused together upon deposition as the material is in a melted state. Figure 2 (b) shows a top view of the last layer which is layer 4. The top view shows how the nozzle had moved during the process, and how the toolpath creates voids. This process is independent of material in AM-ME. The next section explains types of material in AM-ME and names some of them in industry.
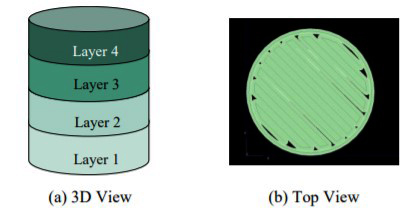
Figure 2: (a) A four-layer cylinder, (b) Top view of the cylinder
There are two types of material in the AM-ME process which are the build material and support material. As it shows, for producing Figure 3 (a), the build material, red part of Figure 3 (b), and the support material, gray part of Figure 3 (c), are used during the process. In the end, the support material is needed to remove from Figure 3 (c) to get Figure 3 (a).
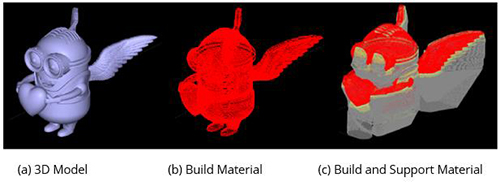
Figure 3: Build and support materials