Abstract
Inert gas soldering can be classified as a system which uses a controlled nitrogen blanket atmosphere and an entry vacuum oxygen/nitrogen exchange chamber.
Some of the main benefits of using inert gas soldering include very low oxide formation, flexibility around flux selection and elimination of post cleaning requirements.
Major features of the Inert gas soldering system include Controlled nitrogen blanket atmosphere, entry vacuum oxygen /nitrogen exchange chamber, PC controlled ultrasonic vaporization fluxer or spray fluxer, conveyor/ wave angle adjustment, motorized solder pot lift, dual wave nozzles attached to conveyor, smart wave, ball bearing solder pot supports for solder pot maintenance external to the system, and extended cool down tunnel for vapor emissions reduction. The particular features that contribute to the success of soldering under a controlled inert gas atmosphere are:
- Soldering takes place in a metallically pure oxide free solder module, oxygen levels are monitored by electrolytes at less than ten parts per million.
- Oxide formation is significantly reduced on the printed circuit boards pre and post soldering as a result of enclosed nitrogen atmosphere, dross formation has been measured to be approximately ten percent of that of a conventional soldering system.
- The systems may operate with either alcohol dicarboxylic acids or low solids (three percent or less) fluxes.
- Post cleaning requirements may be eliminated, leaving an ionic contamination level of less than 20 micrograms/square inch of NaCl equivalent.
Inert atmosphere protects the surface that does not contain any chemical elements that could react with the surface and affect its chemical composition. It has a great importance for soldering, since formation of oxides is well reduced. It follows that the use of inert atmosphere for soldering process is beneficial. Inert gases are used to create an inert atmosphere, for example: nitrogen, argon, hydrogen. A soldering inert atmosphere is often provided by the nitrogen. It is mainly about the availability and economic demands of purchase.
The advantages of the inert atmosphere usage are for example: preventing oxidation of soldered surfaces, better solder spreading, slag reduction, easier cleaning after soldering or fewer defects during soldering of small-pin-pitch components. On the other side, usage of inert atmosphere has also disadvantages, for example: high purchase and operating costs, greater risk of certain defects during soldering – tombstone effect or creation of small solder balls on the PCB (printed circuit boards).
The use of nitrogen to render the atmosphere chemically inert whilst soldering has become a rather common practice. It is widely accepted in the electronic assembly industry that nitrogen 'improves' the wave soldering process; however, its use in reflow equipment is much less frequent, and often questioned. In point of fact, though, hot nitrogen rework tools were introduced at almost the same time as the first nitrogen atmosphere wave soldering equipment.
The main contribution in Novák T. et al. paper was investigation of influence of nitrogen atmosphere on solderability different surface finishes. The test samples had flashes around edges after cutting. Therefore, the samples were ground by a metallographic grinder. The last change of tested samples was the flux application before the measurement. Then the solderability test was carried out. For this experiment, lead-free solder alloy SAC 305 (Sn3Ag0.5Cu) was chosen. The tested parameters were: solder temperature 245°C, immersion depth: 2 mm, immersion time: 10 s, immersion speed: 20 mm/s. When all test parameters were set, there was a need of an inert atmosphere creation around the solderability tester. Test samples have various surface finishes or various metal surfaces. Chosen surface finishes are describe in Table 1.
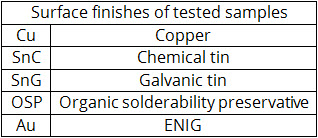
Table 1: Chosen surface finishes The influence of an inert atmosphere is advantage for soldering process that is shown from measured values. It was confirmed that an inert atmosphere created by nitrogen improves surface solderability of tested samples. Figure 4-8 shows that the difference between the wetting force in a normal atmosphere and in an inert atmosphere is considerable. The biggest differences are seen at the surfaces of copper and chemical tin. Conversely, the smallest effect of an inert atmosphere on solderability is seen at the surface of the tested samples OSP and ENIG.
Solderability test showed that decreasing oxygen content in the soldering process improves the surface solderability. This increases the wetting force and the surface tension. It brings the soldering process that ensures a higher quality of solder joints. For the production of electronic equipment, this phenomenon is very important and determines which direction it is possible to head as far as the issue of lead-free soldering is concerned. It also indicates the importance of knowing the solderability of surfaces for production planning in terms of scrap and error rate.
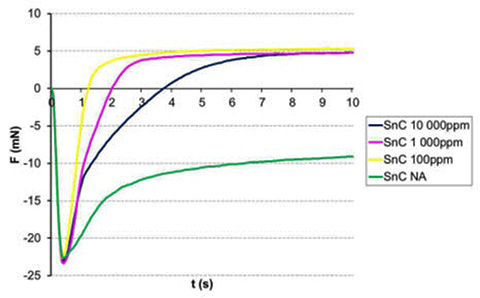
Figure 1: Wetting balance of chemical tin
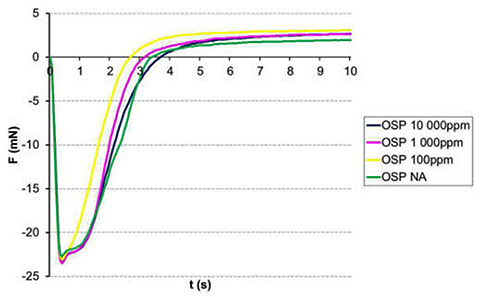
Figure 2: Wetting balance of OSP
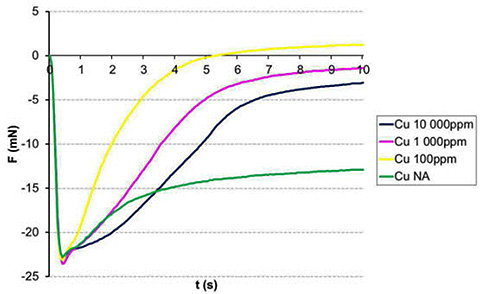
Figure 3: Wetting balance of copper
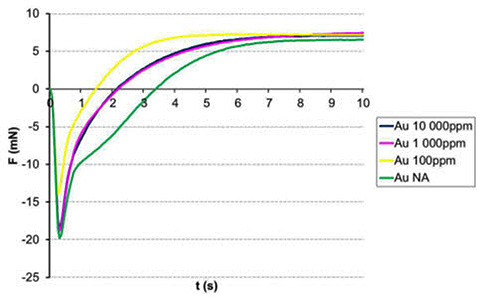
Figure 4: Wetting balance of ENIG