Abstract
Selective laser sintering (SLS) was one of the first additive manufacturing techniques, developed in the mid-1980s and was adapted over time to be applicable for practically all structural materials such as plastics, metals, glass, ceramics, and composites.
A key advantage of the SLS technique is that post-processing requires minimum time and therefore it can be classed an efficient option for industrial application.
Unlike other methods of 3D printing, SLS requires very little additional tooling once an object is printed, meaning that objects don't usually have to be sanded or otherwise altered once they come out of the SLS machine.
SLS doesn't require the use of additional supports to hold an object together while it is being printed. Such supports are often necessary with other 3D printing methods, such as stereolithography or fused deposition modeling, making these methods more time-consuming than SLS.
Part Recovery and Post-Processing
Selective laser sintering post-processing requires minimal time and labor, and leads to consistent results for batches of many parts.
After a print job is complete, the finished parts need to be removed from the build chamber, separated, and cleaned of excess powder. This process is typically completed manually at a cleaning station using compressed air or a media blaster.
SLS parts have a slightly rough, grainy surface finish right out of the printer similar to a medium grit sandpaper.
Post process options include:
• Polishing
• Dyeing
• Impregnation (water-proofing)
• Spray painting (individual colors)
• Shot peening
The most commonly used materials for SLS:
• Aluminum-Filled (PA12-AL)
• Carbon Fiber Filled Nylon (Windform XT)
• Flame Retardant Nylon (Duraform FR100)
• Glass-Filled Nylon (Duraform GF)
• Impact-Resistant Nylon (Duraform EX)
• Nylon (Duraform PA)
• Rubber-Like (Duraform Flex Plastic)
Advantages of SLS:
• SLS parts have good, isotropic mechanical properties, making them ideal for functional parts prototypes;
• SLS require no support, so designs with complex geometries can be easily produced;
• The manufacturing capabilities of SLS is excellent for small to medium batch production.
Disadvantages of SLS:
• Only industrial SLS systems are currently widely available, so lead times are longer than other 3D printing technologies, such as FDM and SLA;
• SLS parts have a grainy surface finish and internal porosity that may require post-processing, if a smooth surface or water tightness is required;
• Large flat surface and small holes cannot be printed accurately with SLS, as they are susceptible to warping and oversitnering.
Application
The application of selective laser sintering is based on two key advantages:
- Production without prior preparation, because there is no need for tools that use shaping technology;
- Possibilities of object production with complex geometrical characteristics, which can not be produced using traditional production technologies.
Selective laser sintering is a shortest path from a computer model to the real object, so what is the solution for the preparation of test samples, individualized products, tools for design technology, and even small product series. The most important application of selective laser sintering:
- Rapid prototyping (shortened RP - „rapid prototyping“)
- Conception models
- Functional prototypes
- Making tools of complex shape (shortened RT - "rapid tooling")
- Production of small series (shortened RM - "rapid manufacturing")
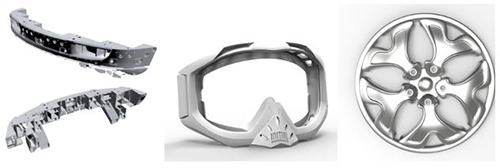
Figure 1: Parts produced/manufactured by SLS process