Abstract
Solidification cracks are a serious threat for all types of metallic materials and can appear in several forms, stress/cold cracks or hot cracks or tears.
The main difference between these two main groups of defect is that the cold cracks appear below the non-equilibrium solidus temperature and hot tears above it.
Solidification cracks are a common and serious defect encountered in both ferrous and non-ferrous castings and welds. Many aluminum alloys are susceptible to the two general types of cracks: stress or cold cracks and solidification cracks, otherwise known as hot cracks or hot tears. The essential difference between these two types of cracks is that the former propagate below the non-equilibrium solidus temperature that is in a fully solid material, whereas the latter propagate above it. Hot tears are found to be interdendritic and often discontinuous in nature. They are usually found at a hot spot, i.e. a sudden enlargement in the cross section of a casting or where the heat transfer is reduced locally in the mould. They can also be found near a re-entrant corner of a casting.
On the other hand, hot tears are identified as cracks, either on the surface or internally in the casting. These cracks may be large and visible to the naked eye or small and found only by magnetic particle inspection.
Hot cracks or hot tear is one of the major defects in casting industry, because of the complex mechanisms acting during the solidification of metals, the prediction of the hot tearing phenomenon is not an easy task.
On the other hand, hot tearing is the formation of irregular cracks in a casting that develop during solidification and cooling; typically while the casting is still inside the mold or die cavity. The cause of hot tearing is generally attributed to the development of thermally induced tensile stresses and strains in a casting as the molten metal contracts during solidification and solid state shrinkage. As a result, hot tearing often occurs at inside corners or fillets of casting geometries, where casting shrinkage is constrained by the mold cavity.
In die casting, the mold cavity is a comparatively rigid structure (usually steel), in compared to the relatively low strength aluminum, magnesium or zinc casting alloys at high temperature. One of the key “castability” attributes considered in the development of new metal casting alloys is a low propensity for hot tearing. In addition to casting design features, factors that influence hot tearing include both casting alloy (chemical composition and solidification characteristics), and casting process parameters. Therefore, hot tearing tends to be of greater concern in die casting processes, compared to sand casting processes where the mold cavity is typically lower in strength, and more compliant to casting shrinkage. Hot tearing cracks can be seen via in Constrained Rod Casting (CRC) shown in Figure 1.
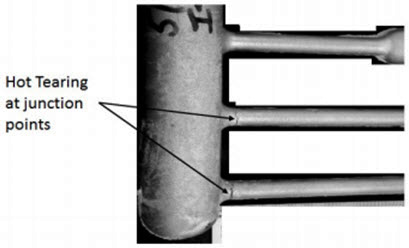
Figure 1: Hot tearing at junction points of constrained rod casting
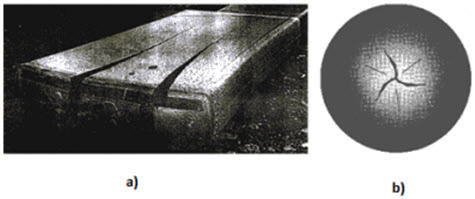
Figure 2: a) Hot tearing in aluminum ingot; b) Hot tearing in extrusion billet As an illustration, Figure 3 shows the typical appearance of hot tearing in the microstructure in an Al-10%Cu alloy. From many studies starting in the 1950s, and reviewed by Novikov and Sigworth, it appears that hot tears initiate above the solidus temperature and propagate in the interdendritic liquid film.
These result in a bumpy fracture surface covered with a smooth layer. In DC casting, the name ‘‘mushy zone’’ is misleading, as its top part is actually a slurry, because the newly formed grains are still suspended in the liquid. Only after the temperature has dropped below the coherency temperature that is the temperature at which grain starts interacting, a real mush is formed. The deformation behavior of the mush is critical for the formation of pores or hot tears. During solidification, the liquid flow through the mushy zone decreases until it becomes insufficient to fill initiated cavities so that they can grow further.
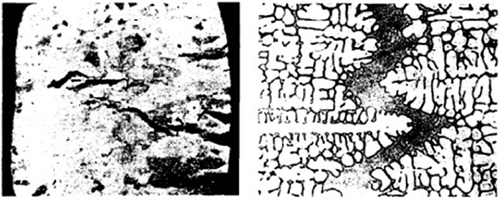
Figure 3: Appearance of hot tears in Al-Cu microstructure specimen Pekguleryuz et al. performed investigation of hot tearing in aluminum alloy AA1050 via Acoustic Emission (AE) and cooling curve analysis methods using a ring mold. The experimental set up for a ring shaped mold is shown in Figure 4. AE method is an approach which can detect the hot tearing using elastic waves. When a specimen is in non-equilibrium, it goes through deformation and results in releasing the elastic strain energy, which is detected as stress waves.
The AE sensor converts the stress wave into a voltage proportional to the magnitude of the stress wave. Also, during plastic deformation of materials, there are many stress waves moving at the same speed, which superimposes (amplifies) these waves, and then it is easy to detect by the AE sensor. Hot tearing information was collected via AE and cooling curve analysis. The aluminum alloy AA1050 has liquidus and solidus equilibrium temperatures of 659°C and solidus 630°C, respectively. The non-equilibrium liquidus ranges from 652 to 659°C. The solidus temperature was 630°C. The non-equilibrium freezing range varied from 43 to 99°C. Hot tearing initiated where the AE energy was over 600 energy units (e.u.) and frequency range was from 110 to 140 kHz in zone II.
Hot cracking occurred when AE energy was over 650 energy units and average frequency range was from 111 to 145 kHz in zone III. Hot tearing occurred at temperature ranging from 636 to 653°C. The solidus ranged from 556 to 614°C as shown in Figure 5. The fraction solid at the onset of hot tearing ranged from 0.71 to 0.99. Addition of Fe in alloys slightly increased hot tearing.
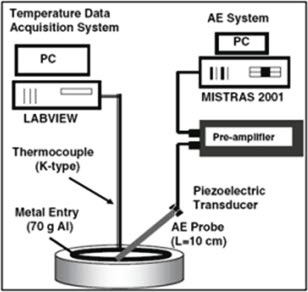
Figure 4: Experimental set up of ring mold casting
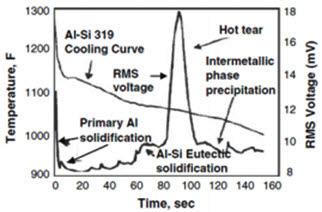
Figure 5: Hot tearing detection via AE method