Abstract
The solid-solution hardening of carbon has a major effect on the strength of martensite, but ductility can only be obtained at low carbon levels. Although alloying elements affect hardenability, they have a minor effect on hardness except to reduce it at high carbon levels by causing austenite to be retained.
The solid-solution hardening of carbon has a major effect on the strength of martensite, but ductility can only be obtained at low carbon levels. Although alloying elements affect hardenability, they have a minor effect on hardness except to reduce it at high carbon levels by causing austenite to be retained.
Alternative ways of improving the strength of alloy steels are:
(1) Grain refinement, which increases strength and ductility. This can be developed by severely curtailing the time after the cessation of forging at some low temperature of austenite stability or by rapid heating, coupled with a short austenitising period. Fine grain is produced in 9% Ni steel by tempering fine lath martensite.
(2) Precipitation hardening by carbide, nitride or intermetallic compounds.
(a) By secondary hardening, e.g. 12% Cr steel with additions.
(b) Age hardening a low carbon Fe-Ni lath martensite supersaturated with substitutional elements, e.g. maraging.
(c) Age hardening of austenite, e.g. stainless steels. Phosphorus and titanium are common additions. Stacking faults are often associated with fine carbide precipitates, and strength can be raised by increasing the number of stacking faults (i.e. lower fault energy).
(d) Controlled transformation 18/8 austenite steels in which transformation to martensite is induced by refrigeration or by strain.
(3) Thermomechanical treatments which may be classified into three main groups:
(a) Deformation of austenite prior to the transformation.
Ausforming consists of steel deforming in a metastable austenitic condition between Ac1 and Ms (e.g. 500°C called LT) followed by transformation to martensite and light tempering (Fig. 1). This results in increased dislocation density in the martensite and a finer carbon precipitation on tempering. Strengths up to 1800 MPa can be obtained without impairing the ductility (~6 % deformation). Steels must possess a TTT-curve with a large bay of stable austenite, e.g. 826 M40. Typical application is for leaf springs.
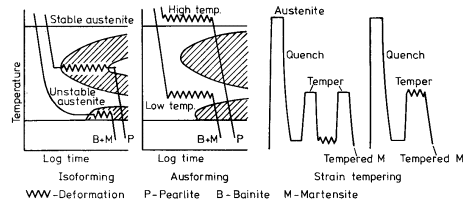
Figure 1. Methods of thermomechanical treatment
Deformation of stable austenite just above Ac3 before cooling (called HT). The properties are somewhat inferior to those produced by ausforming.
Deformation induced transformation originally used in Hadfield 13% Mn steel, but can be adapted to metastable austenitic stainless steels. The fully austenitic steel is severely warm-worked above the lowest temperature at which martensite is produced during the straining. The distinctive property is the high rate of straining hardening, which increases ductility.
(b) Deformation of austenite during the transformation
Isoforming is the deformation of a steel (e.g. 1% Cr) during the isothermal transformation to pearlite, which refines the structure and improves fracture toughness (Fig. 1). A somewhat similar thermomechanical process can be used in the bainitic region, producing bainite and martensite.
Zerolling consists in forming martensite by deformation at subzero temperatures to strengthen 18/8 austenitic steels. The amount of martensite is influenced by alloy composition and increased with deformation and lowering of the temperature.
(c) Deformation after the transformation of austenite
Marforming consists of deforming the maraging steel in the soft martensitic condition, generally cold. There is a pronounced increase in strength of the subsequent maraged product. With other steels, considerable increases in strength can be obtained by straining martensite (~3 %) either in the untempered or tempered condition. A strengthening effect also occurs on re-tempering, probably due to the resolution and reprecipitation of the carbides in a more finely dispersed form.
Strain tempering and dynamic strain ageing
Both processes involve about 5% deformation at the room temperature between two stages of tempering -- strain tempering -- while in dynamic strain ageing deformation is concurrent with tempering.