Abstract
Smart coatings provide a new approach to the important and established topic of protective coatings to protect metallic materials from external environmental influence such as corrosion.
Smart coatings go further by reacting and consequently performing in response to a range of external stimuli such as temperature, UV light, and pH changes.
By definition, corrosion is the physico-chemical metal-environment interaction, which causes changes in the characteristics of the metal and thereby leads to deficiency of the role of the metal, the media, or the system involving both of them. When the perfection of the material is influenced by an external action from the environment, it may become necessary to protect it from this unfavorable action. Introduction of coatings is the most suitable solution to protect the metallic surfaces.
The protection of metals and alloys with coatings is regarded as a hot topic for materials science for many years. Furthermore, over long periods, varying the rules that govern both environmental problems and human health worries imposed intense limitations on the use of dangerous compounds such as Volatile Organic Compounds, Hazardous Air Pollutants, and use of Chromium(VI). As a common example, Chromium-containing compounds used in coatings are known to be toxic and carcinogenic; consequently, recent regulations impose strong limitations in future use of chromium containing compounds aiming to a great effort in fabrication of chromate-free coatings. These limitations, and the absence of alternative materials able to achieve all technical needs, procure to the development of new coating systems. Great research efforts for the investigation of new smart and green coatings for corrosion protection have been carried out. The developments of low-Volatile Organic Compounds, low-Hazardous Air Pollutants, and non-toxic coatings, able to provide efficient corrosion inhibition, have been being investigated to provide smart coatings.
Coatings are designed to provide long-lasting protection against most chemical aggressive environments. There are different reasons for the failure of a coating: misapplication, defects, or simply a long period of exposure to aggressive elements, e.g. high temperatures, light, acids, etc. Furthermore, with the exception of a few coatings, most of them are permeable to the water to some degree. In fact, during its service life, the properties of the coating will eventually change as a result of the penetration of the water, oxygen and other aggressive species through the coating. In addition, defects or the combination of mechanical damage resulting from the impact of solid objects may lead to the formation of microcracks on the coating surface, providing pathways by which the aggressive species may diffuse towards the metal surface. Whatever the reason, the failure will eventually lead to disbonding of the coating and flake formation from the metal coating interface (Figure 1).
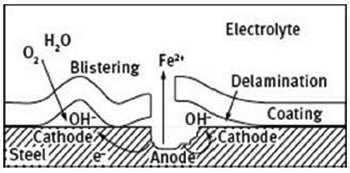
Figure 1: Schematic illustration of the blistering and delamination mechanism Maintenance and repair of the damaged coatings are known to be very expensive, especially on large structures, e.g. offshore oil rigs, ships, etc. Moreover, the conventional repair procedures are generally time consuming and it is mainly appropriate to repair the external damage rather than the internal microcracks. Dry and Sottos performed the first successful attempt at a self-healing material in 1993, using fibres as healing agent carriers. In 2001, White et al. published in Nature a landmark paper entitled “Autonomic healing of polymer composites” with the first successful attempt at an encapsulated healing agent combined with a dispersed encapsulated catalyst agent within a polymeric matrix. In the last few decades, as witnessed by the increasingly number of scientific papers, textbooks published and four international conferences on self-healing materials held in Netherlands (2007), USA (2009), UK (2011) and Belgium (2013), self-healing materials have become an intense field of research. Since then, different approaches have been researched and tested; to date the most common approach and the most successful is the one proposed by White and Sottos, which involves the encapsulation of a self-healing reagent within microcapsules incorporated in the coatings (Figure 2).
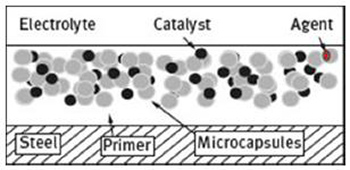
Figure 2: Schematic representation of the microcapsules incorporated within the coating matrix The encapsulation of reactive agent has been widely used in the agriculture, food and pharmaceutical industries as a delivery device. In the context of corrosion protection it has proved to be an effective means of increasing the life-span of the coating, enhancing the compatibility of the active agent with the coating matrix and sustaining, prolonging and controlling the release rate of the agent itself. In particular, as will be discussed later, the process of encapsulation has proved to be very useful in the case of corrosion inhibitors because it allowed coating scientists to solve some problems related to their chemical activity and solubility in water.
This new class of coatings are commonly referred as “smart coatings” due to their ability to respond to physical, chemical or mechanical external stimuli, namely temperature, UV light, and pH changes, and they can be considered as an alternative mean to further enhance the corrosion protection and thereby the durability of metallic structures. Based on the type of microcapsules content, three major release mechanisms were proposed:
- mechanical rupture of the microcapsule wall,
- diffusion through the wall, and
- erosion.
In mechanical rupture, upon rupture resulting from microcrack or sudden damage of the coating, the encapsulated self-healing agent is released into the damaged region, and by acting as a healant prevents further propagation of the crack, allowing the recovery of the barrier property of the coating (Figure 3). In particular, corrosion inhibitor microcapsules present all of three mechanisms above mentioned, depending on the type and final use of the coating. The release can be achieved either upon rupture of the capsules themselves or by localized pH changes as a result of the corrosion process. Changes towards acidic and alkaline pH may lead the inhibitors either to diffuse through the shell of the capsule into the coating or by a spontaneous leakage due to the erosion of the embedded capsule. In both cases the released agent can react with the environment, forming a thin protective layer on top the metal surface. There are basically two different methods to incorporate the microcapsules into the coating, mostly depending on the final use of the coating: blending them within coating matrix, or electrolytically co-depositing the microcapsules on the substrate with metal ions in order to produce metal-matrix composites (MMCs) (Figure 4).
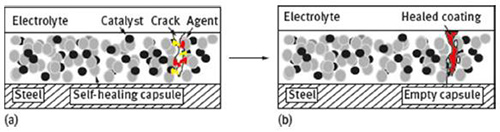
Figure 3: Schematic representation of self-healing coating; (a) before and (b) after healing
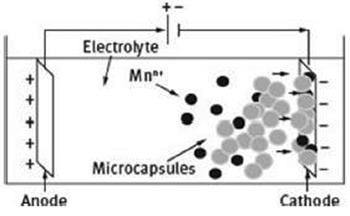
Figure 4: Schematic representation of the microcapsules incorporated within the coating matrix applied by electrolytic codeposition with metal ions