Abstract
After design of casting technology, pattern making and molding, the existence of the product starts with the melting and pouring process.
A quality heat treatment is the most important sequence besides the chemical composition, to obtain the required microstructure and mechanical properties, as a basis for creep strength.
Today the requirements for the quality of heavy section castings are increasing very rapidly. At the Voest Alpine Stahl Linz Foundry, they manufacture castings for steam turbines in the 1-60 t weight range. Figure 1 shows the main sequences in the flow of production of heavy steel castings for power engineering. After design of casting technology, pattern making and molding, the existence of the product starts with the melting and pouring process. As castings in such dimensions must not have defects which result in scrap, the pouring and solidification process is simulated in computer software during the design phase, in order to locate critical sections for shrinkage (see Figure 2).
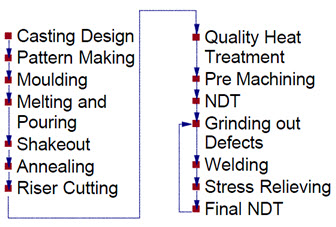
Figure 1: Typical manufacturing plan for heavy steel castings
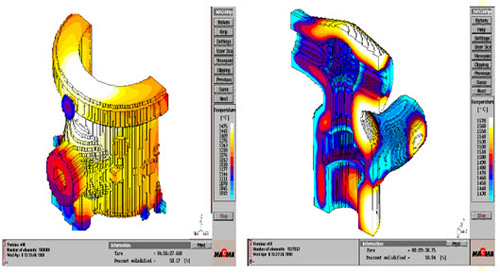
Figure 2: Simulation of solidification of a VHP-Casing and a valve casing, later welded together (G-X 12 CrMoWVNbN 10 1 1) After the time of solidification (approx. 2 weeks) has passed, the casting is shaken out. The handling of the casting in this condition is absolutely critical, because the cast microstructure is highly brittle. Therefore an annealing treatment is necessary for the casting, to stand the high thermal stresses during riser burning. The temperature range in which riser burning is performed, is also critical, as the stresses from the different temperature gradients and the changes in wall thickness in different sections should not be added to the stresses from transformation of the microstructure.
A quality heat treatment is the most important sequence besides the chemical composition, to obtain the required microstructure and mechanical properties, as a basis for creep strength. After pre machining, the casting is examined by non- destructive testing methods (magnetic particle, ultrasonic and radiographic). All indications which do not meet the applied acceptance standard have to be removed by grinding and arc air burning. After magnetic particle testing of the excavations, these are welded, followed by a stress-relief cycle.
Many dimension control sequences are performed between the main production phases, in order to determine whether the dimensions will become critical for final machining or function. Final non-destructive testing is the last sequence in the foundry, before the casting is sent for final machining.
Steam-turbine casings are massive steel castings that encase the internal stationary and rotating components of the turbine. Casings have two critical functions: (1) containing the steam pressure and (2) maintaining support and alignment of the internal components. Cracking of the casing can lead to steam leaks and, in extreme situations, to bursting. Casing distortion can cause damage by allowing contact between the stationary and rotating parts.
The Doosan’s high pressure Steam Turbine casing is a cast steel structure with a verified design and construction to prevent cracks during the casting. After rough machining, the cast steel is subjected to detailed nondestructive inspections of ultrasonic and radiographic tests. The casing flanges are designed to be relatively thick to prevent steam leakage.
The low pressure exhaust hood and inner casing are fabricated from steel plate. Bolted access covers are easy to inspect the internal steam path components. An expansion joint designed into the crossover pipe decrease thermal stresses and distortions for the exhaust hood, and heat baffles welded on the surface of the inner casing prevents heat deformation. All turbine casings have a bolted horizontal joint flange for relatively easy and quick maintenance.
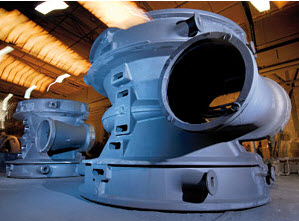
Figure 3: Steam Turbine Casing, 45 t