Abstract
Compacted graphite iron (CGI) represents one of the three main classifications of cast iron based on graphite morphology, alongside lamellar graphite iron and spheroidal graphite iron. CGI offers exceptional engineering properties, with tensile strength and elastic modulus significantly higher than grey cast irons (75% and 35% respectively). This article explores CGI's unique microstructure, mechanical properties, and growing applications in automotive and industrial sectors, highlighting why it has become an increasingly important engineering material that combines optimal strength, ductility, and thermal conductivity characteristics.
Introduction to Cast Iron Classifications
Cast iron encompasses a family of alloys divided into several classes, defined primarily by their graphite morphology and metallic matrix structure. The three principal classifications of cast iron based on graphite structure are:
- Lamellar graphite iron (LGI), commonly known as gray iron or flake graphite iron, featuring graphite shaped as lamellas or flakes
- Compacted graphite iron (CGI), characterized by its distinctive worm-like or vermicular graphite structure
- Spheroidal graphite iron (SGI), also called ductile iron or nodular cast iron, containing graphite in the form of spheroids or nodules
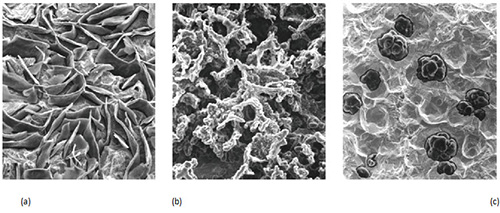
Figure 1: Microstructure of (a) gray iron, (b) CGI and (c) ductile iron
Distinctive Properties of Compacted Graphite Iron
Compacted graphite iron (CGI) has emerged as a promising engineering material due to its unique vermicular graphite form. Its properties position it strategically between grey and ductile irons, offering an optimal combination of mechanical and physical characteristics. Compared to conventional grey cast irons, CGI demonstrates:
- 70% higher tensile strength
- 35% higher elastic modulus
- Nearly double the fatigue strength
These enhanced properties, combined with good thermal conductivity, have attracted significant attention to CGI in recent years. The material has found important applications in automotive engine manufacturing, machine parts production, and various other industrial applications. Casting methods for CGI continue to evolve as manufacturers seek greater control over the final microstructure.
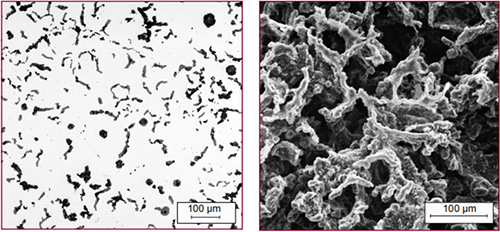
Figure 2: a) CGI microstructure containing 10% nodularity and b) Deep-etched SEM micrographs show the complex coral-like graphite in three-dimensions
Standardization and Specifications
The ISO 16112 international standard provides comprehensive specifications for CGI, establishing five distinct grades ranging from GJV 300 to GJV 500, with minimum tensile strengths from 300 MPa to 500 MPa respectively. According to this standard, proper CGI microstructure must maintain a nodularity range of 0-20%, with flake graphite being unacceptable.
The pearlite content can be adjusted to suit specific applications—GJV 300 Grade is fully ferritic while GJV 500 Grade is fully pearlitic. Like other cast iron variants, CGI can be enhanced with specific alloying elements to improve high-temperature strength, wear resistance, or other properties. Various heat treatments, including austempering, can also be applied to modify the material's characteristics.
While typical chemistry ranges exist for CGI production, the chemical composition is considered secondary to the mechanical properties achieved in the final casting.
Table 1. Mechanical and Physical properties of 10% Nodularity CGI – ISO 16112 should be plac
Property |
Test Method |
Temp (°C) |
GJV 400 |
GJV 450 |
Pearlite Content (%) |
- |
- |
~70 |
>90 |
Ultimate Tensile Strength (MPa) |
ASTME 8M (25°C) ASTME 21 (100°C & 300°C) |
25 |
400-475 |
450-525 |
100 |
375-450 |
425-500 |
400 |
300-375 |
350-425 |
0.2% Yield Strength (MPa) |
ASTME 8M (25°C) ASTME 21 (100°C & 300°C) |
25 |
280-330 |
315-365 |
100 |
255-305 |
290-340 |
400 |
230-280 |
265-315 |
Elastic Modulus (GPa) |
ASTME 8M (25°C) ASTME 21 (100°C & 300°C) |
25 |
140-150 |
145-155 |
100 |
135-145 |
140-150 |
400 |
130-140 |
135-145 |
Elongation (%) |
ASTME 8M (25°C) ASTME 21 (100°C & 300°C) |
25 |
1.0-3.5 |
1.0-2.5 |
100 |
1.0-3.0 |
1.0-2.0 |
400 |
1.0-2.5 |
0.5-1.5 |
Endurance Ratio (Fatigue Limit/UTS) |
Rotating-Bending Tension-Compression 3-point Bending |
25 |
0.45-0.50 |
0.45-0.50 |
25 |
0.25-0.35 |
0.25-0.35 |
25 |
0.60-0.70 |
0.60-0.70 |
Thermal Conductivity (W/m-K) |
Comparative axial heat flow ASTME 1225 |
25 |
39 |
38 |
100 |
39 |
37 |
400 |
38 |
36 |
Thermal Expansion Coefficient (µm/m-K) |
Pushrod dilatometry DIN 51 045 |
100 |
11.0 |
11.0 |
400 |
12.5 |
12.5 |
Poisson's Ratio |
ASTME 132 |
25 |
0.26 |
0.26 |
100 |
0.26 |
0.26 |
400 |
0.27 |
0.27 |
0.2% Compressive Yield (MPa) |
ASTME 9 (medium length) |
25 |
380-420 |
410-440 |
400 |
280-320 |
350-390 |
Fatigue Strength Reduction Factor |
Dependent on notch geometry |
25 |
1.20-1.60 |
1.20-1.60 |
Density (g/cc) |
Displacement (75x25x25 mm) |
25 |
7.0-7.1 |
7.0-7.2 |
Brinell Hardness (BHN) |
10 mm diameter, 3000 kg load |
25 |
183-235 |
207-255 |
Manufacturing Considerations
Modern manufacturing techniques for CGI have developed significantly, with various casting methods now available to producers. The critical aspect of CGI production remains achieving precise control over the graphite morphology, maintaining the characteristic vermicular structure while limiting both nodularity and flake formations. This control is essential for ensuring consistent mechanical and physical properties in the final components.
The balanced properties of CGI make it particularly valuable for applications requiring better strength than grey iron but with better casting characteristics and thermal conductivity than ductile iron. This explains its growing popularity in complex, high-performance components like diesel engine blocks and cylinder heads.