Abstract
Driven by an interaction of mechanical and metallurgical factors, hot tearing is one of the most difficult to control defect issues in casting processes.
Nickel based alloys are widely used and often the material of choice in important applications such as aerospace and power due to their stable and good mechanical properties. Therefore this group of alloys are a reasonable selection for studying their hot tearing tendencies through several informative studies.
Hot cracking, also called hot tearing, solidification cracking or hot shortness is one of the most common and serious defects encountered in many casting processes such as welding and continuous casting. It is particularly difficult to control as it involves an interaction of mechanical and metallurgical factors.
Nickel-based alloys are widely used in industries such as the aircraft industry, chemicals, power generation, and others. Their stable mechanical properties in combination with high resistance to aggressive environments at high temperatures make these materials suitable for the production of components of devices and machines intended for operation in extremely difficult conditions, e.g. in aircraft engines. Nickel-based alloys are used for precision castings and high-pressure castings. The most frequent defects in nickel-based alloy castings are misruns, micro-shrinkage, and cracks. In the case of castings having complex shapes, the number of defective castings can exceed 10%. Defects forming during the casting process and during service can be repaired by welding and pad welding. Unfortunately, the technologies employed to repairs of cast components do not always produce the desired results, which often renders production unprofitable. The main reason for the disqualification of complete structures or individual castings from use are pores and cracks that form during the casting process.
The solidification characteristics and the hot tearing susceptibility were investigated on two Ni-based superalloys for turbocharger turbine wheel, K418 and K419 in the paper of Zhao-xia Shi, Jian-xin Dong, Mai-cang Zhang, Lei Zheng.
The microstructure evolution and solidification characteristics of K418 and K419 alloy were investigated by differential scanning calorimetry (DSC) analysis, isothermal solidification quenching and optical metallographic examination. Hot tearing phenomenon was investigated by analyzing the fracture of the hot crack. A modified Clyne−Davies HTS criterion was proposed to quantitatively explain the different hot tearing susceptibility of the superalloys.
DSC measurement
The chemical compositions of K418 and K419 alloys used are listed in Table 1. It was to be noted that all compositions were given in mass fraction unless otherwise stated here. The samples were taken from the as-received condition bar with 31 mm in diameter, which was produced by conventional manufacturing process comprising vacuum induction melting and casting into steel moulds under a protective argon atmosphere. DSC measurement was performed in a Netzsch testing apparatus (model STA449C) to obtain temperatures of reactions. The heating rate was 20°C/min up to 1000°C, then 10°C/min up to 1450°C.
This was followed by a cooling at 10°C/min down to 1000°C, then 20°C/min down to room temperature. The DSC specimens were cut from the master alloy. All tests were conducted in a purged high-purity argon atmosphere using high-purity alumina crucibles. A baseline was obtained by heating and cooling the crucible without samples according to the experimental method; the effect of the crucible was deducted by subtracting the baseline from the experimental data. The heating curve was used to obtain the solidus, and the cooling curve was used to quote the liquidus. The phase transformations were also monitored on both the heating and the cooling curve, and the average value of the two was considered to be the phase transition temperature. The phase transition temperature was then used to select the quenching temperatures.

Table 1: Chemical compositions of tested alloys in the present experiments (mass fraction, %)
Isothermal solidification quenching
The evolution of microstructure was conducted on isothermal solidification quenched samples. Specimens for isothermal solidification quenching experiment were cylinders of d8.5 mm×7 mm cut from the alloy bars. The sample was sealed by the mixture of silica sol and alumina powders to effectively protect melts from flowing out and oxidation during melting and solidification. A schematic illustration of the isothermal solidification quenching process is shown in Fig. 1. Each sealed sample was put in an alumina burning boat and heated to 1420°C for 20 min to achieve complete melting and homogeneous. The sample was then rapidly quenched into a salt water bath with the concentration of 10% from different temperatures (expressed as Tq) in the freezing temperature interval obtained from the DSC data. The remaining liquid at a given temperature was quenched to offer a convenient method studying the microstructure evolution during solidification.
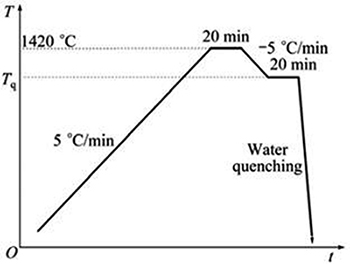
Figure 1: Schematic of isothermal solidification quenching process
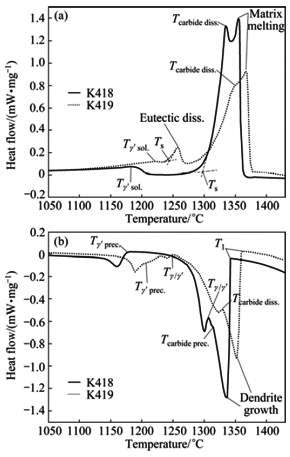
Figure 2: DSC results for K418 and K419 during heating and cooling (Heating and cooling rates both were 10°C/min. The way of obtaining the solidus and liquidus temperatures, Ts and Tl, γ′ solution and precipitation temperatures, Tγ′ sol. and Tγ′ prec., as well as carbide dissolution and formation temperatures, Tcarbide diss. and Tcarbide prec., was indicated in the plot. The other main phase transformations were also marked.)