Abstract
Heat treatment can be performed on ductile iron to increase strength, wear resistance, ductility, toughness, and/or improve machinability by controlling the matrix microstructure. In ferrous alloys, an intercritical heat treatment starts with partial austenitization in the intercritical region where ferrite and austenite are present. The amount of austenite depends on the chemistry of the alloy and the temperature.
Heat treatment can be performed on ductile iron to increase strength, wear resistance, ductility, toughness, and/or improve machinability by controlling the matrix microstructure. In ferrous alloys, an intercritical heat treatment starts with partial austenitization in the intercritical region where ferrite and austenite are present. The amount of austenite depends on the chemistry of the alloy and the temperature. After intercritical austenitizing, the material can be quenched in a salt bath to a temperature above the martensite starting temperature (austempering, typically between 230°C (446°F) and 400°C (752°F) and held for a period of time to stabilize the high temperature austenite upon quenching to room temperature.
This heat treatment produces a microstructure of graphite nodules in a matrix of ferrite plus austenite particles, which provides a desirable combination of high yield strength, high ultimate tensile strength and high elongation to fracture. This material is known as intercritically austempered ductile iron (IADI) or dual phase austempered ductile iron. Ductile iron can also be quenched to a temperature below the martensite finish temperature after intercritical austenitizing. In this case, the high-temperature austenite transforms to martensite. After quenching, the material is tempered in order to soften and toughen the hard and brittle as-quenched martensite. The resulting microstructure consists of graphite nodules in a matrix of ferrite plus tempered martensite. In this study, such material is called intercritical austenitized quenched and tempered ductile iron (IAQ & TDI).
The influences of intercritical austenitizing temperatures on microstructures and mechanical properties of austempered ductile irons has been investigated in the paper of K.Chen, J.S.Tsai and B.T.Chen.
A series of intercritical austenitizing temperatures ranging from 775 to 900°C are used and austempering is performed at 300 and 400°C on a conventional unalloyed FCD700 ductile iron. Experimental results show that mechanical properties, including strength, ductility, and the toughness, all increase with intercritical austenitizing temperatures till an optimum austenitizing temperature of 830°C. At this optimum processing condition, strength of 974 MPa, impact energy of 166 J, and 16.4% ductility is achieved. These properties are much higher than non-treated ductile iron with 790 MPa strength, 42J impact energy, and 8.2% ductility. Microstructure refining via well distributed sub-micron ausferrite structure is essential for the increase of strength. Furthermore, the increased carbon content of retained austenite and austenite volume fraction combines to increase toughness through martensitic transformation giving rise to transformation induced plasticity (TRIP) effect.
The microstructure consists of ausferrite (dark) and proeutectoid ferrite (white) with graphite nodules dispersed within the matrix. It is observed that the austenite nucleates at prior ferrite grain boundaries and gradually grows into ferrite regions. Table 2 lists the volume fractions of proeutectoid ferrite, graphite, and ausferrite (containing retained austenite and bainitic ferrite). The amount of proeutectoid ferrite apparently decreases and ausferrite increase with increasing austenitizing temperatures. It is noted that the Ac3 temperatures appear to be around 870°C as proeutectoid ferrite reduces to nearly 0% at this temperature.
Effects of austempering temperature affect mainly the amount of retained austenite and bainitic ferrite. At lower austempering temperature of 300°C, large undercooling leads to more and finer bainitic ferrite as diffusion is limited (Figure 3(a)). On the other hand, higher austempering temperature (400°C) reduces nucleation of bainitic ferrite leading to feather-like ausferrite structures. Figure 3(b) shows that autempering at 400°C gives rise to more blocky retained austenite.
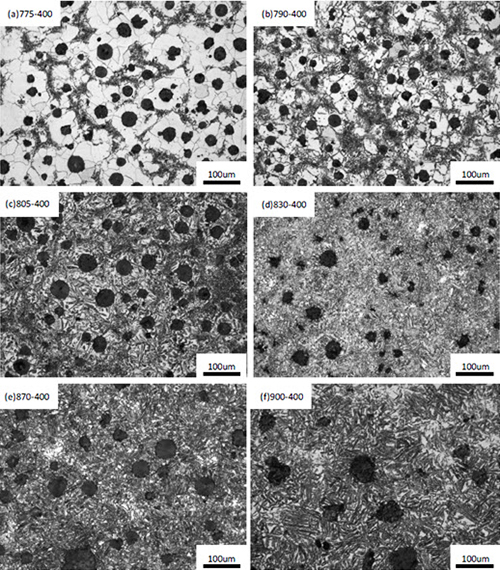
Figure 2: Microstructures of ductile iron austenitized at (a) 775°C, (b) 790°C, (c) 805°C, (d) 830°C, (e) 870°C, (f) 900°C and austempered at 400°C
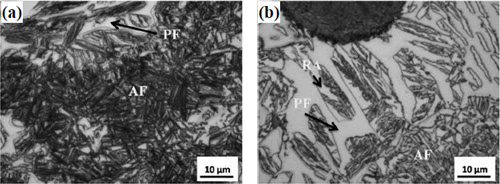
Figure 3: Microstructures of ductile iron austenitized at 805°C and austempered at (a) 300°C (b) 400°C (PF: proeutectoid ferrite, RA: retained austenite, AF: ausferrite)