Abstract
LaserCusing is a commercial selective laser melting method which as a technology are rapidly emerging as the choice technique for manufacturing low volume, high complexity components.
LaserCusing is different to the similar SLS process in that instead of sintering, the metal powder is directly fused layer by layer and at extremely high density (> 99.7%) which produces excellent mechanical properties.
The demand from industry to gain greater control of customised part manufacture using the combined strengths of computer aided design (CAD) and 3D printing methods has focused interest on additive manufacturing (AM) techniques.
Additive manufacturing (AM) techniques are a group of emerging technologies that have the ability to build 3D parts from bottom up by adding layer upon layer at a time. In this process, information of each layer is taken from a stereolithography (STL) file that is the CAD file sliced in approximated triangles and passed to a 3D printer. Parts being built by 3D printing are becoming more popular in optics industry because it's easy to build light weight components that are very durable.
Selective laser melting, also known as laser powder bed or 3D printing of metal, is a rapidly developing manufacturing technique that enables the fabrication of complex-shaped parts with intricate details. It involves an interaction of a laser beam with powder surface aiming towards achieving parts by melting and fusing of a series of powder layers on top of each other under an inert atmosphere according to a designed model. SLM is an adequate process for the fabrication of optics shutters because it uses laser spot size of 50±500 μm with layer thickness of 20±100 μm which resulted in as SLM part resolution of about 150 μm.
Among the AM methods, selective laser melting (SLM) dominates applications in the industrial and academic sectors. Compared with conventional fabrication routes, SLM offers a range of benefits. The complete melting of the metallic powder particles results in a near-100 per cent dense product without the need for component-specific tooling [3]. This results in reduced production time and maximises material utilisation. Additionally, the layer-by-layer control provides geometrical freedom, and allows the designer to focus more on the functionality of the part than on its manufacturability.
One example of a commercial SLM method is LaserCUSING. The process uses a stochastic exposure scheme based on the ‘island principle’. Each powder layer is divided into ‘islands’ that are laser-scanned, based on a random distribution. It is claimed that this strategy reduces the accumulation of residual stresses caused by steep temperature gradients. The starting material consists of single-component metallic powders generated by an atomisation process, and includes steel, aluminium, nickel-based, titanium, bronze, and precious-metal alloys.
The process
Essentially, the process consists of the following: On a special workbench that is incorporated in the machine, a thin layer of the desired metal powder is automatically evenly spread in the construction chamber. An STL file then enables the laser to only fuse those particles where material must come. Immediately after the fusing by laser, a new layer of metal powder is applied that, in turn, is locally fused to the underlying layer that has already solidified. In this way, you build up a product, layer by layer, and you are not restricted by the complexity of the geometry (see schematic diagram in Figure 1).
Thus, design a component in a CAD program and allow it to be built up in 3D, in order to obtain the end product. In fact, the computer uses special software to convert the three-dimensional file into so-called slices that are, in turn, fused by the machine in order to produce a ‘hard copy’, i.e. an end product.
Oxidation is not a problem because oxygen is not present. The components that it can manufactures using LaserCusing has a maximum size of 350 x 300 x 200 mm, and this takes place inside a construction chamber. The laser beam has a diameter of 0.2 mm and an accuracy of +/- 50 μm. The layer thicknesses can vary between 25 and 100 μm with this having a corresponding effect on the surface roughness.
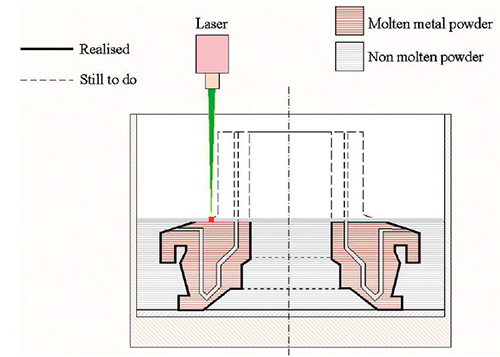
Figure 1: Schematic diagram snapshot of LaserCusing. A cylindrical product with cooling ducts is built up layer by layer. LaserCusing is essentially different from SLS because unlike sintering, the metal powder is directly fused layer by layer, so that you can actually think of this as a kind of minuscule local moulding. This produces high-density (> 99.7%) products that have excellent mechanical properties.
Products produced by LaserCusing (SLM) can also be used as a finished high-quality industrial component and for rapid tooling. The products manufactured with laser, offer a good alternative for smaller series that you have to cast or forge, thus dispensing with the many additional costs associated with constructing casting models, core boxes, the smelting of metal and the time-consuming finishing as well as NC programming.
In the light metal die-casting industry:
- Solve temperature-related mould and mould surface defect problems
- Hot spots avoided
- Increased casting quality (dimensionally/material structure)
- Reduction of cycle time
- Increased tooling lifetime
- Easy repair of crashed cores