Abstract
RPV steels are a critical focus of material use in nuclear power plants since their integrity is fundamental to the environmental and safety issues that can be potentially catastrophic in the event of failure.
Exposure to very high levels of neutron irradiation means that embrittlement is a key concern and so great focus is put onto the correct chemical composition of the steels to ensure the correct properties are exhibited to combat these extreme conditions.
The Reactor Pressure Vessel (RPV) is one of the most important components for the safety of nuclear power plants. It contains the reactor core and the reactor coolant, which is regarded as irreplaceable and highly critical for environmental and obvious safety factors. Relating to the materials themselves the RPV is exposed to extreme neutron irradiation which makes the RPV steels susceptible to embrittlement.
The safety goal is to avoid catastrophic failure of the RPV and this can only be achieved using a structural integrity evaluation based on fracture mechanics to ensure sufficient margin against failure during transients. RPV embrittlement has been an issue for over 50 years but it is only in the last 20 years or so that dramatic improvements in microstructural techniques have enabled development of mechanistic insight that can be used to underpin predictions of properties of the RPV during service.
Pressure vessels for light water reactors (LWRs) are designed and fabricated in accordance with the requirements in consensus codes that are based on mechanical and physical properties of the steels used to construct the vessels. In the absence of radiation damage to the reactor pressure vessel (RPV), fracture of the vessel is difficult to postulate because the fracture toughness of the RPV in the unirradiated condition is generally very high at and above room temperature. However, exposure to high-energy neutrons can result in embrittlement of radiation-sensitive RPV materials. The degrading effects of neutron irradiation on carbon and low-alloy pressure vessel steels have been recognized and investigated since the early 1950s. In those steels at LWR operating temperatures [~520–570°F (~270–300°C)], radiation damage is produced when neutrons of sufficient energy displace atoms; the displacements result in displacement cascades, which produce large numbers of vacancy and interstitial-type defects. Although the inside surface of the RPV is exposed to neutrons of varying energies, the higher-energy neutrons produce the bulk of the damage. In a typical LWR, the flux of such high-energy neutrons (> 1 MeV) is from about 1013 to 1016 n·m–2s–1.
Figure 1 shows an example for one particular RPV weld with high copper content.
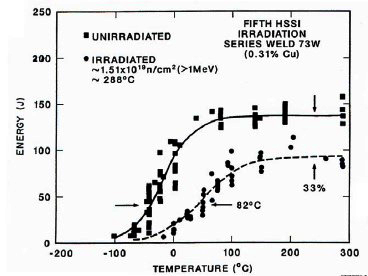
Figure 1: Plot of Charpy impact results showing the effects of irradiation at 288°C to a fluence of 1.5 × 1023 n·m–2s–1 (>1 MeV) on the CVN impact toughness. Table 1 details the compositions and irradiation conditions of the RPV test welds selected for study of S. Connolly, J. Hyde, P. Pareige, D. Parfitt, P. Styman, and K Wilford. The welds were annealed at 920°C for 6 hours and then water quenched, tempered at 600°C for 42 hours, given stress relief at 650°C for 6 hours and finally slow cooled. The samples cover a range of Ni and Cu contents. Samples SH (high Cu) and SL (low Cu) both contain low Ni. Samples WV (high Cu) and 2W (lower Cu) both contain high Ni. The range of compositions for C, Si, Mn, Mo and Cr are low in comparison to those for Cu and Ni. The samples were irradiated at temperatures between 225 and 310°C to doses between 8 and 32 mpda at an accelerated rate in a Materials Test Reactor. Atom maps were used to visually identify the presence of irradiation-induced clusters. Vickers hardness tests were performed on each sample using a 20kg load. The irradiation induced increases in hardness are also detailed in Table 1.
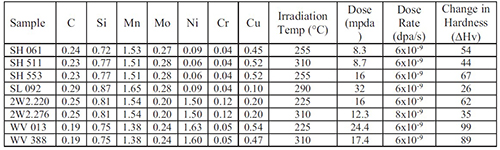
Table 1: Nominal compositions of test weld samples (at%). Balance Fe. They draw next conclusions:
• As the Cu content is reduced, the driving force for clustering decreases. Thus precipitation in SL092 (0.1%Cu, 32mpda) was very much lower than observed in SH (~0.5%Cu, lower dose).
• For both the low and high Ni steels, the higher the bulk Cu content the higher the observed Cu composition of the clusters.
• At lower irradiation temperatures, the clusters appear to contain more Si.
• In generally smaller clusters were observed in the high Ni steels. The exception was the high Ni weld WV388 in which relatively large irradiation induced clusters were observed due to the high irradiation temperature.
• At higher irradiation temperatures the clusters are more developed due to thermal growth.