Abstract
Overall magnesium alloys are an attractive prospect for material selection where light-weighting requirements, for example in vehicles, are demanding and stringent to make components lighter without comprising safety.
Twin roll casting provides a processing option to widen the potential application of magnesium alloys in sheet form whilst at the same time retaining the mechanical properties required for such diverse use.
There has been a growing interest in Mg alloys due to their excellent specific strength and stiffness. Such properties of Mg alloys are quite attractive for applications in transportation systems that require light-weight components. Most of the Mg alloys currently in use in transportation systems are cast products. However, Mg sheet products are much needed since they have a larger potential for applications than their cast counterparts. It has been recently shown that the application of twin-roll casting (TRC) can effectively produce low cost Mg alloy sheets with the equivalent tensile properties to those of conventionally processed alloy sheets.
The improvement of mechanical properties of magnesium alloys nowadays is very important, because of the variety of industrial applications. For this goal, the number of casting techniques and further treatments were developed. Among the continuous casting techniques, which allow producing long strips of the alloys, is twin-roll casting. Using this process one can get the magnesium alloy with finest microstructure and higher specific strength.
Different casting techniques are used to produce Mg alloys with the definite properties and to meet specific requirements. Among them are die casting and twin-roll casting (TRC) followed by hot extrusion or hot rolling. Each of the processes affects the texture and microstructure and therefore the mechanical properties of the alloy.
Twin roll casting (TRC) of magnesium alloys becomes more important due to the economic and energy efficient process of manufacturing sheets and strips compared to conventional thin sheet production. Sheets of magnesium wrought alloys, produced via twin roll casting, exhibit good mechanical properties; however, the main drawback concerning their application potential is their low formability at low temperatures. The formability of magnesium wrought alloys is closely related to the resulting microstructure, texture and hcp lattice structure. Improving formability, through grain refinement and texture modification, can be obtained by different approaches: thermomechanical processing, severe plastic deformation such as equal-channel angular extrusion (ECAE), differential speed rolling (DSR) or cross-rolling (CR) and chemical alloying. Processes of severe plastic deformation may be detrimental to cost development and limitations in possible shapes and dimensions. Studies about chemical alloying recommend rare earth (RE) elements as well as Ca, Sr or Li being preferred to influence the texture modification, towards weaker basal or random texture development. Apart from their enhanced formability compared to conventionally available alloys, fabrication of novel alloys via twin roll casting has scarcely been published yet.
The subject of the study in the paper of K. Neh, M. Ullmann, M. Oswald, F. Berge, R. Kawalla was the mechanical properties of twin rolled casting strips of several magnesium alloys containing aluminum or rare earth elements.
Twin roll casting was carried out at the pilot plant of the Institute of Metal Forming at the Technische Universität Bergakademie Freiberg, which is used in cooperation with the Magnesium Flachprodukte GmbH Freiberg. The applied casting system consists of an electrical melting furnace as well as a casting channel and a casting nozzle, which enable the production of magnesium strips with thicknesses between 3 mm and 7 mm and a maximum with of 740 mm. The melt flows from the casting channel into the casting nozzle and hereinafter into the rolling gap, where the material solidifies quickly and is deformed partially. The twin roll cast strip is trimmed into plates or coiled. Water cooled working rolls with a diameter of 840 mm were used. The used magnesium alloys and their chemical composition are shown in Table 1. Besides aluminum containing magnesium alloys, like AZ31, AZ31 with 0.25 wt% SiC and AM50, the alloys with rare earth elements ZE10 (main alloying elements zinc and rare earth elements), ME21 (main alloying elements manganese and cerium) and WE43 (main alloying elements yttrium and rare earth elements) were processed. Characterization of microstructure was conducted by light and scanning electron microscopy. Tensile testing was used to determine the mechanical properties at room temperature. For the identification of liquidus and solidus temperatures to ensure a selection of suitable TRC parameters, differential scanning calorimetry (DSC) was conducted. Different heating and cooling rates of 10 K/min and 20 K/min were used. Twin roll casting was carried out at temperatures between 670°C and 720°C with casting speeds from 1.4 m/min to 1.7 m/min depending, on the chemical composition of the magnesium alloy.
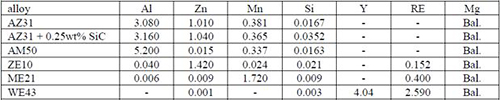
Table 1: Used magnesium alloys with chemical composition in wt% AZ31 with SiC addition and WE43 offer excellent strength in twin roll cast condition (Figure 1). Compared to AZ31 strip without additives or AM50, the yield strength is enhanced from 245 MPa (or 250 MPa for AM50) to 330 MPa. This represents an increase of over 30%. For ultimate tensile strength, improved values from 280 MPa (or 300 MPa for AM50) to 360 MPa are achieved. Grain refinement and a strengthening effect as a result of the SiC addition induce an improvement of the mechanical properties. Higher strength properties of WE43 result from solution and precipitation hardening, especially fine dispersed intermetallic compounds are responsible for improved mechanical properties. But the elongation of all alloys is still insufficient for further processing due to coarse second phases acting as initial points for cracking. The mechanical properties of ZE10 and ME21 are not as high as those of the aluminum containing magnesium alloys. Compared to AZ31 optimized production parameters are required for the Mg-RE-alloys in order to develop a technology for twin roll casting. The insufficient elongations of the twin roll cast strips are improved by a subsequent heat treatment. As a result of the solution of undesirable precipitations and the transformation of the dendritic into one with equiaxed grains the elongation of AZ31 and AM50 is improved from 3.0% and 2.5% to 18% and 22%, respectively.
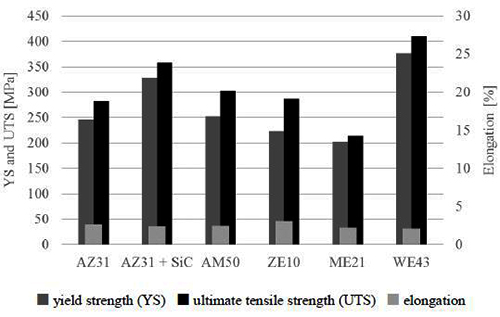
Figure 1: Mechanical properties of the investigated magnesium alloys in twin roll cast condition (0° direction)