Abstract
Additive manufacturing is a relatively recent manufacturing method which has become a key area of interest in multiple industrial sectors.
As the application and growth of AM occurs, several systems to classify the AM processes have developed, including one proposed by the American Society for Testing and Materials (ASTM) F42 Committee.
Additive Manufacturing (AM) comprises a family of different technologies that build up parts by adding materials layer by layer at a time based on a digital 3D solid model. After thirty years of development, AM has become a mainstream manufacturing process with more materials and new technologies involved in this process. Undoubtedly, the most dramatic and challenging development of group of technologies has been the printing of metals. Nowadays, the use of AM for the production of parts for final products continues to grow. Organizations around the world are successfully applying the technology to the production of finished goods. AM allows design optimization and produces customized parts on-demand with almost similar material properties with the conventional manufactured parts. It does not require the use of coolants, fixtures, cutting tools and other assisting resources. The advantages of AM over conventional manufacturing can change the world of industry and lead to a new industrial revolution.
The analysis of today’s AM-business indicates that AM is swiftly growing in significance for many industries as it offers great possibilities to accelerate innovation, compress supply chains, reduce material and energy usage, and waste. In particular, the aerospace industry, which produces geometrically complex high-tech parts in small lot sizes, can benefit from AM’s ability to simultaneously reduce material consumption, and easily create aircraft parts with complex internal structures. Therefore, already today the aerospace industry is in the vanguard of the industrial application of AM. Progressively, AM also holds great promise for the automotive and electronics industry. For instance, vehicle and engines components could be realized using fewer parts and rapidly redesigned to minimize failures. The aerospace, automotive and electronics industry were identified to be promising for the future AM-business.
Various AM processes have been introduced to the commercial market by industrial companies located in different countries (the United States, Germany, Sweden, the United Kingdom, Israel, etc.). There are several systems to classify the AM processes, including one proposed by the American Society for Testing and Materials (ASTM) F42 Committee, which classifies the AM processes into seven areas as shown in Table 1. The AM processes can also be classified based on the state of the starting material used (see Table 2).
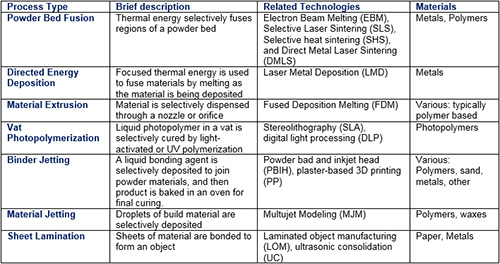
Table 1: The Seven AM Process Categories, as Classified by ASTM F42
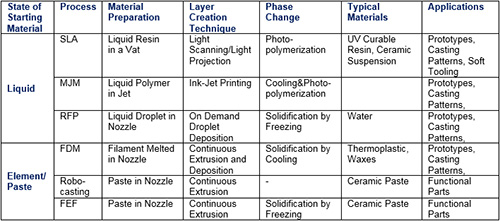
Table 2: Select AM Processes and Working Principles
Key:
SLA = stereolithography; MJM = multi-jet modeling; RFP = rapid freeze prototyping; FDM = fused deposition modeling; FEF = freeze-form extrusion fabrication; SLS = selective laser sintering; SLM = selective laser melting; EBM = electron beam melting; LMD = laser metal deposition; 3DP = 3-D printing; LOM = laminated objective manufacturing