Abstract
The iron pelletizing process is a crucial method for upgrading low-grade iron ore into blast furnace-ready material. This comprehensive process involves multiple stages, from crushing and liberation to agglomeration and heat treatment. The process combines iron ore with water and specific binders, which are then formed into uniform pellets through mechanical rolling. This article explores the technical aspects of iron pelletizing, including raw material preparation, process parameters, and quality control measures, highlighting its significance in modern steel production.
Introduction to Iron Ore Processing
The major raw material in the iron and steel industry is iron ore, which is classified as either high-grade or low-grade based on its Fe content. High-grade iron ores, which can be directly used in blast furnaces, are not sufficiently abundant in Earth's crust to meet the demands of the iron and steel industry. The exploitation of low-grade iron ores becomes necessary after enrichment. These lower-grade ores contain considerable amounts of impurities, including compounds of silica, alumina, calcium, and magnesium.
The Liberation Process
The concentration process requires crushing and grinding for adequate liberation before implementing separation techniques. Liberation is typically achieved at considerably fine particle sizes. Consequently, the concentrate obtained is not suitable for direct charging into the blast furnace or direct reduction plant without converting it into suitably sized agglomerates. The most commonly employed agglomeration technique is pelletizing, where a mixture of iron ore, water, and binder is rolled in a mechanical disc or drum to produce agglomerates (green or wet pellets).
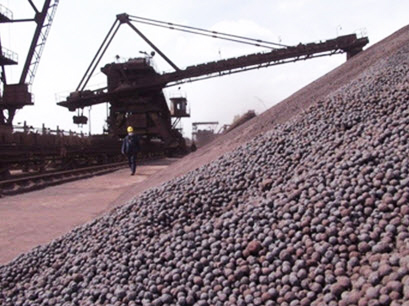
Figure 1: Iron pellets showing uniform size and shape
The Pelletizing Process: Step-by-Step
The pelletizing process contains numerous sub-processes or process segments. From mine to final product, the iron ore undergoes the following main process segments:
- Crushing and Waste Removal: The iron ore is crushed, and waste rock is removed. Approximately 85% of the particles should be less than 44 μm in dimension, enabling the extraction of valuable magnetite.
- Slurry Formation: Water is added to the magnetite to create magnetite slurry.
- Additive Integration: Additive material (dolomite or olivine, depending on the product) is incorporated into the slurry.
- Water Removal: Most water is removed from the slurry using press filters, resulting in approximately 9% water content by weight.
- Binder Addition: After filtering, binder (bentonite or organic binder) is added.
- Green Pellet Formation: Pellets are formed using balling drums. The output is screened, with undersized pellets recycled through the drum and oversized pellets crushed and recycled.
- Drying Process: Correctly sized pellets are transported via conveyor for drying using hot air flow through the bed.
- Heat Treatment: The pellets undergo firing (1250-1300°C) before cooling to approximately 200°C.
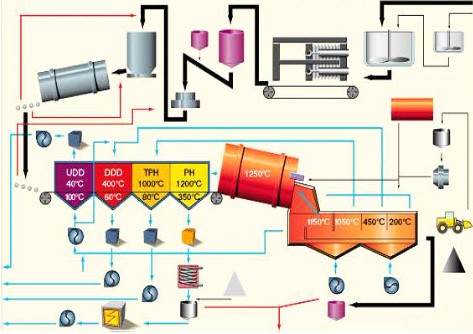
Figure 2: Comprehensive overview of the iron ore pelletizing process
Process Control and Optimization
Several process segments can be operated using classical control techniques, with some operations like slurry formation, additive integration, and binder addition already automated in most modern pelletizing plants. Process success depends heavily on well-functioning preceding segments. Suboptimal performance in any segment, such as inconsistent binder addition, affects subsequent operations, particularly the balling drum operation.
Quality Control and Market Requirements
Market demand is the primary consideration in product development. Critical price parameters include pellet purity and size, with buyers specifying nominal diameters typically between 10-12 mm, plus or minus a small variance. Crushed pellets, while unavoidable to some extent, are highly undesirable for iron mills as they complicate their processes. They represent an economic loss for manufacturers since recycling into earlier process stages is impossible, resulting in a lower-quality product. Excessive crushed pellets often result from high moisture content in green pellets, indicating poor cold process control.