Abstract
Powder Bed Fusion (PBF) is ASTM standard technological term used to quantify well-known 3D printing techniques such as Direct Metal Laser Sintering, Electron Beam Melting, Direct Laser Melting and Selective Laser Melting.
The main advantages of the PBF techniques include high precision of complex geometries, diverse application using different metal types and advantageous mechanical properties of the finished component.
Powder Bed Fusion (PBF) is the ASTM standard name for 3D printing techniques that build through a bed of powder (Direct Metal Laser Sintering, Electron Beam Melting, Direct Laser Melting and Selective Laser Melting).
Metal parts produced using PBF melting technology are free from residual stresses and internal imperfections, making them ideal for demanding applications found in the aerospace and automotive industries.
The history and categorization of PBF metal 3D printers get a bit messy and it mostly relates to the difference between sintering and melting. The different Powder Bed Fusion methods notably include:
• Selective Laser Sintering (SLS) - SLS 3D printing technology originated in the late 1980’s at the University of Texas at Austin. Over the years, this technology has experienced remarkable advances. Basically, the process uses lasers to sinter, or coalesce, powdered material layer-by-layer to create a solid structure. The final product, rendered enveloped in loose powder, is then cleaned with brushes and pressurized air. The main materials used in the SLS 3D printing process include polyamide (Nylons), Alumide (a blend of gray aluminum powder and polyamide), and rubber-like materials. Nylons are strong and durable but do feature some flexibility, making them excellent for snap fits, brackets, clips, and spring features. Designers should take the susceptibility for shrinkage and warping of thin parts into consideration during the conceptual phase.
• Selective Laser Melting (SLM), also called Direct Metal Laser Sintering (DMLS) - The same technical principle is used to produce Selective Laser Melting (SLM) and Direct Metal Laser Sintering (DMLS) parts, but is exclusively used to produce metal parts. SLM achieves a full melt of the powder so that single-component metals, such as aluminum, can be used to create light, strong spare parts and prototypes. DMLS sinters the powders and is restricted to alloys, including titanium-based alloys. These methods require added support to compensate for the high residual stress and to limit the occurrence of distortion. Applications include jewelry and dental industries, spare parts, and prototypes.
• Electron Beam Melting (EBM) - The EBM 3D printing technology attains fusion with the use of a high-energy electron beam and produces less residual stress resulting in less distortion. It uses less energy and can produce layers faster than SLS. This method is most useful in high-value industries such as aerospace and defense, motor sports, and medical prosthetics.
Difference between Metal Sintering and Melting
Sintering uses a combination of heat and pressure to make particles stick together. Melting uses high enough temperatures to cause the particles to fully melt and join together. Sintered parts have high porosity and require heat treatments to be strengthened, though they’ll never be as strong as forged metal parts; melted parts are nearly fully solid and don’t require heat treatments. In the image below you can see the difference between a sintered and melted part. The particles of the sintered part are simply touching real well but there are large gaps between them throughout the body. In contrary to the melted image on the right. The particles seen are melted and the body is a far more cohesive solid mass with no visible voids.
Figure 1 shows difference in microstructure between sintered and melted product.
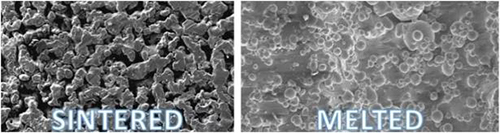
Figure 1: Comparison of the microstructure in sintered and melted product When the German company EOS came up with the term DMLS, they were actually sintering and using the heat treatments afterward, but since then they’ve started using stronger lasers that do fully melt. They just hung on to DMLS term, likely because it was already popular and users don’t like having to remember a dozen different acronyms.
Another difference is that SLM works with a single metal at a time and DMLS works with metal alloys.
The industry uses both terms (SLM and DMLS), nowadays most metal 3D printing companies use a form of melting instead of sintering.
Electron Beam Melting (EBM) uses a high-power electron beam, rather than a laser, to melt the metal powder; electron beams produce more energy and higher temperatures than lasers so they can handle (and are limited to) high-temp superalloys.
Several industries rely on parts created on metal powder bed fusion 3D printers. Medical professionals and surgeons use these 3D printed metals for biocompatible implants, aerospace engineers use them to reduce the weight of aircraft, and industrial manufacturers use them for custom tooling equipment.
Metal PBF Pros
- Nearly any geometry can be fabricated with high precision
- Wide range of metals, including the lightest titanium alloys and the strongest nickel superalloys that are difficult to process with traditional manufacturing technologies
- Mechanical properties are as good as (and sometimes better than) forged metals
- Can be machined, coated, and treated like traditionally-fabricated metal parts
Metal PBF Cons
- High cost of materials, machinery, and operation
- Parts must be attached to the build plate with support structures (to prevent warping) that produce waste and require manual post-processing to remove
- Limited build sizes (though they’re getting steadily larger)
- Handling of metal powders can be dangerous and requires strict process controls