Abstract
Hydrogen sulfide (H2S) corrosion presents significant challenges in industrial processes, particularly in oil and gas operations. This article examines the electrochemical mechanisms of H2S corrosion on mild steel, focusing on the formation of various iron sulfide scales and their impact on material degradation. The review discusses key prevention strategies, including cathodic protection, galvanization, and chemical inhibition methods, providing insights into their effectiveness in industrial applications. Understanding these mechanisms and prevention techniques is crucial for maintaining infrastructure integrity and operational safety in corrosive environments.
Introduction
Hydrogen sulfide corrosion significantly impacts industrial operations, particularly in the oil and gas sector, where its effects can lead to substantial economic losses and safety concerns. The phenomenon particularly affects mild steel, a material widely used in industrial applications due to its cost-effectiveness and mechanical properties.
Corrosion Mechanisms
The corrosion process in H2S environments is primarily electrochemical, driven by the aggressive dissociation products of hydrogen sulfide. These products catalyze electrochemical reactions, particularly iron dissolution, leading to material degradation. Understanding this process is essential for developing effective prevention strategies.

Figure 1: Proposed mechanism of H2S corrosion on Fe
Surface Scale Formation
A distinctive feature of H2S corrosion is the formation of various iron sulfide scales. Unlike simpler corrosion processes, H2S environments produce multiple sulfide types, including:
- Amorphous ferrous sulfide
- Mackinawite
- Cubic ferrous sulfide
- Pyrite
Mackinawite typically forms first through direct surface reactions, creating a complex corrosion environment.
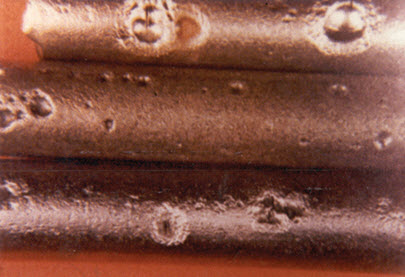
Figure 2: Signs of hydrogen sulfide corrosion include shallow round pits with etched bottoms
Prevention Strategies
- Cathodic Protection
This method involves making the protected material act as a cathode while a sacrificial anode, typically zinc, undergoes preferential corrosion. This technique is particularly effective in pipeline protection.
- Galvanization
This localized protection method involves coating the material with a less corrosion-resistant metal that sacrifices itself to protect the base material. The process creates an electrochemical cell where the coating metal serves as the anode.
- Chemical Inhibition
Chemical inhibitors, such as Catamin AB, provide effective protection by forming protective films on metal surfaces. In high H2S concentrations, these inhibitors work in conjunction with natural iron sulfide layers to prevent further corrosion.