Abstract
The modern method for casting thin strips of steel is efficient and results in a consistent, durable product. The technique might sound simple, but it took more than 100 years to develop. It is now a fast, highly technical way to create a raw material that is close to what the final products require, which saves money for manufacturers. Further developments might have even greater rewards.
The idea of twin-roll casting (TRC) was first patented by Sir Henry Bessemer in 1857. Development of the TRC process took more than 100 years and now it is commercialized for production of both ferrous and non-ferrous alloys, particularly for some special steels.
The twin-roll strip casting process is a near-net-shape casting technology for the production of thin strips having a thickness of between 0.1mm to 6.0 mm. This process produces thin strips directly from the liquid metal by combining casting and rolling in a single step. This process provides better control over the microstructure and mechanical properties of the cast strip. The twin-roll strip casting process is very simple, but there are several complex phenomena involved, like fluid flow, heat transfer, and solidification. The process of twin-roll strip casting is dynamic and quick and occurs at high temperature. The success of the twin-roll strip casting process has led to the elimination of the hot rolling process and made easier the manufacturing of thin strips, which are difficult to hot-roll.
The Strip Casting Process and Its Classification
Near-net-shape casting processes have stimulated increasing efforts for the production of flat products, in terms of both investment and operating costs and greater flexibility and possibility of better material properties in comparison with conventional continuous casting technology. With the aim of achieving good surface quality and high productivity, different types of near-net-shape casting (NNSC) processes have been developed, including the one known as strip casting (SC).
Twin-roll strip casters can consist of either equal sized rolls or unequal sized rolls. These rolls may be arranged horizontally, vertically, or inclined. According to the direction of casting, twin-roll strip casters are divided into two types, which are shown in Figure 1. These are:
(1) vertical twin-roll strip caster (VTRSC),
(2) horizontal twin-roll strip caster (HTRSC).
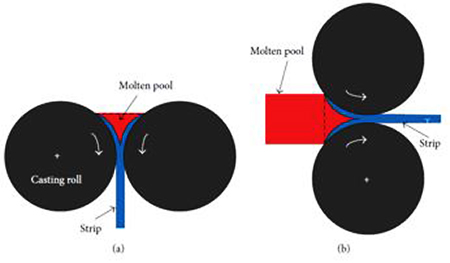
Figure 1: (a) Vertical twin-roll strip caster. (b) Horizontal twin-roll strip caster. In a vertical twin-roll caster, the two rolls are aligned horizontally and the direction of casting is vertical, whereas in a horizontal twin-roll caster, the two rolls are aligned vertically and the direction of casting is horizontal. The ultimate goal of a twin-roll strip caster is to cast thinner, wider, and faster with only microdefects on the strip surface. Casting wider and faster minimizes macrodefects and directly increases productivity, while casting at a reduced gauge is an advantage, in that it can save subsequent cold rolling steps. Based on the comparison of HTRSC and VTRSC, the most typical configuration used in strip casting is the so-called vertical twin-roll strip caster.
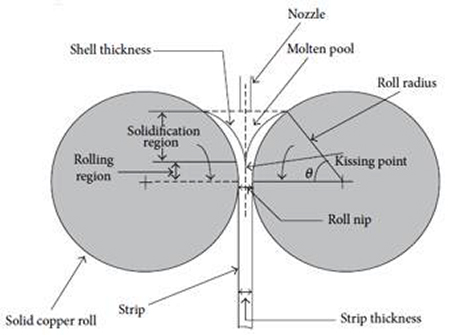
Figure 2: Schematic diagram of vertical twin-roll strip caster.
Principles of Vertical Twin-Roll Strip Casting
The vertical twin-roll strip caster is composed of two equal diameter counter-rotating rolls. The rolls are normally made of high thermal conductivity copper/steel alloys. Their axes of rotation are located in the same horizontal plane. The main equipment used within this process is the crucible, the tundish, the molten metal feeding system (nozzle), and the rolls. In this process, the liquid metal is supplied from the tundish through a nozzle into the wedge-shaped region formed by the two counter-rotating rolls. When the superheated liquid metal comes in contact with the moving rolls, solidification starts with the extraction of heat from the liquid metal to the roll surface and a thin solidified shell is formed on each of the roll surfaces. With the continuous extraction of heat through the moving rolls, the solidified shells gradually grow in thickness. Finally, the two solidified shells contact with each other and weld together at the nip of the rolls (minimum distance between the rolls) and the material exits from the caster in the form of a solidified strip. A more detailed schematic view of a vertical twin-roll strip caster is presented in Figure 2.
Vertical twin-roll strip casting, as a near-net-shape casting technology, shows great potential for an energy efficient production of steel strip:
• The production of advanced high strength steels is simplified by small as-cast thicknesses and an inline hot rolling step. Therefore, the expensive post-processing with re-heating and several rolling passes of conventional production can be minimized and a cost- and energy-efficient hot strip production may become possible.
• A time dendritic a-cast structure is formed by the enormous cooling rates and hence negative segregation effects in highly alloyed steels are significantly reduced.
• Furthermore, the rapid solidification may allow a nanocrystalline or even an amorphous microstructure, thus enabling the continuous production of amorphous steels or metallic glasses.
• By an appropriate process design as used in flexible casting and profile casting, tailored strips with defined thickness distribution can be produced in one single process without any subsequent cold rolling or welding operation.
• Currently, the potential for cladded steel strips by means of vertical strip casting is under investigation, in which a solid strip is introduced in the melt pool, using the high temperatures of the melt for joining two different materials.